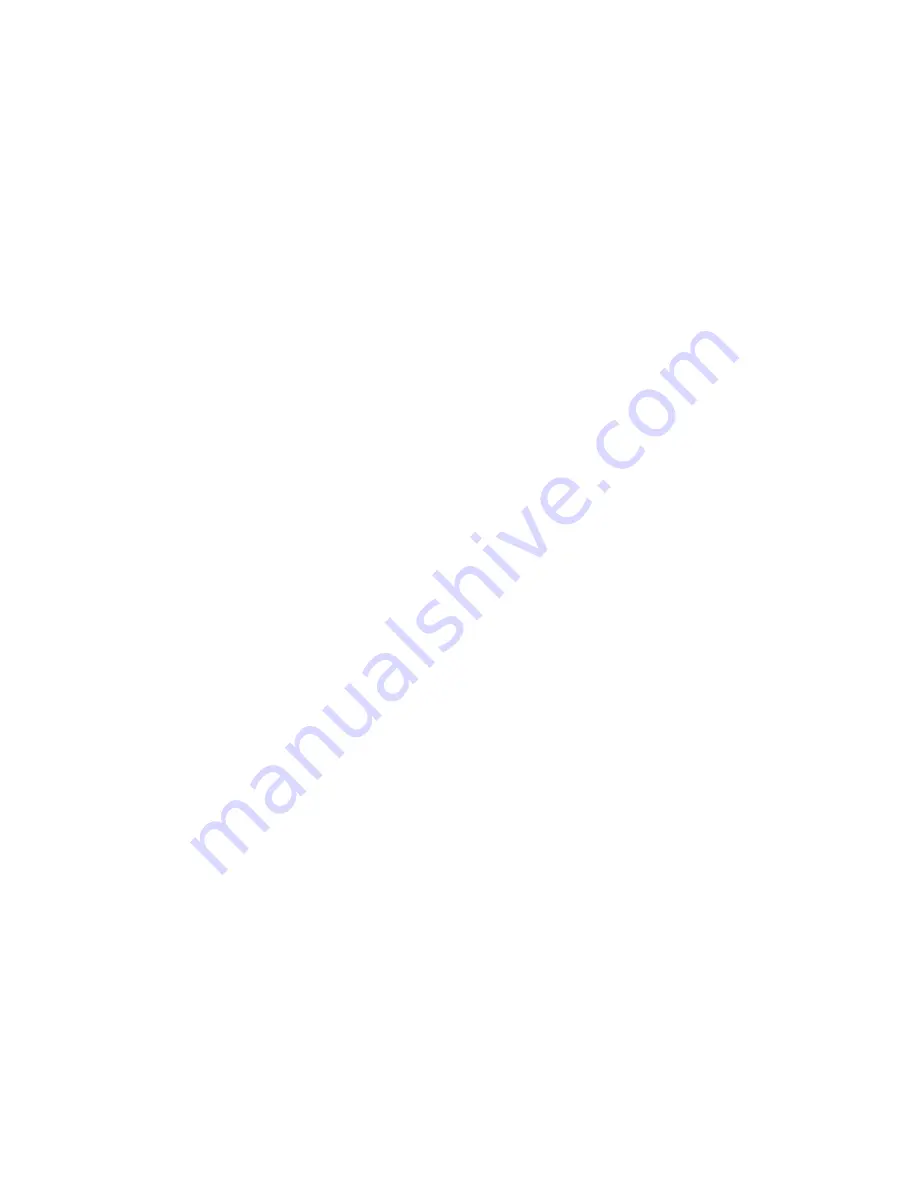
P
AGE
15
3.1.2.2 PULSED OUTPUTS
Pulsed output(s), one for each pen, can be implemented on instruments provided with the
totalization feature and a relay that is not assigned to any other function.
Pulsed output is selected in the Program mode. With a pulsed output select (PoS) equal to 1,
each time the Totalizer Display is incremented, the relay that is assigned, in the Program
mode, as a pulsed output will close for a duration of 50 milliseconds or 60 milliseconds based
on a 60 Hz or 50 Hz line frequency, respectively.
On two pen instruments, a Combined Pulse Output is available. This feature provides a
pulsed output as the Combined Total increases.
Note: Upon sensor break, the Combined Pulse Output will increment at a indetermi-
nate rate.
3.1.2.3 PROCESS VALUE RETRANSMISSION
Process value retransmission can be implemented on instruments provided with at least one 4
to 20mA output.
Process value retransmission is selected in the Program mode. When selected, a current
output must be assigned and the process output must be scaled.
On two pen instruments, a Combined Flow Rate is available. When selected in the Program
mode, this feature provides a process value retransmission value equal to the combined flow
rate. The value is scaled using Pen 1 process output upper and lower parameters.
3.1.2.4 DATA LOGGING
Data logging can be implemented on instruments provided with the data logging feature, and
it will store data for up to 28 days.
Each day, at the time specified by
ttLd
(time to log data), the following data will be logged:
date, minimum rate, its time, maximum rate, its time, daily total, and average rate. The daily
total is derived by substracting "yesterday's total" from the current total. The average rate is
derived from the daily total, taking into account the flow time base. After the data is logged,
"yesterday's total" will be set to the current total, and the minimum and maximum rates and
times are set to the current rate and time.
Logged data is accessed via a day number, with 1 through 7 corresponding to the current
week. At the beginning of each week (00:01 on day 1 - each Monday) the data is shifted
down one week, with the oldest weeks worth of data being discarded. All data for the current
week is zeroed, including the date for each day.
3.1.2.5 ENGINEERING UNITS PROCESSING ALGORITHM
In the Program mode, the parameter
EuPA
, Engineering Units Processing Algorithm specifies
how the engineering unit inputs are handled. This allows selection of the various algorithms
to convert the raw input in to the desired process value.
LINEAR CONVERSION -
EuPA
= 0
For those sensors/transmitters that provide an output directly proportional to flow, or other
applications where the instrument may be used with a linear input to output transformation.
SQUARE ROOT EXTRACTION -
EuPA
= 1
The square root extraction function applies to rate of flow measurments using differential
pressure sensors. Differential pressure transmitters typically generate a 4-20mADC signal
that represents differential pressure, not flow. The flow is a function of the square root of the
differential pressure.
2 STAGE SQUARE ROOT EXTRACTION -
EuPA
= 2
This approach is used to minimize the process value below a 4% input, since it is less
meaningful due to inaccuracy and repeatability problems. Below 4% a linear function is
applied.
(Continued on next page)
Summary of Contents for MRC 7800
Page 56: ...PAGE 56...