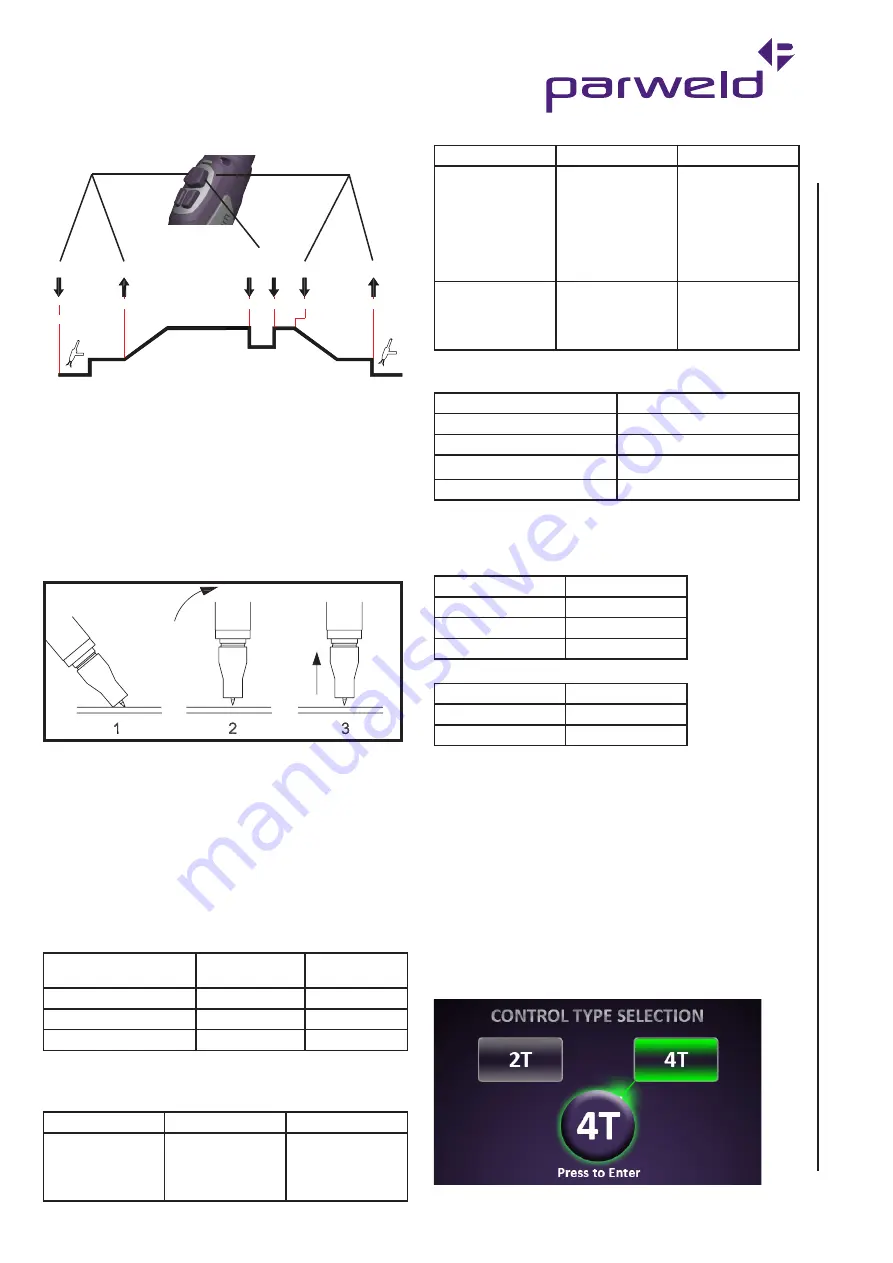
www.parweld.com
15
Step Current, 4T mode
Release
Press
Release
Initial
Current
Final
Current Post Gas
Pre Gas
Press
Tap
Button
7.7.4 TIG Welding Guide
Torch starting in Lift TIG mode
Ensure the gas supply is switched on to the machine. Briefly contact
the tip of the tungsten electrode down onto the work piece with the
torch at around 70
0
from vertical. Depress the trigger to start the gas
flow and switch on the power, lift the torch up from the work piece
to draw out an arc. To prevent melting of the end of the tungsten the
machine will increase the output current when it detects the rise in
arc voltage as the tungsten is lifted from the work piece. At the end
of the weld release the torch trigger and the power will slope down
and switch off.
At the end of the weld release the trigger and allow the power and
gas to switch off before moving the torch from the weld.
Torch starting in HF mode
Ensure the gas supply is switched on to the machine. Hold the torch
with the tip of the tungsten approx 2-3 mm from the job. Depress the
trigger to start the gas flow and switch on the power. At the end of
the weld release the torch trigger and the power will slope down and
switch off.
TIG welding guide ranges
Electrode diameter
AC current
(amps)
DC current
(amps)
0.040” (1.0mm)
15-30
20-60
1/16” (1.6mm)
60-120
75-150
3/32” (2.4mm)
100-180
150-250
Tungsten electrode types
Type
Application
Colour
Thoriated 2%
DC welding of mild
steel,
Stainless steel and
Copper
Red
Type
Application
Colour
Ceriated 2%
DC welding of mild
steel, Stainless
steel, Copper
AC welding
of aluminium,
magnesium and
their alloys
Grey
Zirconiated
AC welding
of aluminium,
magnesium and
their alloys
White
Guide for selecting filler wire diameter
Filler wire diameter
Current range
1/16” (1.6 mm)
20 - 90
3/32” (2.4 mm)
65 - 115
1/8” (3.2 mm)
100 - 165
3/16” (4.8 mm)
200-350
The filler wire diameter specified is a guide only, other diameter
wires may be used according to the welding application.
Shielding gas selection
Alloy
Shielding gas
Aluminium & alloys
Pure Argon
Carbon steel
Pure Argon
Stainless steel
Pure Argon
Nickel alloy
Pure Argon
Copper
Pure Argon
Titanium
Pure Argon
7.7.5 DC TIG welding (No Pulse)
Note:- shorting or dipping the electrode into the weld pool
for more than 1 second will cause the machine to reduce the
welding power to zero in order to protect the tungsten and
minimise contamination.
1) Connect the torch to the TIG torch socket and the gas hose to the
gas outlet.
2) Connect the trigger control plug on the torch to the trigger socket.
3) Connect the Earth lead to the Earth socket.
4) Set the process mode to 2T or 4T if you prefer a latching trigger
action. (Note in 4T position you must press and release to start the
process and press and release again to stop the process).
Summary of Contents for XTM 211Di
Page 1: ...OPERATOR MANUAL ISSUE 1 XTM 211Di ...
Page 27: ...www parweld com 27 ...