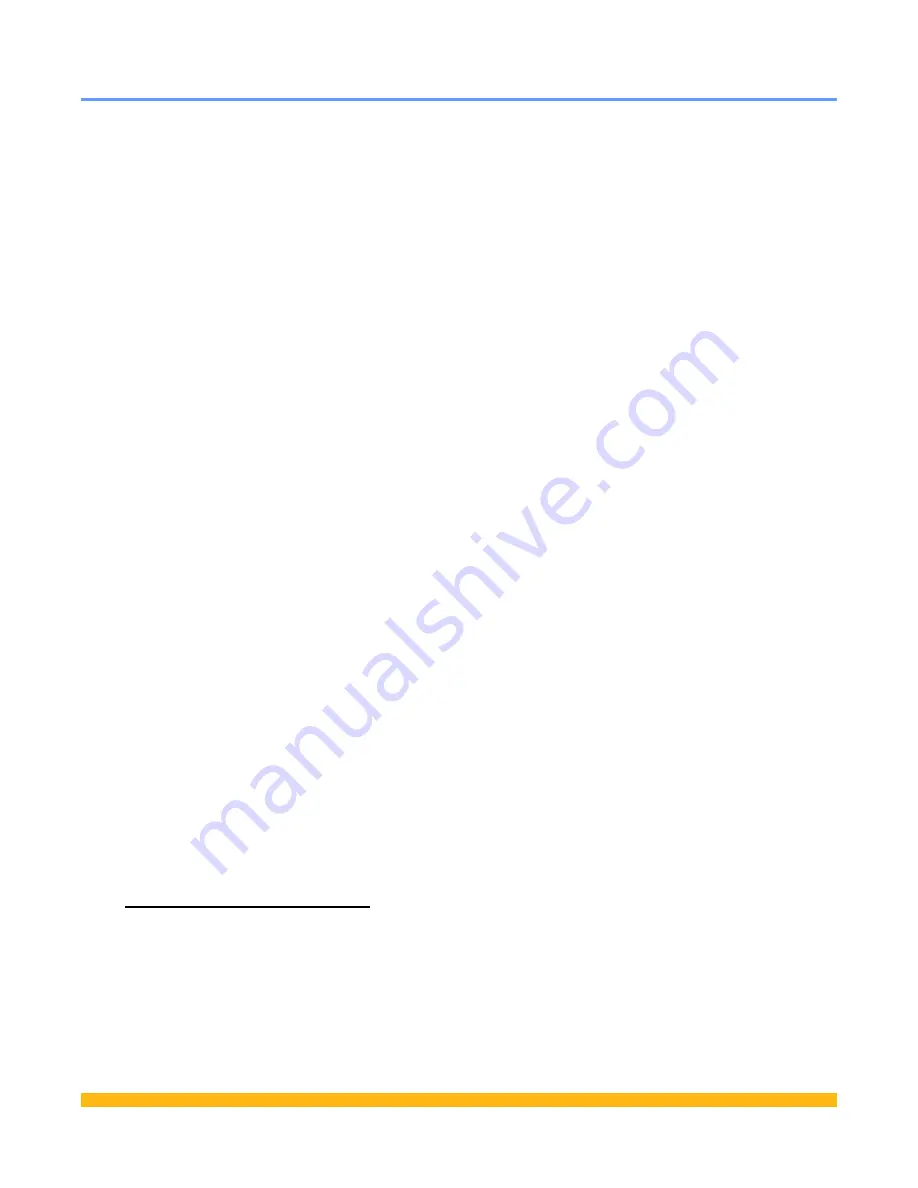
MX45S Series Product Manual
22
Parker Hannifin Corporation
EMN Automation - Parker
Irwin, Pennsylvania
Grounding / Shielding
All cables are shielded. These shields are to be grounded to a good earth ground. Failure to ground
shields properly may cause electrical noise problems. These noise problems may result in positioning er-
rors and possible run away conditions.
The motor cable has an area of the shield exposed to allow a grounding path from shield to drive ground.
MX45S purchased with ViX drives as part of the configurable part number come equipped with p-clips de-
signed for the small OD of the motor cable to allow the cable shield to be grounded to the ViX ground.
Cabling
The MX45S is provided with high flex cabling.
The encoder cable is terminated with a Renishaw Tonic Interface adapter (15 pin “D” type connector).
The motor cable is terminated with flying leads which are stripped and tinned and ready for installation into
the screw terminals on the ViX drive.
The limit/home cable is terminated with flying leads which are stripped and tinned and ready for installation
into the screw terminals on the ViX drive.
For wire color codes and pin outs see tables in electrical section of manual.
Recommended bend radius for these cables is 50mm. This radius will provide a minimum of 10 million
cycles of the cable. Smaller bend radius will reduce cable life while larger bend radius will increase life.
If the positioner is mounted in a multi-axis configuration special care should be taken in routing and strain
relieving the cables so as to prevent flexing of the cable at the connection to the table and where mounted
stationary to the structure. Provide sufficient service loop that the cable bends a minimum of 25mm from
these end points. It is also recommended to avoid twisting the cable. The cable should be secured in a
position which will orient it in a direction that creates a single plane of operation for the cable.
Cable Management
For multi-axis configurations special attention needs to be taken into account for the moving cables on the
non-base axis.
TIP: For Multi-axis Configurations
.
Consider using the top axis for the highest frequency move in the application. The top axis will have the
least amount of weight to move and will reduce the cycles on the cables.