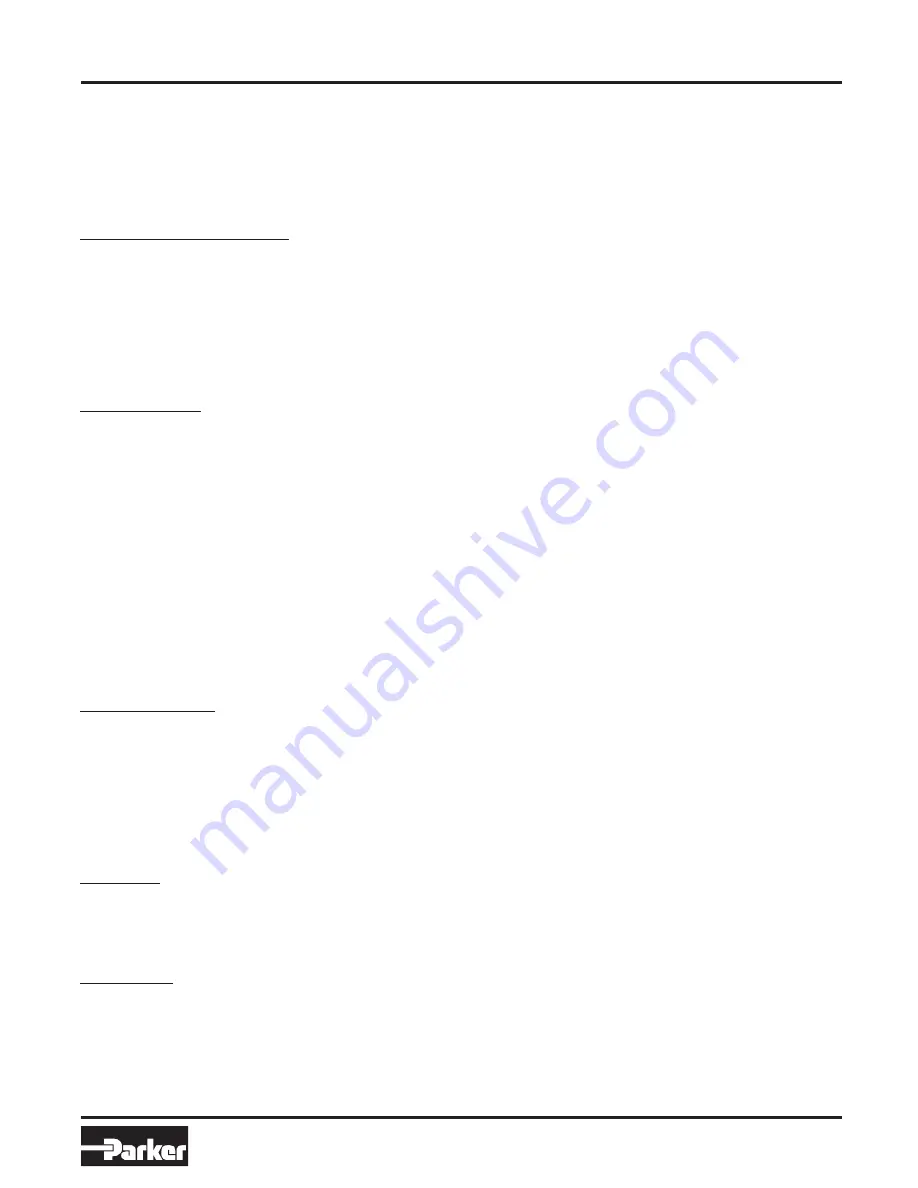
23
Instruction Manual
Oildyne 108/118 and 165/175 Series
Hydraulic Power Units
Bulletin HY22-3210A/US
Parker Hannifin
HPS Division
New Hope, MN 55428 USA
Maintenance
tank), through the hole in the reservoir end. With the screw
vertical, locating the pump’s mounting leg will take some effort.
Once the pump leg is found, turn the screw counter-clockwise
until an audible ‘click’ is heard and felt by the fingers. At this
point turn the screw clockwise to begin tightening the screw into
the pump mounting leg. Tighten to a torque of 1.9 +/- .3 Nm (17
+/- 3 in-lbs). Follow the complete mounting, filling, bleeding and
startup instructions on page 15.
‘C’, ‘D’, ‘P’, ‘Q’, ‘R’ and ‘S’ reservoirs
Ensure the reservoir seal is in place in the power unit adapter
pilot. With the reservoir sitting upright on a flat surface, orient
the power unit adapter to correctly align with the ‘tabs’ on
the power unit adapter with the brass inserts by the reservoir
opening. Push the power unit gently down onto the reservoir
to engage the reservoir seal. Once the power unit is firmly on
the reservoir, reinstall the four Phillips-head screws through the
power unit adapter ‘tabs’ into the reservoir brass inserts and
tighten to 2.8 +/- .5 Nm (25 +/- 5 in-lbs). Follow the complete
mounting, filling, bleeding and startup instructions on page 15.
‘F’ and ‘G’ reservoirs
With the reservoir vertical, ensure the ‘V-lip’ seal is in place on
the reservoir mouth. The reservoir wall is positioned inside the
‘V’. Orient the power unit over the reservoir so the reservoir
ffiller/breather is on the same side as the ports surface of the
power unit adapter. The ‘tab’ on the power unit adapter to the
left of the UP port should align with the welded reservoir ‘ear’.
Insert the screws from the underside of the ‘ears’ up toward the
power unit, ensuring the plastic spacers are in place between
the reservoir ‘ears’ and the power unit adapter ‘tabs’.
These
are self tapping screws so following these instructions
is critical to ensure a proper installation.
When the screw
touches the power unit adapter ‘tab’, turn the screw slowly
counter-clockwise (when viewed from the screw head) until an
audible ‘click’ is heard and felt, confirming the screw thread is
properly engaged with the power unit ‘tab’ threaded hole. Then
turn the screw in the opposite direction to tighten the screw.
Torque both screws to 2.8 +/- .5 Nm (25 +/- 5 in-lbs). Follow the
complete mounting, filling, bleeding and startup instructions on
page 15.
‘H’, ‘I’ and ‘J’ reservoirs
Ensure the o-ring is in place in the groove of the reservoir
adapter plate. Position the reservoir so the filler/breather is
aligned between the power unit’s UP and DN ports. Gently
push the reservoir into the reservoir adapter plate until the
reservoir is snug against the plate. Install the four screws from
the reservoir end into the reservoir flange holes into the brass
inserts of the reservoir adapter plate. Hand- tighten all four
screws then alternately tighten each screw to 2.2 to 2.8 Nm (20
to 25 in-lbs). Follow the complete mounting, filling, bleeding and
startup instructions on page 15.
All Reservoirs
Maintain oil level at all times. The oil should be checked after
the first 100 hours and verified that the class of oil meets the
requirements of the pump being used. Change the oil every
1000 to 2000 hours depending on the application and operation
environment.
Hydraulic Fluids
The type of fluid must be compatible with the Nitrile (Buna
N) seals used on the power unit, and must comply with the
recommendations of the manufacturers of the component
parts. Acceptable fluids include standard Automatic
Transmission Fluid (ATF) and most mineral based hydraulic
fluids with viscosities between 32 cSt (150 SSU) and 64 cSt
(300 SSU) at 38°C (100°F). For fluids other than these please
contact Parker Oildyne with the details. If users wish to use
alternative oil, hydraulic fluid or ATF, they are warned to check
that they have the same properties as those recommended.
Parker Oildyne takes no responsibility if alternatives are
used.
Maintenance Suggestions
1. Never return to the system any fluid which has leaked out.
2. Always keep the supply of fresh fluid covered tightly.
3. Use clean containers, hoses, and funnels when filling
the reservoir. Using a filter cart when adding oil is highly
recommended.
4. Use common sense precautions to prevent entry of dirt into
components that have been temporarily removed from the
circuit.
5. Make sure that all filler/breathers on the reservoir are
properly fastened.
6. Do not run the system unless all normally provided suction
strainers are in place.
7. Make certain that the fluid used in the system is of a type
recommended by the manufacturers of the system or
components.
8. Parker Hannifin offers an oil sampling kit which can be
used to ascertain the condition of the system fluid.
Check Oil Samples Periodically
Checking oil temperature periodically is good preventive
maintenance. Periodically siphon an oil sample from the
reservoir and compare it with a sample of clean, new oil.
Oil that has been running too hot will look darker and feel
thinner than new oil. It will also smell burned. Normally it
will contain more contaminants, because hot oil leads to
accelerated wear of component parts.
Recommended Spare Parts
• Suction strainer, Parker Oildyne part number 410521.
• ‘A’ reservoir mounting screw, Parker Oildyne part number
411355; screw o-ring part, number 409815.
• ‘B’ reservoir mounting screw – is power unit specific –
please contact Parker Oildyne with the power unit 6-digit
part number.
• ‘C’, ‘D’, ‘P’, ‘Q’, ‘R’ and ‘S’ reservoirs mounting screw,
Parker Oildyne part number 415222.
• ‘F’ and ‘G’ reservoir mounting screw, Parker Oildyne part
number 415020; plastic spacer, part number 412051.
• ‘H’, ‘I’ and ‘J’ reservoir mounting screw, Parker Oildyne part
number 415939.
For any other requirements please contact Parker Oildyne with
the 6-digit part number of your power unit. This number is
located on the power unit Parker Oildyne label.
Be aware of risk of hazards if poor quality replacement parts
are used or are obtained from an unauthorized source.
Troubleshooting
Personnel involved with maintaining these units are advised to
wear gloves and protective clothing.
See pages 24 and 25 for troubleshooting help.
Conclusive Unit Failure
If the operation of the unit cannot be restored after attempts at
the trouble shooting suggestions listed previously, please contact
your local distributor or the Parker Oildyne directly to arrange for
warranty replacement/repair if within the warranty period.