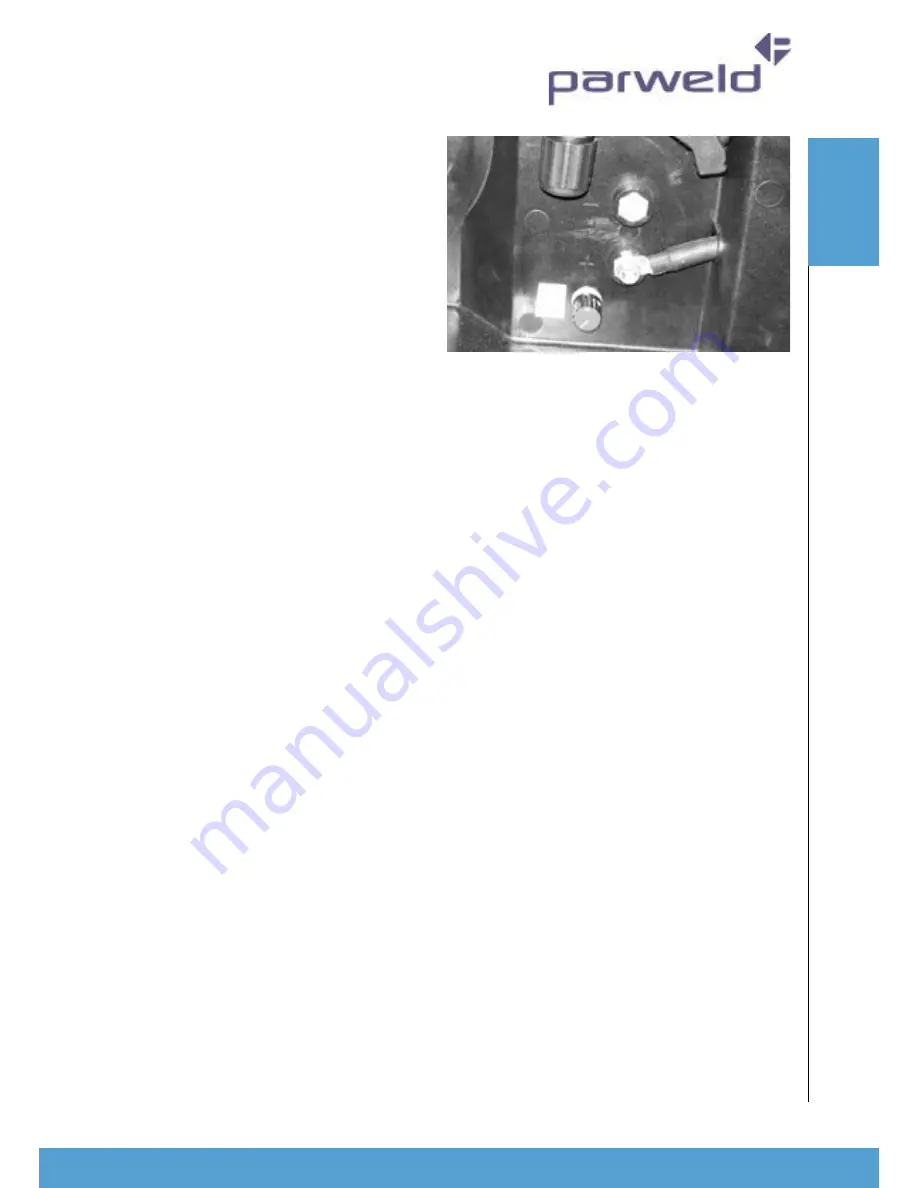
www.parweld.com
www.parweld.com
7
in MMA mode unless the on/off switch is in the off
position.
5.0 Installation
Read entire installation section before starting
installation.
SAFETY PRECAUTIONS
• ELECTRIC SHOCK can kill.
• Only qualified personnel should perform this
installation.
• Only personnel that have read and understood the
Operating Manual should install and operate this
equipment.
• Machine must be grounded per any national, local
or other applicable electrical regulations.
• The power switch is to be in the OFF position when
installing work cable and electrode cable and when
connecting other equipment.
5.1 Unpacking the Machine
Carefully remove the machine from the packaging,
we recommend you retain the packaging until the
machine has been fully installed and tested incase it
has been damaged in transit and has to be returned to
the re-seller.
5.2 Location
Be sure to locate the welder according to the following
guidelines:
In areas, free from moisture and dust.
Ambient temperature between 0-40
0
C.
In areas, free from oil, steam and corrosive gases.
In areas, not subjected to abnormal vibration or shock.
In areas not exposed to direct sunlight or rain.
Place at a distance of 12” (300 mm) or more from
walls or similar that could restrict natural airflow for
cooling.
5.3 Input and grounding connection
WARNING
Before starting the installation, check that your
power supply is adequate for the voltage, amperage,
phase, and frequency specified on the Machine
nameplate.
Operate the welding power source from a single-
phase 50/60 Hz, AC power supply. The input voltage
must match one of the electrical input voltages shown
on the input data label on the unit nameplate. The
XTI-601MP machine should only be used on 230V
supply. Refer to the specifications table for voltage
tolerances.
Have a qualified electrician connect the input plug.
For long runs over 30m , larger copper wires should
be used. The green/yellow wire in the input cable
connects to the frame of the machine. This ensures
proper grounding of the machine when the machine
plug is inserted into the receptacle.
5.4 MIG welding torch setup
The welder, as shipped from the factory, is
connected for electrode positive (+) polarity. This is
the normal polarity for MIG welding. The polarity of
the welding set can be changed for use with gas less
flux cored wires by reversing the polarity connections
inside the wire feed cover .
Referring to the diagram
following which shows the normal connection for Gas
assisted welding. For gasless flux cored wire the wire
should be connected to the (-) output.
5.4.1 Changing drive roll sets
1. Turn off the power source.
2. Release the pressure on the idle roll by pulling the
pressure adjuster towards the wire spool holder.
the. The idle roll assembly should now hindge
down away from the pressure roll.
3. Unscrew the plastic knob retaining the grooved
drive roll and side off the drive roller.
4. Ensure the wire size marked on the side of the
feed roller matches the wire size to be used.
5. Replace the drive in reverse of the above
procedure ensuring the wire size to be used is
marked on the outward facing side of the roller as
it is refitted.
NOTE: Be sure that the torch liner and contact tip are
also sized to match the selected wire size.
5.4.2 Welding wire installation (MIG)
Open the Wire Drive Compartment Door
6. Unscrew the plastic retaining wheel from the end
of the spool holder shaft.
7. Position the wire spool so that it will rotate in a
direction when feeding so as to be de-reeled from
the bottom of the coil.
8. Slide the wire spool all the way onto the shaft and
refit the plastic retaining nut.
O
pera
tIO
n
Summary of Contents for XTI-601 MP
Page 1: ...INSTRUCTION MANUAL...