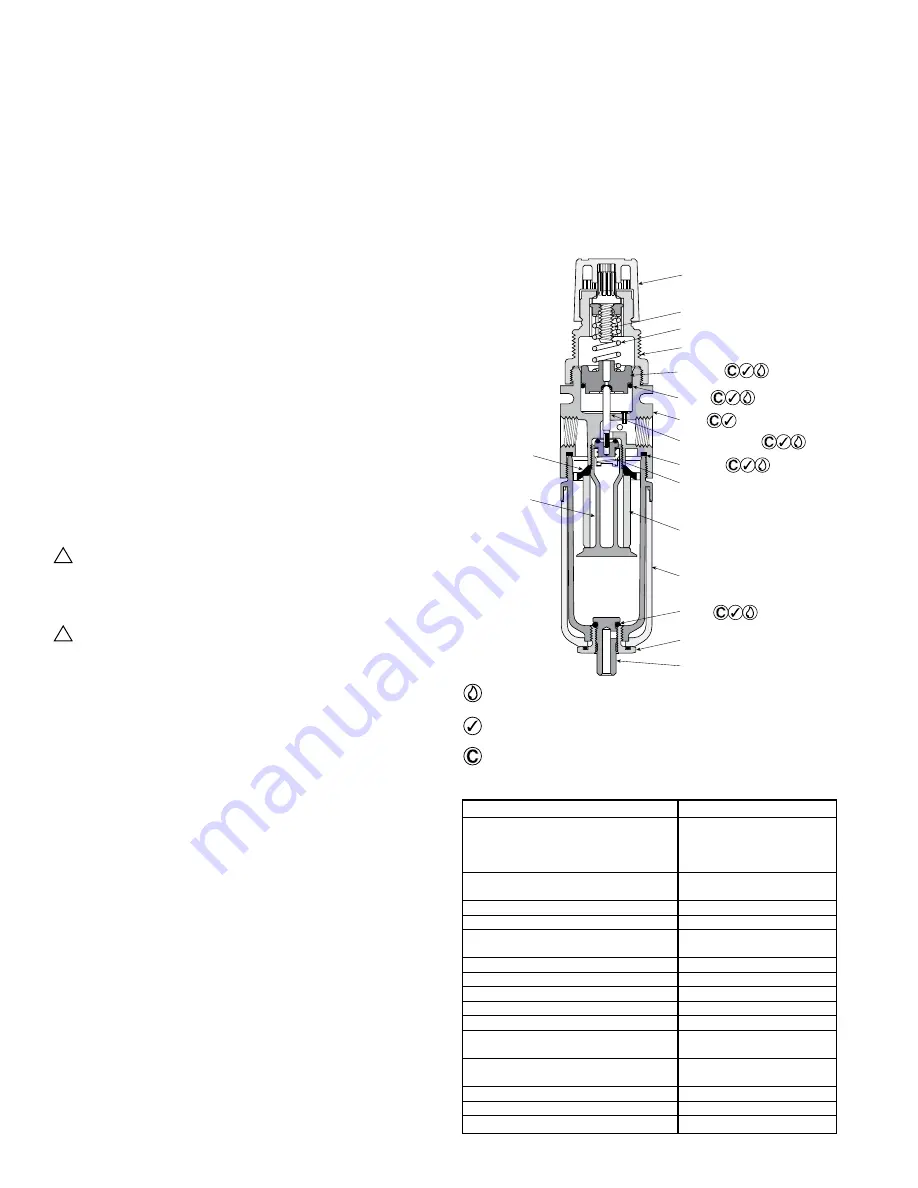
Adjusting Knob
Adjusting Screw Assembly
Bowl Seal
Inner Valve
(Poppet) Assembly
Control Spring
Spring, Return
Piston
Assembly
Piston
O-ring
Body
Spring Cage (Bonnet) Assembly -
Torque: 4.5 to 5.6 Nm (40 to 50 in. lb.)
Filter
Element
Bowl
Sight Gauge Retainer
Deflector
(Vane Plate)
Element
Retainer
O-Ring
Manual Drain
(Finger Tighten)
B35 Integral Filter / Regulator
IS-B35
Service
Caution: Disconnect or shut off air supply and exhaust the
primary and secondary pressures before servicing unit.
Turning the Adjusting Knob counterclockwise does not vent
downstream pressure on non-relieving regulators. Downstream
pressure must be vented before servicing regulator.
Caution: Grease packets are supplied with kits for lubrication
of seals. Use only mineral based grease or oils. Do not use
synthetic oils such as esters. Do not use silicones.
Note: After servicing unit, turn on air supply and adjust regulator
to the desired downstream pressure. Check unit for leaks. If
leakage occurs, do not operate - conduct repairs and retest.
Servicing Filter Element -
(Refer to Figure 1)
1. Unscrew and remove Bowl.
2. Unscrew the Element Retainer from Body and then remove
Deflector and Element.
3. Clean all internal parts and bowl before reassembling.
4. Install new element. Install Deflector. IMPORTANT: The Filter /
Regulator will not operate properly if the Deflector is not installed
properly.
5. Attach Element Retainer and finger tighten firmly.
6. Replace Bowl Seal. Lightly lubricate new seal to assist with
retaining it in position.
7. Install Bowl into Body and tighten; hand tight, plus 1/4 turn.
Servicing Regulator -
(Refer to Figure 1)
1. Disengage the Adjusting Knob by pulling upward. Turn Adjusting
Knob counterclockwise until the compression is released from the
Pressure Control Spring.
2. Remove the Bonnet and Bowl assemblies by unscrewing the
Bonnet and Bowl from the Body.
3. Remove Piston Assembly from Body.
4. Remove Element Retainer, Deflector, Filter Element, Poppet
Assembly, Poppet Return Spring.
5. Clean and carefully inspect parts for wear or damage. Wipe
parts, clean with soapy water or denatured alcohol
but do
not use denatured alcohol on plastic bowl or sight gauge
.
!
!
If using compressed air to blow dry, be sure to wear appropriate
eye protection. If replacement is necessary, use parts from
service kits. Clean Bowl.
6. Lubricate O-rings with grease found in service kits.
7. Install Filter Element onto the Filter Retainer, and install Deflector
onto Retainer.
8. Install Poppet Assembly, Poppet Return Spring, Element
Retainer and Element. IMPORTANT: The Filter / Regulator will
not operate properly if the Defector is not installed properly.
9. Install Piston Assembly into Body Assembly. Assemble Bonnet
Assembly onto Body and tighten per Figure 1.
10. Install Bowl into Body and tighten, hand tight, plus 1/4 turn.
4. Install Filter / Regulator so that air flows in direction of arrow on
top of body.
5. Install Filter / Regulator vertically with the bowl drain mechanism
at the bottom. Free moisture will thus drain into the sump (“quiet
zone”) at the bottom of the bowl.
6. Gauge ports are located on both sides of the Filter / Regulator
body for your convenience. It is necessary to install a gauge or
socket pipe plugs into each port during installation.
Operation
1. Both free moisture and solids are removed automatically by the
filter.
2. Manual drain filters must be drained regularly before the separated
moisture and oil reaches the bottom of the Baffle or End Cap.
3. The Filter Element should be removed and replaced when
pressure differential across the filter is 69 kPa (10 PSIG).
4. Before turning on the air supply, disengage the Adjusting Knob
by pulling upward. Turn Adjusting Knob counterclockwise until the
compression is released from the Pressure Control Spring.
5. Then turn Knob clockwise and adjust regulator to desired
downstream pressure. This permits pressure to build up slowly in
the downstream line.
6. To decrease regulated pressure settings, always reset from a
pressure lower than the final setting required. Example, lowering
the secondary pressure from 550 to 410 kPa (80 to 60 PSIG) is
best accomplished by dropping the secondary pressure to 350
kPa (50 PSIG), then adjusting upward to 410 kPa (60 PSIG).
7. When desired secondary pressure settings have been reached,
push the Knob down to lock this pressure setting.
Figure 1
Lightly grease with provided lubricant.
Inspect for nicks, scratches, and surface imperfections.
If present, reduced service life is probable and
future replacement should be planned.
Clean with lint-free cloth.
Service / Parts Kits Available
Description
B35 (1/8" & 1/4")
Bowl Kits (Includes Bowl Seal)
Polyurethane
BKF35A
Zinc
BKF35D
Zinc (with Sight Gauge)
BKF35W
Cage Kits
CKR35A (“A” Range)
CKR35BC (“B & C” Range)
Filter Element (5 Micron)
EK504VY
Filter Element (20 Micron)
EK504Y
Filter Repair Kit
(Element & Retainer, Deflector)
RKF30
Gauge, 0 to 60 (0 to 4 bar)
K4515N18060
Gauge, 0 to 160 (0 to 11 bar)
K4515N18160
Mounting Bracket
SAR161X57
Piston Drain (Max. Pressure 175 PSIG)
PKF35
Panel Mount Nut
R05X51
Regulator Repair Kit
(Relieving)
RKR30
Regulator Repair Kit
(Non-Relieving)
RKR30K
Adjusting Knob
R35-0545P
Return Spring
SPR-445-1
Bowl Seal
GSK-504Z101