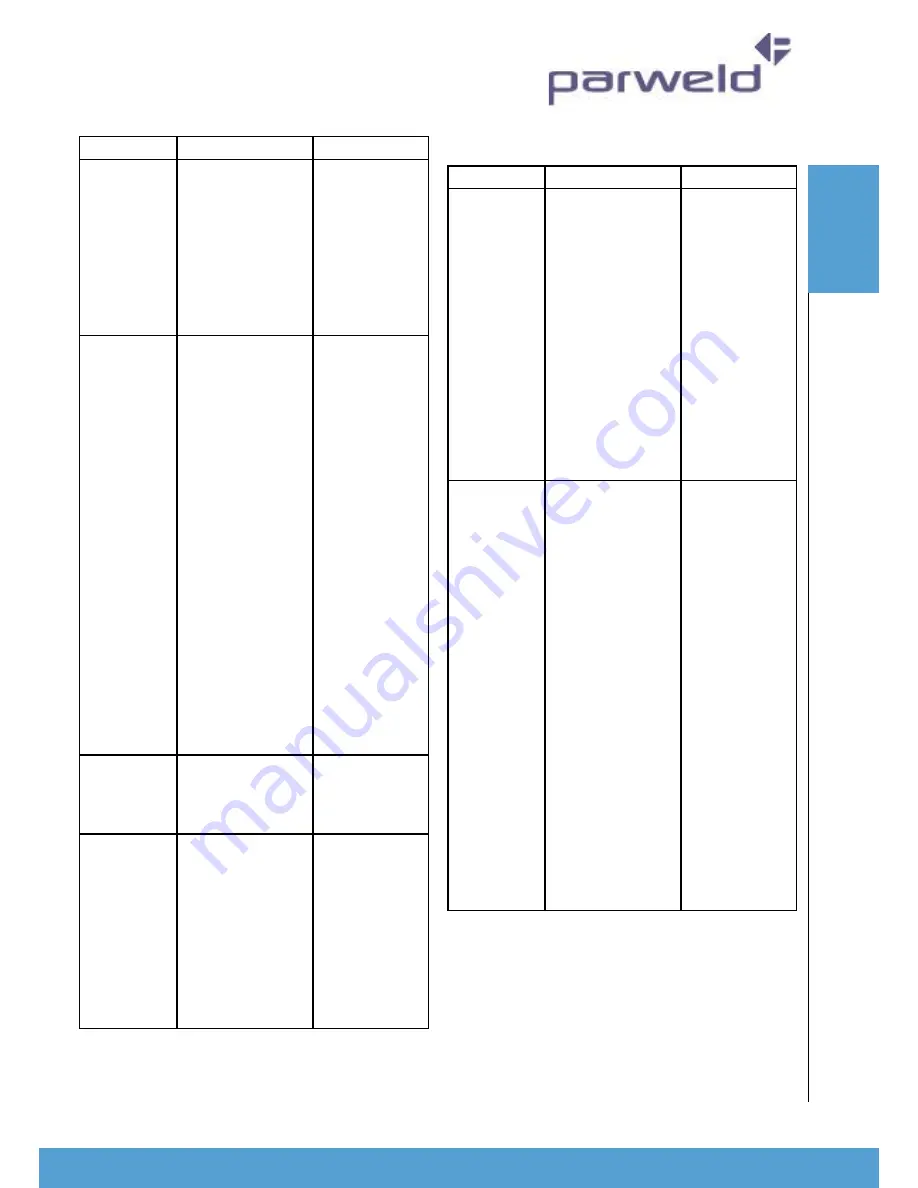
www.parweld.com
www.parweld.com
Description
Possible Cause
Remedy
Dirty weld
pool
(a) Electrode
contaminated
through contact
with work piece or
filler rod material
(b) Gas contami-
nated with air
(a) Clean the
electrode by
grinding off the
contaminates
(b) Check gas
lines for cuts
and loose fitting
or change gas
cylinder
Electrode
melts or
oxidizes
when an arc
is struck
(a) No gas flowing
to welding region
(b) Torch is clogged
with dust
(c) Gas hose is cut
(d) Gas passage
contains impurities
(e) Gas regulator is
turned off
(f) Torch valve is
turned off
(g) The electrode
is too small for the
welding current
(a) Check the
gas lines for
kinks or breaks
and gas cylinder
contents
(b) Clean torch
(c) Replace gas
hose
(d) Disconnect
gas hose from
torch then raise
gas pressure
to blow out
impurities.
(e) Turn on
(f) Turn on
(g) Increase
electrode
diameter or
reduce the
welding current
Poor weld
finish
Inadequate
shielding gas
Increase gas
flow or check
gas line for gas
flow problems
Arc flutters
during TIG
welding
(a) Tungsten
electrode is too
large for the
welding current
(b) Absence of
oxides in the Weld
pool.
(a) Select
the right size
electrode. Refer
to basic TIG
welding guide.
(b) Refer basic
TIG welding
guide for ways
to reduce arc
flutter
Description
Possible Cause
Remedy
Welding arc
cannot be
established
(a) Work clamp is
not connected to
the work piece or
the work/torch
leads are not
connected to the
machine
(b) Torch lead is
disconnected
(c) Gas flow
incorrectly set,
cylinder empty or
the torch valve is
off
a) Connect the
work clamp to
the work piece
or connect the
work/torch
leads to the
right welding
terminals.
(b) Connect it to
the ‘.’ terminal.
(c) Select the
right flow
rate, change
cylinders or turn
torch valve on.
Arc start is
not smooth
(a) Tungsten
electrode is too
large for the
welding current .
(b) The wrong
electrode is being
used for the
welding job.
(c) Gas flow rate is
too high.
(d) Incorrect
shielding gas is
being used.
(e) Poor work
clamp connection
to work piece
(a) Select
the right size
electrode
(b) Select the
right electrode
type. Refer
to basic TIG
welding guide
(c) Select the
correct rate for
the welding job.
Refer to basic
TIG welding
guide
(d) Select the
right shielding
gas. Refer
to basic TIG
welding guide
(e) Improve
connection to
work piece
Faul
t
FI
n
DI
n
G
13
Summary of Contents for XTI-601 MP
Page 1: ...INSTRUCTION MANUAL...