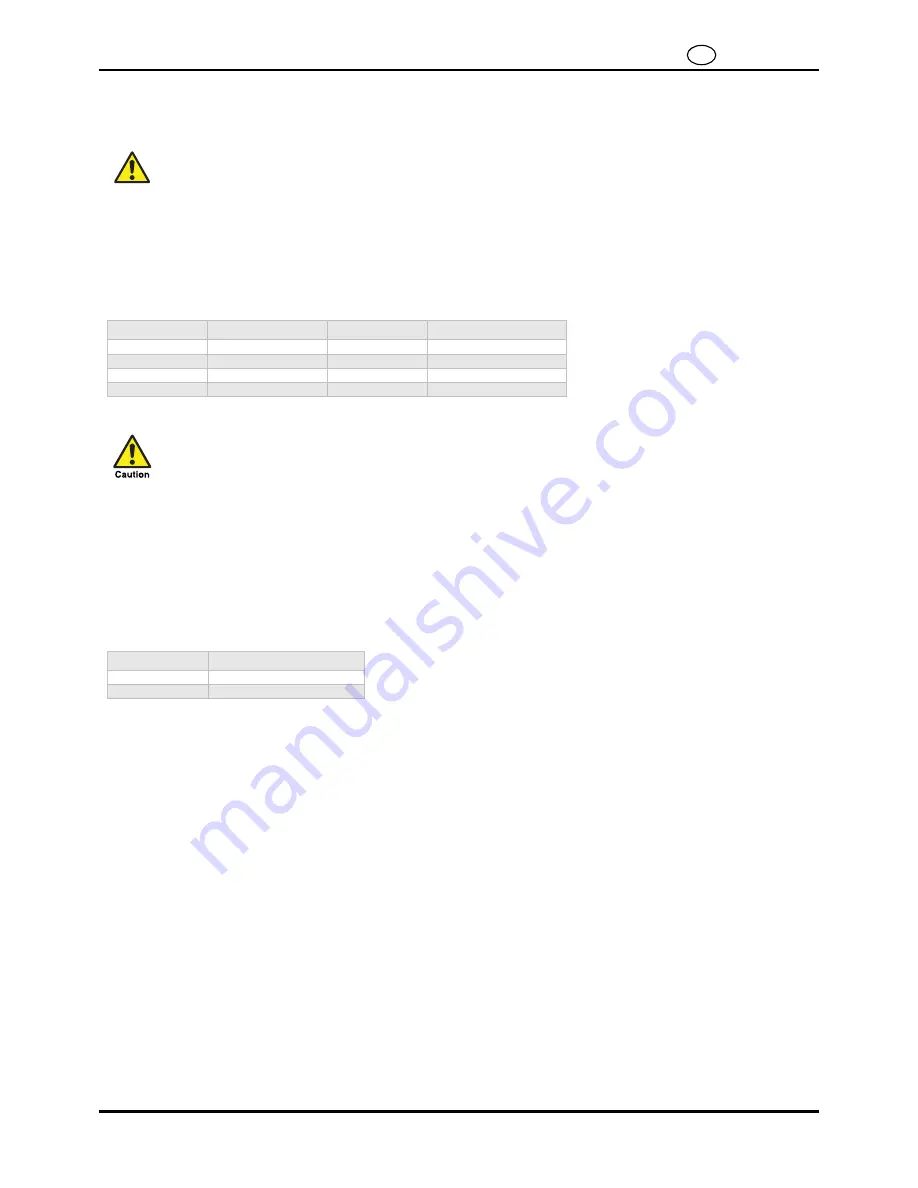
Safety Information
EN
6
3 Installation & Commissioning
3.1 Recommended system layout
The dryer should be installed with the correct pre-filtration and condensate management equipment to meet both the specification and local
environmental requirements.
Referring to diagram A4 in Annex A, the following equipment is recommended to meet these requirements:
3.2 Locating the equipment
Identify a suitable location for the equipment taking into consideration the minimum space requirements for maintenance and lifting equipment.
When considering the final location of the equipment take into account the noise generated when in use.
The dryer can be installed free standing, secured to the floor via the fastener points provided in the base or secured to a wall using the optional
brackets.
Installation Kits
3.3 Mechanical Installation
Once the dryer has been located into position install the piping and filtration for connection to the inlet and outlet manifold. AO grade filtration
can be used at the dryer inlet as shown in diagram A4 of Annex A.
Ensure that each filter condensate drain is suitably piped away and any effluent is disposed of in accordance with local regulations.
Two inlet and two outlet connections are available at the top of the dryer to enable connection from either left or right. Unused connections must
be sealed with the threaded plugs provided.
It is important to ensure that all piping materials are suitable for the application, clean and debris free. The diameter of the pipes must be
sufficient to allow unrestricted inlet air supply to the equipment and outlet gas / air supply to the application.
When routing the pipes ensure that they are adequately supported to prevent damage and leaks in the system.
All components used within the system must be rated to at least the maximum operating pressure of the equipment. It is recommended that the
system be protected with suitably rated pressure relief valves.
A by-pass line may be installed into the system to provide a constant air supply during maintenance.
Only competent personnel trained, qualified, and approved by Parker domnick hunter should perform installation,
commissioning and service procedures.
Ref
Description
Ref
Description
1
Compressor
5
AO filter
2
Wet air receiver
6
AA filter
3
Bypass line
7
Dryer
4
Isolation valves
The use of a bypass line will allow wet untreated air into the system. It should therefore only be used in extreme
circumstances.
Part No.
Description
DASMB1
608204061
DASMB2
608204062
Warning
Summary of Contents for DAS 1
Page 94: ...EL 101 2 2 Parker domnick hunter 2 3 3 2 1 IEC 1 1 1 5 2 6 3 7 4 8 _...
Page 97: ...EL 104 4 4 1 4 2 1 _ 2 3 _ 4 5 _ 6 7 _ 4 3 1 2 3 1 2 3 4 Parker domnick hunter 1 2 3 4 Warning...
Page 98: ...EL 105 5 5 2 Parker domnick hunter 5 1 5 2 6 24 3 6 12 36 _Q _ X E...
Page 187: ...Munkav delmi el r sok HU 201...
Page 214: ...RU 231 Parker domnick hunter 2 3 A3 A 1 IEC 1 1 1 5 2 6 3 7 4 8...
Page 216: ...RU 233 3 4 3 5 7 7 102 7 A B 1 2 C CSA NPT A B C 230V T500mA 115V T1A Brown Blue 1 2...
Page 217: ...RU 234 4 4 1 4 2 1 2 3 4 5 6 7 4 3 1 2 3 1 ON 2 3 4 Parker domnick hunter 1 2 3 4 Warning...
Page 218: ...RU 235 5 5 2 Parker domnick hunter 5 1 5 2 6 24 3 6 12 36 POWER ON STATUS FAULT A B D E...
Page 255: ...Tag rif dwar is Sigurt MT 275 A2 A3 Red Yellow Green Yellow 1 6 7 6 8 4 5 2 1 3...
Page 256: ...Tag rif dwar is Sigurt MT 276 A4 3 4 2 1 5 4 4 7 6...
Page 257: ...Tag rif dwar is Sigurt MT 277 A5 E E E D E A...