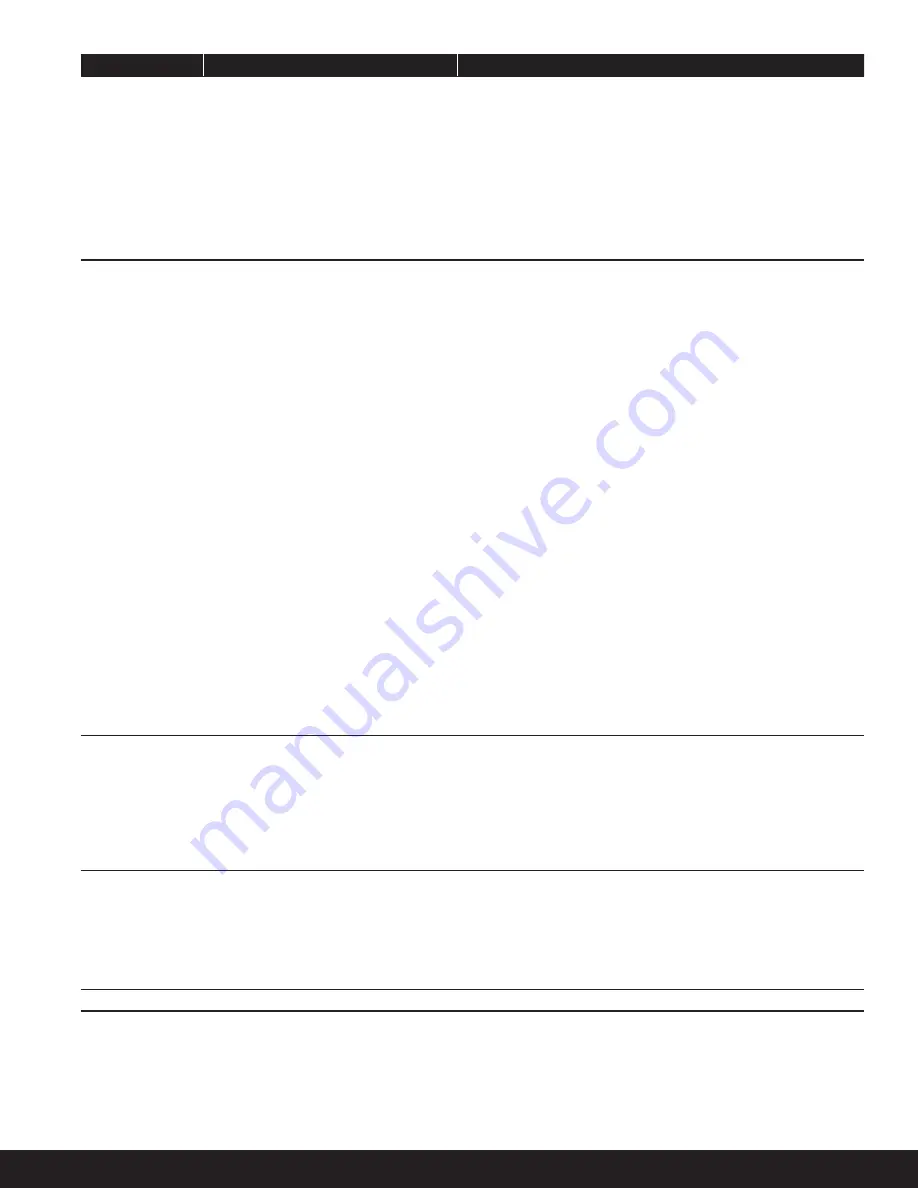
Bulletin 75-00 J / Page 13
Symptom
Possible Cause
Solution
Water bubbler
cloudy.
Water supply turned off.
Hard water.
Venting ammonia.
Open water supply ball valve supplied with purger.
Check water solenoid coil for proper operation (Loose wire,
burned out). Replace if necessary.
Used treated water (softened). Clean bubbler on regular bases to
prevent severe clouding.
Check vent solenoid for proper operation. If bubbles are seen in
the water bubbler when idol, vent solenoid is leaking. Clean or
replace solenoid if needed.
Purger stays in
“Pre-Cool” mode,
will not purge.
Suction too high.
Liquid NH
3
supply off or obstructed.
RTD (#19) not reading accurately or no
display.
Verify Suction is below 4.4
o
C (40
o
F) - 4.0 bar (58.4 psig) for
R-717.
Adjust the A2 (#21) suction regulator to maintain 3 psig (If in or
near a vacuum). If suction is above 3 psig, remove setting from
A2 regulator by turning stem counter clock wise until it stops.
Check liquid ammonia solenoid, SV2 (#8), for proper operation
(Loose wire, burned out). Replace if necessary.
Check controller display for “Liquid Solenoid” pilot light.
Segment should be darkened if liquid is required. This is located
on the upper left side of the front panel (#1).
Check optical level sensor (#17) for proper operation (Loose wire,
defective sensor). Replace if necessary.
Check liquid supply orifi ce (#11) for obstructions. Clean or
replace if necessary.
Note: RTD is factory calibrated and no fi eld adjustment is
required.
If the main controller displays “_ _ _” rather than an actual
temperature reading, check for loose wires. Check wire
loom from main board to cover for loose or damaged wires/
connections.
Replace RTD if necessary.
No temperature
reading on
controller display.
Loose RTD (#19) wire on main terminal
block.
Loose or damaged wire loom
connecting front panel to main board.
Faulty RTD.
Check for loose wires connecting the RTD to the main controller
board.
Check wire loom from main board to cover for loose or damaged
wires/ connections.
Check resistance range of the RTD (100 ohm +/- 0.1%) Replace
RTD if necessary.
No pressure
reading on
controller display.
Loose wire on main terminal block.
Faulty pressure transducer.
Note: pressure transducer (#18) is factory calibrated and no fi eld
adjustment is required.
Check for loose wires connecting the pressure transducer to the
main controller board.
Replace pressure transducer if necessary.
Note:
all items with a (#) can be located in the V200 auto purger parts diagram.
V200 Service Pointers