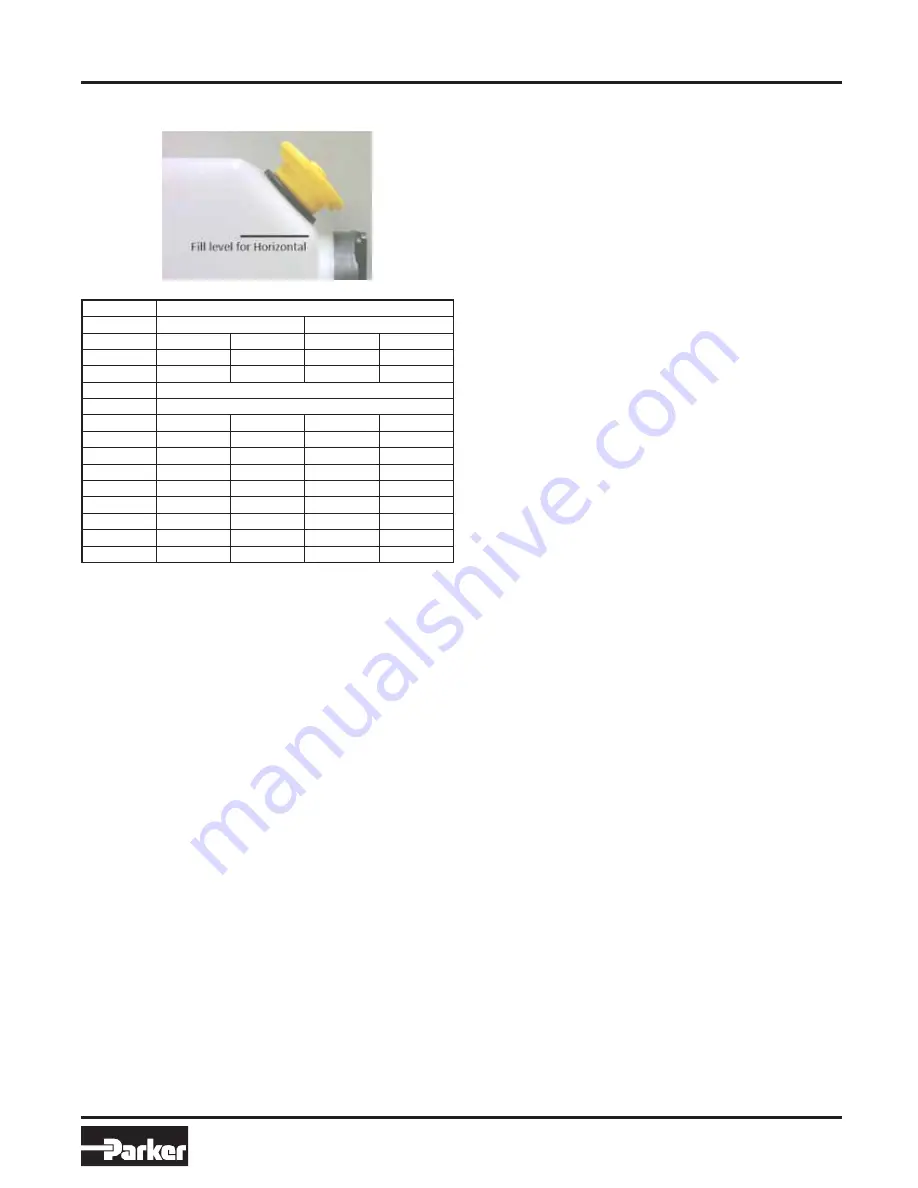
15
Instruction Manual
Oildyne 108/118 and 165/175 Series
Hydraulic Power Units
Bulletin HY22-3210A/US
Parker Hannifin
HPS Division
New Hope, MN 55428 USA
Start-Up Procedures
P, Q, R and S tanks filled to the shoulder below the filler/
breather: See below:
Horizontal Mount (ports face up)
Total Volume
Usable Volume
Code
Liter
Gallon
Liter
Gallon
A
.49
.13
.41
.11
B
.75
.20
.64
.17
C
Vertical Only
D
Vertical Only
F
1.8
.48
1.5
.40
G
1.1
.29
.91
.24
H
2.6
.71
2.4
.65
I
4.5
1.2
4.2
1.1
J
6.0
1.6
5.6
1.5
P
1.2
.32
.94
.25
Q
1.9
.52
1.5
.41
R
3.7
1.0
3.0
.80
S
2.8
.75
2.3
.61
It is strongly recommended that the customer have available the
MSDS for the fluid chosen for use in the 108/118 and 165/175
Series Power Units. Follow all instructions should the fluid be
spilled or come in contact with an operator.
Start-Up Procedures
The product label on the power unit provides the maximum
current (Amperes) that the motor will draw at full power.
For the AC motors used on the 108/118 Series Power Units,
fuses and circuit breaker protection must conform to national
electrical code and your local codes and practices.
For DC motors, refer to the power unit model code and the
performance curves to determine the maximum current your
pump and motor combination will draw at your relief valve
setting(s). Fuse and circuit breaker protection must conform to
national electrical codes and your local codes and practices.
For Single Direction Circuits of 108 and 165 Series
(codes NN and WW)
Ensure the reservoir is filled with an approved fluid. Jog the
motor until oil flows from the ‘UP’ port. If oil does not flow from
the ‘UP’ port, reverse the wire leads on the motor, and repeat.
The pump is now primed. When using an externally mounted
directional control valve (DCV), connect the tank port of the DCV
to the ‘DN’ port of the power unit. Connect the ‘UP’ port of
the power unit to the inlet port of the DCV. If using an externally
mounted two-way release (dump) valve, tee the valve into the
pressure line and plumb the oil return line to the ‘DN’ port. Cycle
the system a few times to ensure the air is out of the circuit.
For Solenoid Valve Circuits of 108 and 165 Series
(codes S1 to S8)
Ensure the reservoir is filled with an approved fluid. If the solenoid
valve is a normally open type, energize the coil with appropriate
voltage to close the valve. Jog the motor on and off until oil shows
at the outlet port of the solenoid manifold. If no oil appears, check
the motor wiring for the proper rotation, and then repeat. Once oil
is visible, connect one end of your fluid conductor to the power
unit manifold port and tighten. Connect the other end of the fluid
conductor to the actuator port, leaving the connection loose. Jog
the motor again until oil appears at the actuator port, and then
tighten the conductor fitting. Energize the motor now to fully rotate/
extend the actuator. If a normally open valve is used, de-energize
the coil to allow the oil from the actuator to return to the power unit
reservoir. (Note: the oil from the actuator will only exit the actuator
if an external force, or spring, is moving the actuator back to its
home position.) If a normally closed valve is being used, energize
the coil with the appropriate voltage to open the valve allowing the
oil from the actuator to return to the power unit reservoir. Cycle the
system a few times to ensure the air is out of the circuit.
For Reversible Circuits of 108 and 165 Series (codes
RR, RB, LL, LB)
Ensure the reservoir is filled with an approved fluid. Using a port
plug of your adapter’s port type, plug the ‘DN’ port. This forces
the pump to draw fluid from the reservoir instead of drawing in
air from the open DN port. Jog the motor until oil flows from the
‘UP’ port. If oil does not flow from the ‘UP’ port, reverse the
wire leads on the motor, and repeat. The pump is now primed.
Connect the fluid conductor to the ‘UP’ port and tighten.
Connect the other conductor end to the piston end of a fully
retracted actuator. With the conductor fitting loose, operate the
power unit until oil (and no air) bleeds from the loose actuator
fitting. Tighten the fitting. Refill the reservoir. Operate the
power unit in the ‘UP’ port rotation (same direction as previously
run). Continue until the actuator is fully stroked, adding only
enough fluid to the reservoir to get the actuator fully stroked.
(Adding too much oil at this point could cause the reservoir to
overflow when the actuator is reversed.)
Remove the plug from the ‘DN’ port and connect one end of
the second fluid conductor to it, then tighten. Jog the power
unit in the ‘DN’ port rotation (opposite direction of earlier), until
oil (with no air) flows from the loose conductor end. Connect
and tighten the fluid conductor end onto the rod end actuator
fitting. Operate the power unit to fully retract the actuator. Once
retracted, check the oil level in the reservoir and add as needed
to maintain full capacity.
Functional testing is considered complete with the successful
priming of these power units and cycling of the actuators.
NOTE: These reversible systems are not self-priming nor
self-bleeding. Failure to follow these instructions can
cause the power unit to not prime, not build pressure, and
operate the actuator erratically.
For 118 and 175 Series (all circuit codes)
Because of the variety of customer-supplied manifolds, valves
and circuits which can be mounted to the 118/175 Series Power
Units, please consult Oildyne for specific startup instructions.
Please provide a hydraulic schematic of your circuit to assist
Parker Oildyne.
Additional Testing
If required, any tests for radiated and conducted emissions
should be performed in accordance with the Electromagnetic
Compatibility (EMC) Generic Emissions standards for
environments appropriate to the end use product to confirm
compliance with the EMC Directive.
If required, any tests for radiated and conducted immunity
should be performed in accordance with the Electromagnetic
Compatibility (EMC) Generic Immunity standards for
environments appropriate to the end use product to confirm
compliance with the EMC Directive.