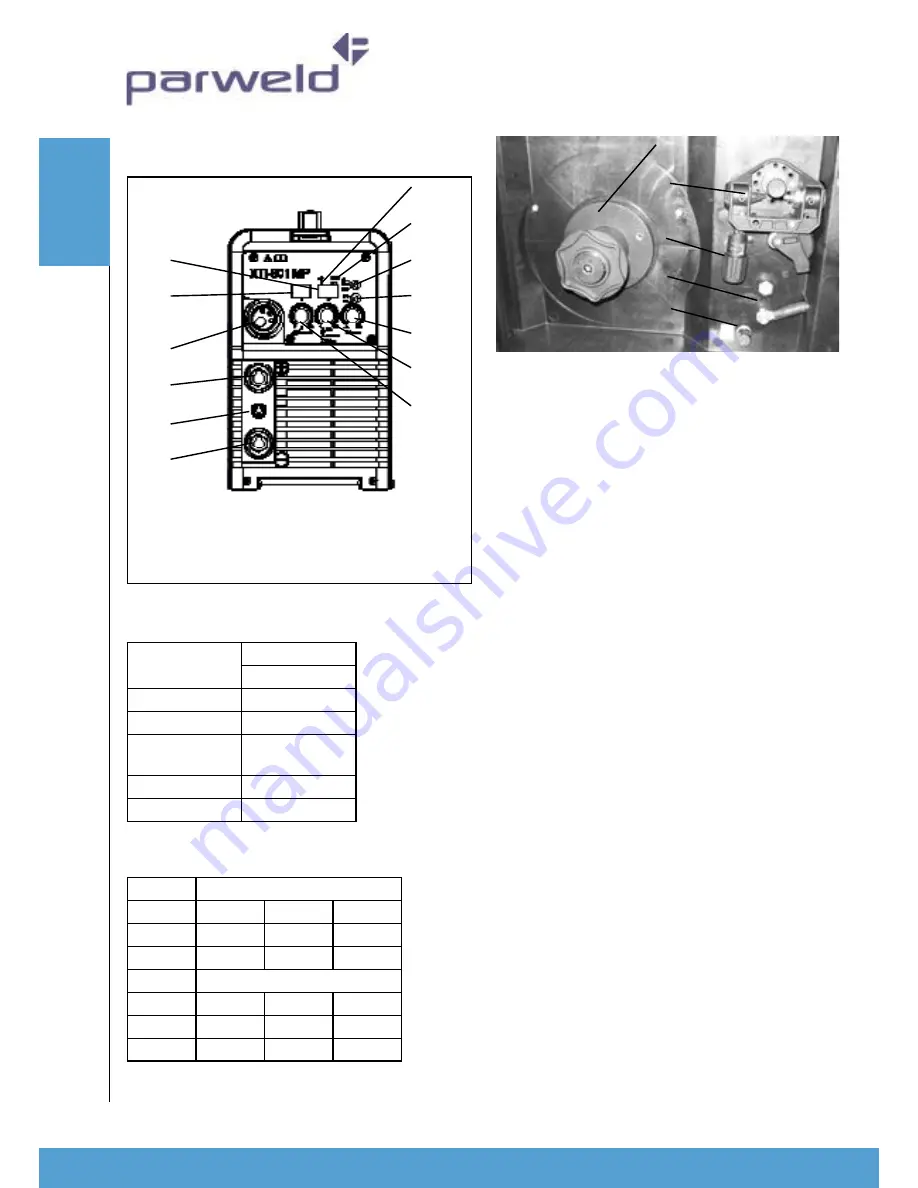
www.parweld.com
6
4.0 Description of Controls
1) Voltage Display. Displays the welding voltage for
the MIG process and the arc voltage for TIG and MMA
welding
2) Amperage Display. Displays the welding amperage
during MIG, TIG and MMA welding
3) MIG torch euro connector, for connection of the
MIG torch
4) Posative output connection, used to connect the
cables for TIG and MMA welding. This is the 50mm
Dinse connection socket.
5) Trigger socket used to connect the trigger control
on the TIG torch
6) Negative output connection used to connect the
cables for TIG, MIG and MMA welding. This is the
50mm Dinse connection socket.
7) Power light This indicates mains power is applied
to the machine and that the machine is currently
switched on when the light is illuminated
8) Fault light indicates if the machine has overheated
or developed a fault condition.
9) MIG/MMA/TIG selector switch Used to select
between MIG, MMA welding mode and Lift-arc TIG
welding.
10) Latch in trigger selector
11) Inductance control, this hardens or softens the arc
in MIG welding, .
12) Voltage control This function controls the MIG
welding voltage. When in MMA mode it controls ARC
force and for TIG welding it controls the time of the
gas post flow.
13) Amperage control for adjusting the Amperage in
MMA or TIG welding and also the wire feed speed in
MIG welding.
14) MIG wire spool holder accepts 5KG (200mm )
spools
15) Wire feed box for MIG welding
16) Wire tension adjuster for MIG welding
17) Polarity adjustment for MIG welding
18) Burn back control for MIG welding.
ON OFF Switch for switching on or off the mains
supply to the machine. (mounted on the rear of the
machine)
Note the output of the machine is permanently on
3.0 Technical Specifications
XTI-601MP
Input voltage
230V +/- 10%
Frequency
50/60Hz
Input current
33A max
15 eff
Fuse rating
16A
Output OCV
56
MIG
25A/14.4V to 160A/22V
X
30%
60%
100%
I2
160A
115A
90A
U2
22V
20V
18.5V
TIG
10A/10.4V TO 160A/16.4V
X
30%
60%
100%
I2
160A
115A
90A
U2
16.4V
14.6V
13.6V
1
2
3
4
5
6
CO
ntr
O
lS
7
8
9
10
11
12
13
14
15
16
17
18
Summary of Contents for XTI-601 MP
Page 1: ...INSTRUCTION MANUAL...