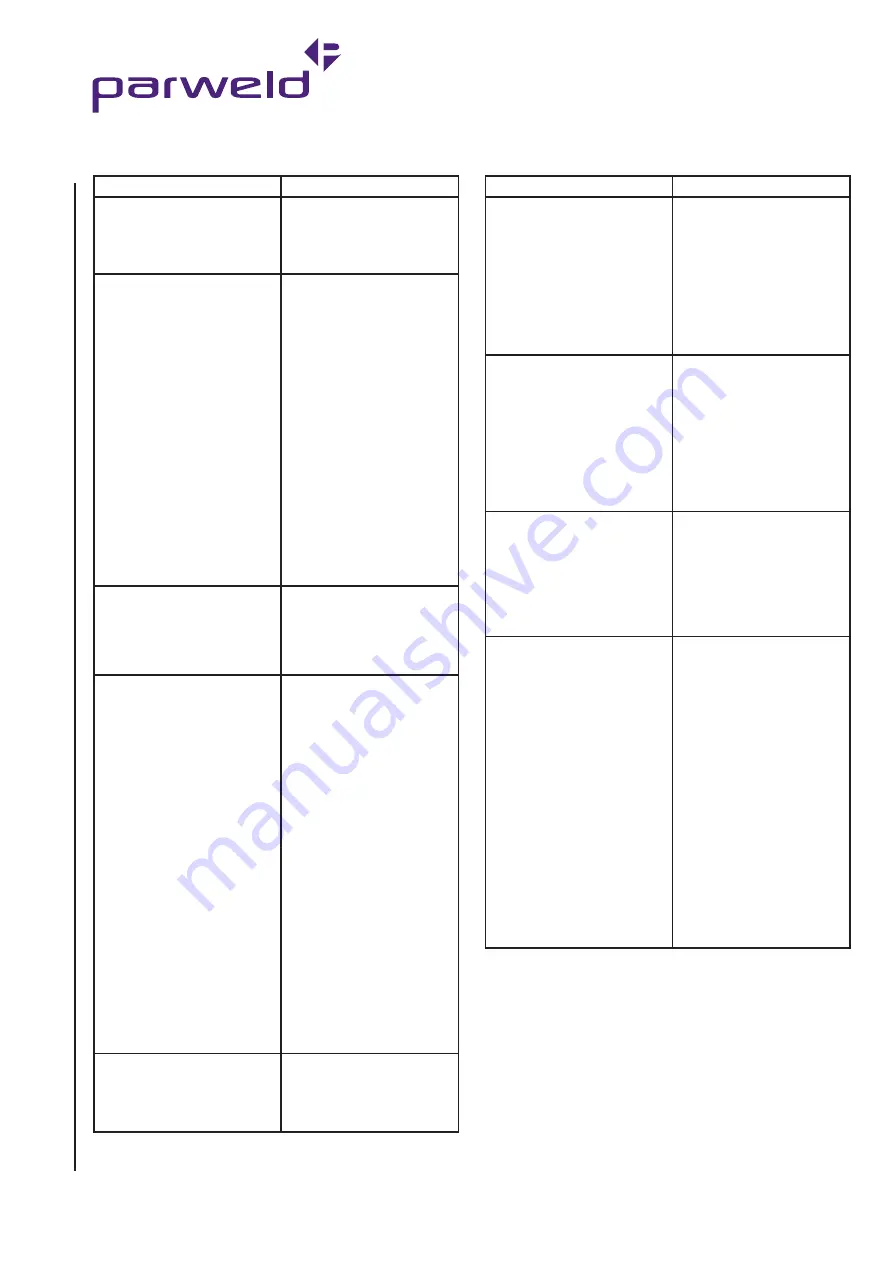
www.parweld.com
20
Problem
Cause/Corrective Action
Excessive Penetration - weld
metal melting through base
metal and hanging underneath
weld.
Excessive heat input. Select
lower voltage range and
reduce wire feed speed.
Increase travel speed.
Lack of Penetration - shallow
fusion between weld metal and
base metal.
Improper joint preparation.
Material too thick. Joint
preparation and design must
provide access to bottom
of groove while maintaining
proper welding wire extension
and arc characteristics.
Improper weld technique.
Maintain normal gun angle of
0 to 15 degrees to achieve
maximum penetration. Keep
arc on leading edge of weld
puddle. Ensure welding wire
extends not more than 13 mm
beyond nozzle.
Insufficient heat input. Select
higher wire feed speed and/or
select higher voltage range.
Reduce travel speed.
Burn-Through - weld metal
melting completely through base
metal resulting in holes where
no metal remains.
Excessive heat input. Select
lower voltage range and
reduce wire feed speed.
Increase and/or maintain
steady travel speed.
Excessive Spatter - scattering of
molten metal particles that cool
to solid form near weld bead.
Wire feed speed too high.
Select lower wire feed speed.
Voltage too high. Select lower
voltage range.
Electrode extension (stick out)
too long. Use shorter electrode
extension (stick out).
Work piece dirty. Remove all
grease, oil, moisture, rust,
paint, undercoating, and dirt
from work surface before
welding.
Insufficient shielding gas at
welding arc. Increase flow of
shielding gas at regulator/flow
meter and/or prevent drafts
near welding arc.
Dirty welding wire. Use clean,
dry welding wire. Eliminate
pickup of oil or lubricant on
welding wire from feeder or
liner.
Wire feed unit operates but no
gas flow .
Gas cylinder empty
Gas regulator closed
Faulty solenoid
Restriction in torch cables
Problem
Cause/Corrective Action
Wire feed unit operates, but
does not feed
Insufficient drive roll pressure
Incorrect drive rolls
Excessive wire spool brake
tension
Incorrect liner
Blocked liner
Bird nesting
Burn back
Bird nesting
Excessive feed roll pressure
Incorrect or blocked liner
Incorrect contact tip size
Contact tip overheating
Restriction in torch cable
Misaligned drive rolls or wire
guides
Excessive cable kinkage
Burn back
Improper voltage setting
Improper stick out
Erratic wire feed
Incorrect or blocked liner
Contact tip overheating
Excessive cable kinking
Erratic Wire Feeding or Arc
Improper drive roll tension
Improper drive roll size
Worn drive rolls
Incorrect or blocked liner
Incorrect wire guide size
Misaligned drive rolls or wire
guide
Gaps at liner or wire guide
junctions
Incorrect contact tip size
Contact Tip overheating
Spatter adhesion on exit
geometry of tip bore
Excessive cable kinkage
Poor earth or cable
connections
Weld joint area dirty
8.1 MIG Welding Problems
(continued)
Summary of Contents for XTM 211Di
Page 1: ...OPERATOR MANUAL ISSUE 1 XTM 211Di ...
Page 27: ...www parweld com 27 ...