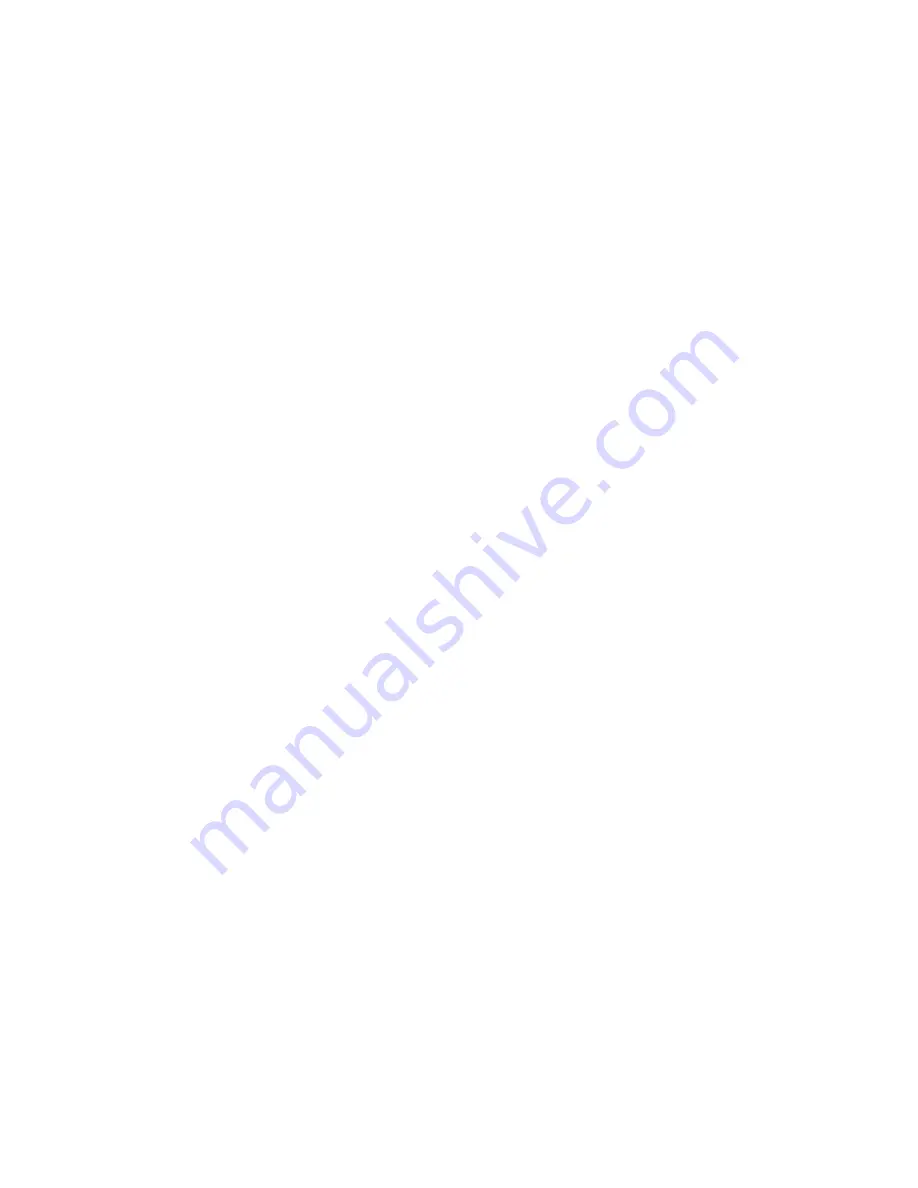
Pneumatic Division Safety Guide
2.7. Chemical Compatibility: For more information on plastic component chemical compatibility see Pneumatic Division technical bulletins
Tec-3, Tec-4, and Tec-5
2.8. Product Rupture: Product rupture can cause death, serious personal injury, and property damage.
• Do not connect pressure regulators or other Pneumatic Division products to bottled gas cylinders.
• Do not exceed the maximum primary pressure rating of any pressure regulator or any system component.
• Consult product labeling or product literature for pressure rating limitations.
3. PRODUCT ASSEMBLY AND INSTALLATION INSTRUCTIONS
3.1. Component Inspection: Prior to assembly or installation a careful examination of the valves, FRLs or vacuum products must be
performed. All components must be checked for correct style, size, and catalog number. DO NOT use any component that displays any
signs of nonconformance.
3.2. Installation Instructions: Parker published Installation Instructions must be followed for installation of Parker valves, FRLs and
vacuum components. These instructions are provided with every Parker valve or FRL sold, or by calling 1-800-CPARKER, or at
www.parker.com.
3.3. Air Supply: The air supply or control medium supplied to Valves, FRLs and Vacuum components must be moisture-free if ambient
temperature can drop below freezing
4. VALVE AND FRL MAINTENANCE AND REPLACEMENT INSTRUCTIONS
4.1. Maintenance: Even with proper selection and installation, valve, FRL and vacuum products service life may be significantly reduced
without a continuing maintenance program. The severity of the application, risk potential from a component failure, and experience
with any known failures in the application or in similar applications should determine the frequency of inspections and the servicing or
replacement of Pneumatic Division products so that products are replaced before any failure occurs. A maintenance program must
be established and followed by the user and, at minimum, must include instructions 4.2 through 4.10.
4.2. Installation and Service Instructions: Before attempting to service or replace any worn or damaged parts consult the appropriate
Service Bulletin for the valve or FRL in question for the appropriate practices to service the unit in question. These Service and
Installation Instructions are provided with every Parker valve and FRL sold, or are available by calling 1-800-CPARKER, or by accessing
the Parker web site at www.parker.com.
4.3. Lockout / Tagout Procedures: Be sure to follow all required lockout and tagout procedures when servicing equipment. For more
information see: OSHA Standard – 29 CFR, Part 1910.147, Appendix A, The Control of Hazardous Energy – (Lockout / Tagout)
4.4. Visual Inspection: Any of the following conditions requires immediate system shut down and replacement of worn or damaged
components:
• Air leakage: Look and listen to see if there are any signs of visual damage to any of the components in the system. Leakage is an
indication of worn or damaged components.
• Damaged or degraded components: Look to see if there are any visible signs of wear or component degradation.
• Kinked, crushed, or damaged hoses. Kinked hoses can result in restricted air flow and lead to unpredictable system behavior.
• Any observed improper system or component function: Immediately shut down the system and correct malfunction.
• Excessive dirt build-up: Dirt and clutter can mask potentially hazardous situations.
Caution: Leak detection solutions should be rinsed off after use.
4.5. Routine Maintenance Issues:
• Remove excessive dirt, grime and clutter from work areas.
• Make sure all required guards and shields are in place.
4.6. Functional Test: Before initiating automatic operation, operate the system manually to make sure all required functions operate
properly and safely.
4.7. Service or Replacement Intervals: It is the user’s responsibility to establish appropriate service intervals. Valves, FRLs and vacuum
products contain components that age, harden, wear, and otherwise deteriorate over time. Environmental conditions can significantly
accelerate this process. Valves, FRLs and vacuum components need to be serviced or replaced on routine intervals. Service intervals
need to be established based on:
• Previous performance experiences.
• Government and / or industrial standards.
• When failures could result in unacceptable down time, equipment damage or personal injury risk.
4.8. Servicing or Replacing of any Worn or Damaged Parts: To avoid unpredictable system behavior that can cause death, personal
injury and property damage:
• Follow all government, state and local safety and servicing practices prior to service including but not limited to all OSHA Lockout
Tagout procedures (OSHA Standard – 29 CFR, Part 1910.147, Appendix A, The Control of Hazardous Energy – Lockout / Tagout).
• Disconnect electrical supply (when necessary) before installation, servicing, or conversion.
• Disconnect air supply and depressurize all air lines connected to system and Pneumatic Division products before installation, service,
or conversion.
• Installation, servicing, and / or conversion of these products must be performed by knowledgeable personnel who understand how
pneumatic products are to be applied.
• After installation, servicing, or conversions air and electrical supplies (when necessary) should be connected and the product tested
for proper function and leakage. If audible leakage is present, or if the product does not operate properly, do not put product or
system into use.
• Warnings and specifications on the product should not be covered or painted over. If masking is not possible, contact your local
representative for replacement labels.
4.9. Putting Serviced System Back into Operation: Follow the guidelines above and all relevant Installation and Maintenance Instructions
supplied with the valve FRL or vacuum component to insure proper function of the system.