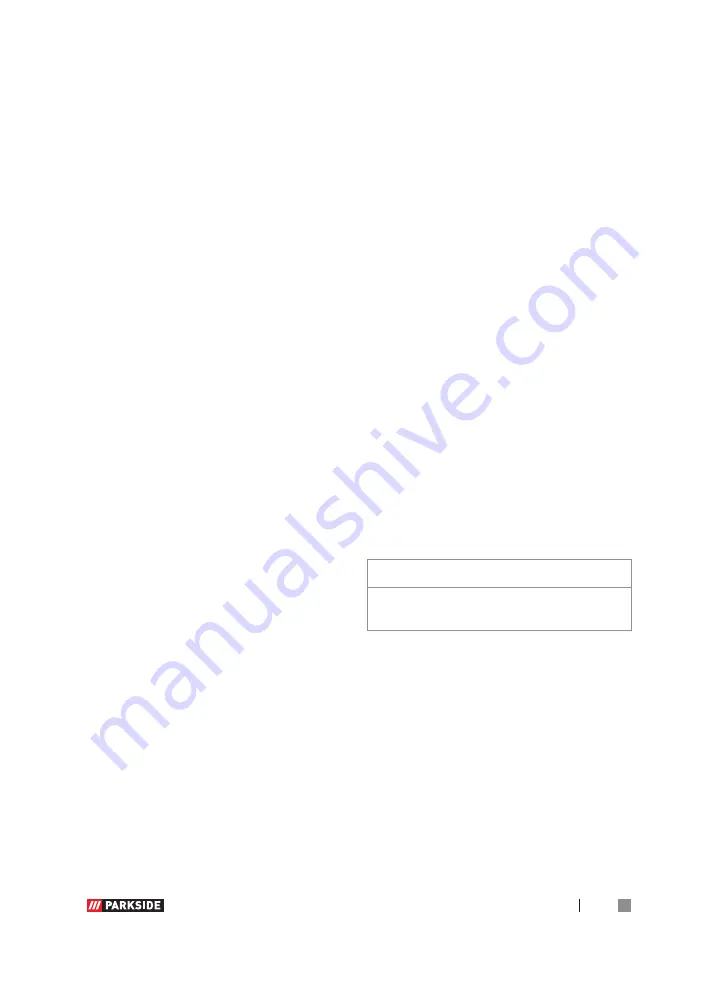
15
GB/IE/NI/CY/MT
cutting work is performed.
The following is recommended
to reduce possible interference
radiation:
the plasma cutter must be
regularly maintained and kept
in good condition
Cutting cables should be com-
pletely unwound and installed
parallel on the floor, if possible
Devices and systems at risk of
interference radiation must be
removed from the cutting area
if possible, or shielded.
• General plasma
explanations
Plasma cutters are operated by
pushing pressurised gas, e.g.
air, through a small pipe. In the
centre of the pipe, there is a
negatively charged electrode that
is directly above the nozzle. The
vortex ring causes the plasma to
rotate quickly. If you supply the
negative electrode with current
and make the tip of the nozzle
touch the metal, this connection
creates a closed, electrical circuit.
A powerful spark occurs between
the electrode and the metal.
While the gas flows into the
pipe, the spark heats up the gas
until it has reached the plasma
condition. This reaction causes
a current from the controlled
plasma with a temperature of
16,649 ºC or more that moves at
speed of 6.096 m/sec and the
metal transforms into steam and
molten discharge. The plasma
itself conducts electrical current.
The working circuit that allows
the arc to occur remains as long
as current is supplied to the
electrode and the plasma remains
in contact with the metal to be
processed.
The cutting nozzle has a range
of further channels. These chan-
nels generate a constant flow of
shielding gas around the cutting
area. The pressure of the gas
flow controls the radius of the
plasma jet.
NOTE!
f
This machine is only designed to use
compressed air as “gas”.
• Before use
• Installation environment
Make sure that the working area is suf-
ficiently ventilated. If the device is used
without sufficient cooling, the power-on time
reduces and it can result in overheating.
Additional protection can be required for this
purpose:
Summary of Contents for PPS 40 B3
Page 4: ...8b 8c 8d F G 16 15 H J 21 21 17 16 18 2 20 19 I 8d 8e 8e L K 21 21 8b 8c...
Page 128: ...128 PL...
Page 292: ...292 BG 2012 19 M V I1 max H IP21S I1 eff t ON t ON max...
Page 293: ...293 BG PPS 40 B3 f 1 50 Hz U0 U1 U2...
Page 296: ...296 BG 15 10 m...
Page 297: ...297 BG f 30 mA...
Page 298: ...298 BG z 16...
Page 299: ...299 BG z 48 V...
Page 300: ...300 BG z z z I...
Page 301: ...301 BG z z z IEC 60974 10...
Page 302: ...302 BG...
Page 303: ...303 BG 16 649 C 6 096 m s f 0 5 m...
Page 305: ...305 BG 2 3 17 4 4 5 13 6 8 8f 8a 8a 7 8 9 8f 8a 5 1 8 8a 8c f 2 3 f...
Page 306: ...306 BG ON...
Page 307: ...307 BG 8 on 8c 8c 8c 8b 8c 8d 8 8b 8c 8d 8...
Page 308: ...308 BG 8b 8c 8d 5 100 PSI 6 8 bar F 8d 8c 8b 8d 1 5 mm f 8c 8d 8c 8b...
Page 309: ...309 BG f 8b 8 8d 8c f f f 18 2012 19...
Page 311: ...311 BG St Ingbert 01 07 2022 Dr Christian Weyler Creative Marketing Consulting GmbH 3 112 115...
Page 312: ...312 BG IAN 365029_2204 www lidl service com QR Lidl www lidl service com IAN 365029...
Page 314: ...314 BG 5 114 1 113 1 2 2 3 115 4 3 61 2014 25 07 2014 115 1 2 1 3 1 1...
Page 316: ...316 GR 2012 19 E M V I1 max H IP21S I1 eff t ON t ON max...
Page 317: ...317 GR Plasma PPS 40 B3 f 1 50 Hz U0 U1 U2...
Page 320: ...320 GR on off 15 10 m...
Page 321: ...321 GR f 30 mA...
Page 322: ...322 GR z 16...
Page 323: ...323 GR z 48V...
Page 324: ...324 GR z z z z...
Page 325: ...325 GR z z IEC 60974 10 A A...
Page 326: ...326 GR A...
Page 327: ...327 GR 16 649 C 6 096 m s f 0 5 m...
Page 329: ...329 GR 6 8 8f 8a 8a 7 8 9 8f 8a 5 1 8 8a 8c f 2 3 f...
Page 330: ...330 GR on off Off HF 8 on...
Page 331: ...331 GR 8c 8c 8c 8b 8c 8d 8 8b 8c 8d 8 8b 8c 8d...
Page 332: ...332 GR 5 100 psi 6 8 bar F 8d 8c 8b 8d 1 5 mm f 8c 8d 8c 8b f 8b 8 8d 8c f f...
Page 333: ...333 GR f 18 2012 19 Lidl a b 1 7...
Page 335: ...335 GR O 2251 1194 IAN www lidl service com QR Lidl www lidl service com IAN 365029...