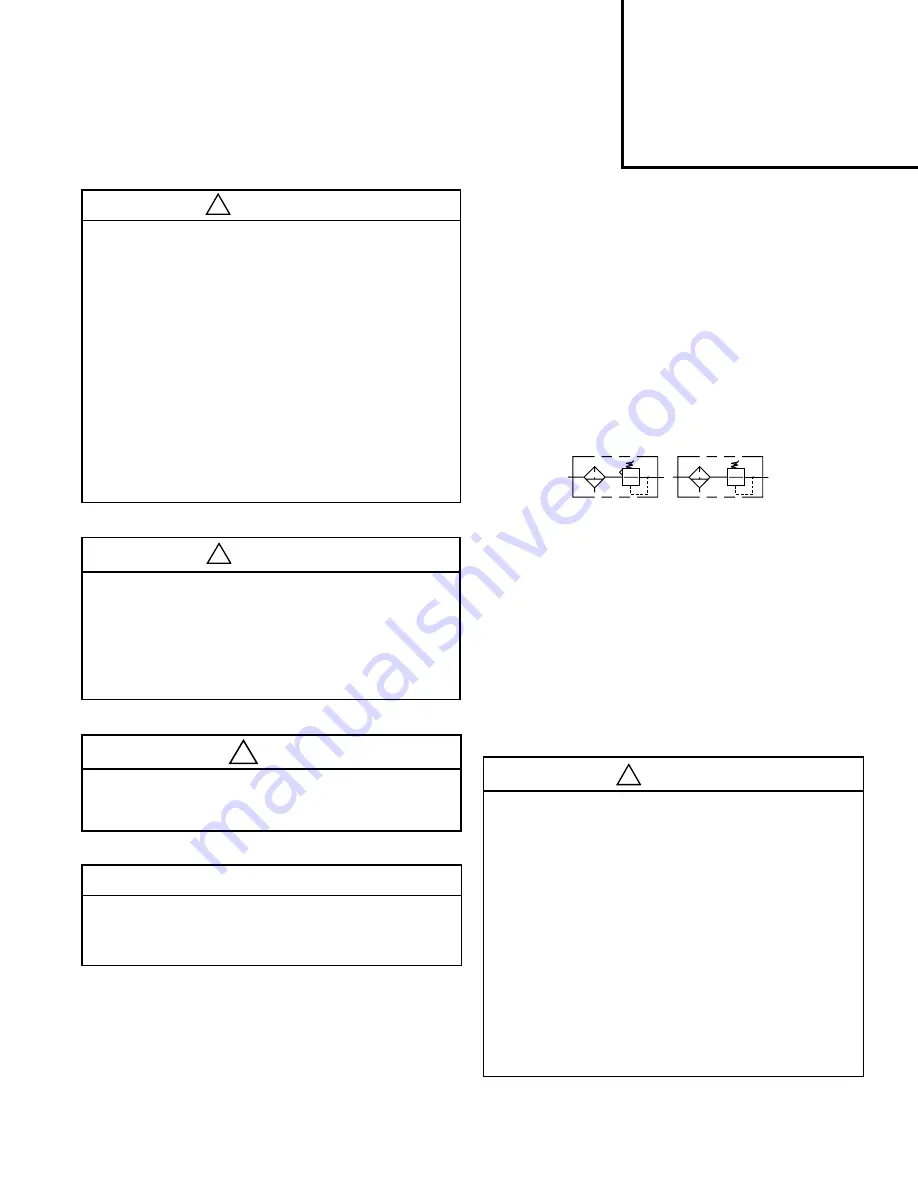
Maximum Recommended Pressure Drop:
kPa PSIG bar
Particulate Filter
70
10
0.7
Operating Pressure Maximum
kPa PSIG bar
Polycarbonate Bowl
1034
150
10.0
Metal Bowl
2068
300
21.0
Metal Bowl with Sight Gauge
1724
250
17.0
Metal Bowl with Piston Drain
1207
175
12.0
Operating Temperature Range
Polycarbonate Bowl
4.4°C to 48.9°C (40°F to 120°F)
Metal Bowl
4.4°C to 82.2°C (40°F to 180°F)
Metal Bowl with Sight Gauge
4.4°C to 65.6°C (40°F to 150°F)
Metal Bowl with Piston Drain
4.4°C to 65.6°C (40°F to 150°F)
Symbols
Filter / Regulator
Installation
1. The Filter / Regulator should be installed with reasonable
accessibility for service whenever possible – repair service kits are
available. Keep pipe or tubing lengths to a minimum with inside
clean and free of dirt and chips. Pipe joint compound should be
used sparingly and applied only to the male pipe – never into the
female port. Do not use PTFE tape to seal pipe joints – pieces have
a tendency to break off and lodge inside the unit, possibly causing
malfunction. Also, new pipe or hose should be installed between the
Filter / Regulator and equipment being protected.
2. The upstream pipe work must be clear of accumulated dirt and
liquids.
3. Select a Filter / Regulator location as close as possible to the
equipment being protected.
Introduction
Follow these instructions when installing, operating, or servicing the
product.
Application Limits
These products are intended for use in general purpose compressed
air systems only.
➤
➤
➤
➤
➤
➤
Pneumatic Division
Richland, Michigan 49083
269-629-5000
!
CAUTION
Polyurethane bowls, sight glass and sight domes on these units may be
attacked by certain chemicals. Never use solvents like carbon tetrachloride,
trichlorethylene, acetone, ketones, certain alcohols, or paint thinner to clean
any parts. These elements can cause crazing or failure of the plastic parts.
The polyurethane resin parts are compatible with most hydrocarbon based
synthetic lubricants but, before using, check with the manufacturer of the
lubricant or oil for compatibility with polyurethane resin.
TO CLEAN POLYURETHANE BOWLS USE MILD SOAP AND WATER
ONLY!
WARNING
FAILURE OR IMPROPER SELECTION OR IMPROPER USE OF
THE PRODUCTS AND/OR SYSTEMS DESCRIBED HEREIN OR
RELATED ITEMS CAN CAUSE DEATH, PERSONAL INJURY
AND PROPERTY DAMAGE.
This document and other information from The Company, its
subsidiaries and authorized distributors provide product and/or
system options for further investigation by users having technical
expertise. It is important that you analyze all aspects of your
application, including consequences of any failure and review
the information concerning the product or systems in the current
product catalog. Due to the variety of operating conditions and
applications for these products or systems, the user, through its
own analysis and testing, is solely responsible for making the
final selection of the products and systems and assuring that all
performance, safety and warning requirements of the application
are met.
The products described herein, including without limitation, product
features, specifications, designs, availability and pricing, are subject
to change by The Company and its subsidiaries at any time without
notice.
EXTRA COPIES OF THESE INSTRUCTIONS ARE AVAILABLE
FOR INCLUSION IN EQUIPMENT / MAINTENANCE MANUALS
THAT UTILIZE THESE PRODUCTS. CONTACT YOUR LOCAL
REPRESENTATIVE.
WARNING
Product rupture can cause serious injury.
Do not connect regulator to bottled gas.
Do not exceed maximum primary pressure rating.
!
!
WARNING
To avoid unpredictable system behavior that can cause personal injury
and property damage:
• Disconnect electrical supply (when necessary) before installation,
servicing, or conversion.
• Disconnect air supply and depressurize all air lines connected to this
product before installation, servicing, or conversion.
• Operate within the manufacturer’s specified pressure, temperature,
and other conditions listed in these instructions.
• Medium must be moisture-free if ambient temperature is below
freezing.
• Service according to procedures listed in these instructions.
• Installation, service, and conversion of these products must be
performed by knowledgeable personnel who understand how
pneumatic products are to be applied.
• After installation, servicing, or conversion, air and electrical supplies
(when necessary) should be connected and the product tested for
proper function and leakage. If audible leakage is present, or the
product does not operate properly, do not put into use.
• Warnings and specifications on the product should not be covered by
paint, etc. If masking is not possible, contact your local representative
for replacement labels.
!
Installation & Service Instructions
IS-B35
B35 Integral Filter / Regulator Series
ISSUED: August, 2006
Supersedes: April, 2006
Doc. #ISB35, ECN #060761, Rev. 3
Safety Guide
For more complete information on recommended application
guidelines, see the Safety Guide section of Pneumatic Division
catalogs or you can download the
Pneumatic Division Safety
Guide
at: www.wattsfluidair.com