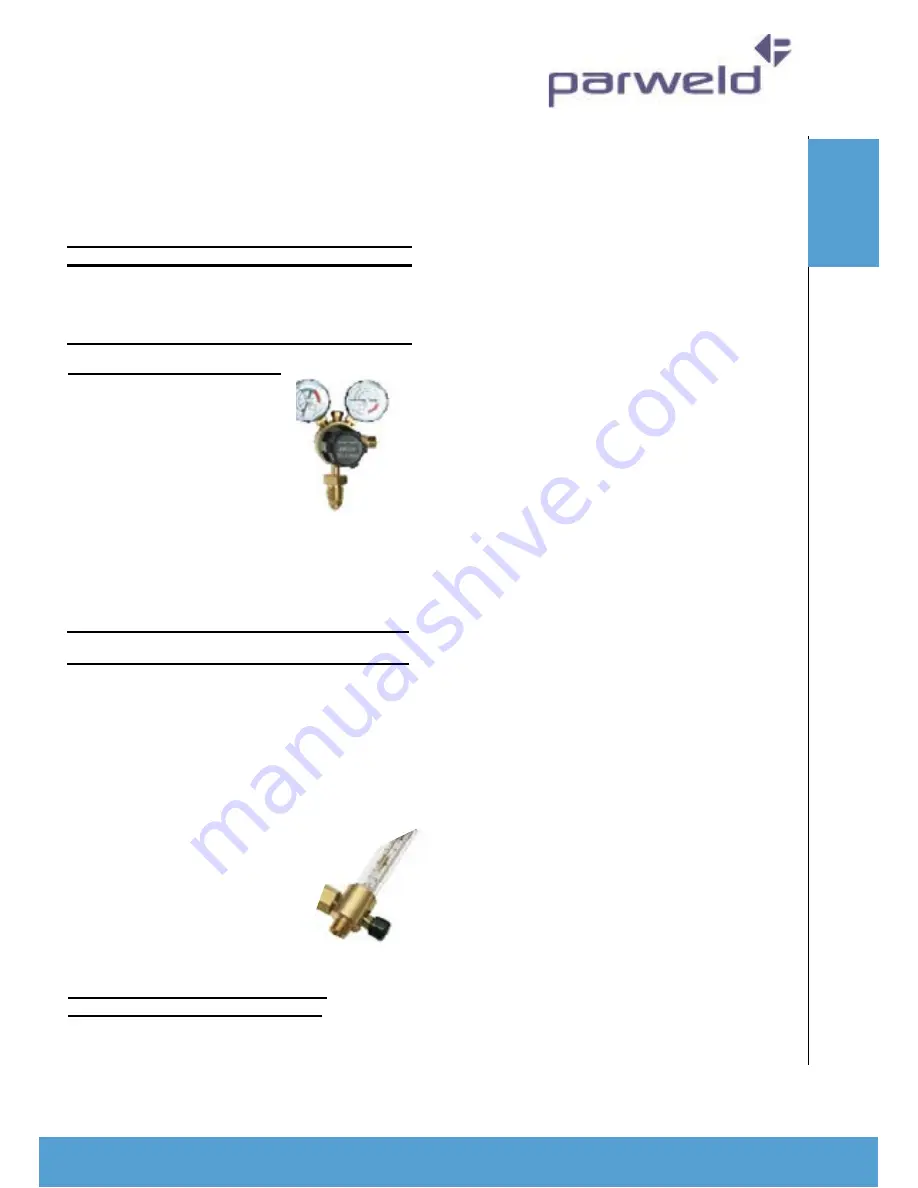
www.parweld.com
15
www.parweld.com
a
CC
eSSO
rY
a
CC
eSSO
rY
9.0 Statement of Warranty
Limited Warranty:
Parweld Ltd, hereafter, “Parweld” warrants its customers that its products
will be free of defects in workmanship or material. Should any failure to
conform to this warranty appear within the time period applicable to the
Parweld products as stated below, Parweld shall, upon notification thereof
and substantiation that the product has been stored, installed, operated,
and maintained in accordance with Parweld’s specifications, instructions,
recommendations and recognized standard industry practice, and not
subject to misuse, repair, neglect, alteration, or accident, correct such
defects by suitable repair or replacement, at Parweld’s sole option, of
any components or parts of the product determined by Parweld to be
defective.
Parweld makes no other warranty, express or implied. This warranty
is exclusive and in lieu of all others, including, but not limited to any
warranty of merchantability or fitness for any particular purpose.
Limitation of Liability:
Parweld shall not under any circumstances be liable for special, indirect
or consequential damages, such as, but not limited to, lost profits and
business interruption. The remedies of the purchaser set forth herein
are exclusive and the liability of Parweld with respect to any contract,
or anything done in connection therewith such as the performance or
breach thereof, or from the manufacture, sale, delivery, resale, or use
of any goods covered by or furnished by Parweld whether arising out of
contract, negligence, strict tort, or under any warranty, or otherwise, shall
not, except as expressly provided herein, exceed the price of the goods
upon which such liability is based. No employee, agent, or representative
of Parweld is authorized to change this warranty in any way or grant any
other warranty.
Purchaser’s rights under this warranty are void if replacement parts or
accessories are used which in Parweld’s sole judgement may impair the
safety or performance of any Parweld product.
Purchaser’s rights under this warranty are void if the product is sold to
purchaser by non-authorized persons.
The warranty is effective for the time stated below beginning on the date
that the authorized Distributor delivers the products to the purchaser.
Notwithstanding the foregoing, in no event shall the warranty period
extend more than the time stated plus one year from the date Parweld
delivered the product to the authorized distributor.
8.0 accessories
8.1 Torch spares
Stock Code
Description
CKE403
Electrode Holder with 3m Lead
CKC403
Earth Lead 3m with Clamp
ER17-12S1BGD
Direct fit Tig Torch
WP17AK
Tig Spares Kit in Plastic Case
8.2 Gas equipment
Everyday Gas Regulators – 300
BAR
Single Stage
Features
Flow rate up to 96m
3
/h (3389 ft
3
/h)
• Full 300 bar capability
• Outlet pressure indicated on the bonnet
• Bottom entry design suited for top outlet
cylinder valves
Fittings
• Fitted with standard 3/8” BSP outlet
• Fitted with
5
/8” BSP inlet connections
Stock Code Description
Maximum Outlet
Pressure
E700140 Argon Preset Regulator
3.0 Bar
E700141 Argon Indicator Regulator 3.0 Bar
E700113 1 Gauge Argon
30 lpm flow
E700123
2 Gauge Argon
30 lpm flow
Flow Meters
Features
• Designed from brass bar whilst the tube
and cover are moulded from high quality
polycarbonate to ensure high impact
resistance and clarity
• Calibrated to operate at an inlet pressure
of 30PSI
• Sensitive needle valve provides easy
adjustment and the downward facing
outlet
connection eliminates hose kinking.
Fittings
• Fitted with standard
3
/
8
9 BSP inlet and outlet
connections
Stock Code Description
706100
Flow Meter Mixed Gas 15
lpm
Summary of Contents for XTI-601 MP
Page 1: ...INSTRUCTION MANUAL...