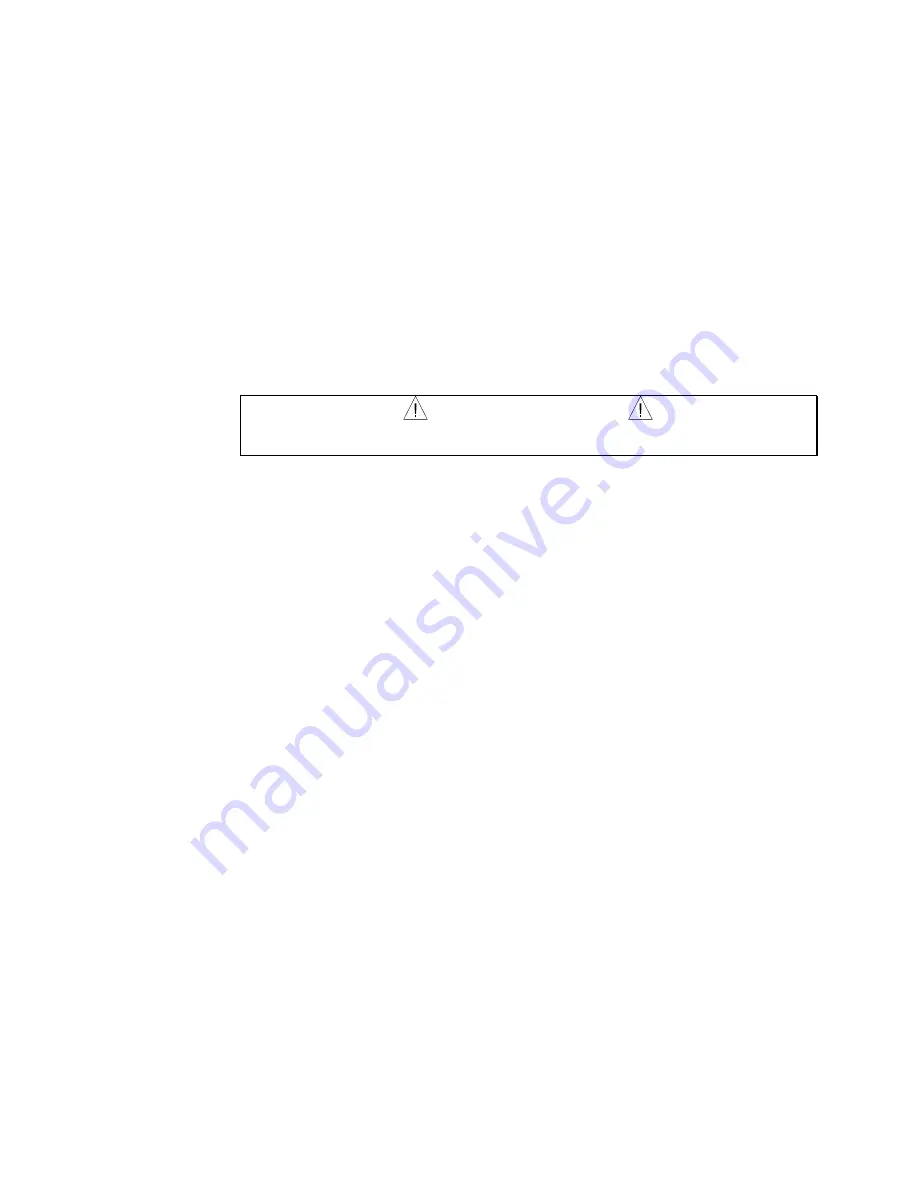
2 4
APEX615n Installation Guide
Disconnecting
Power to the
Controller
Removing power to the controller portion of the APEX615n (
Control L1
and
Control L2
) will
trigger a Drive Fault, plus the controller will issue a "shutdown" signal to the drive that is
equivalent to the
DRIVE0
command.
When power is restored to the controller, the drive will need to be reset using the either the
DRESET
command or the
RESET
Input on the Drive Auxiliary connector. (The
DRESET
command is the equivalent of the
RESET
Input.)
Fusing Information
Recommended fuse sizes are:
APEX6151 (120 VAC):
15-25A slow blow type, Littelfuse p/n 326-025 (or equiv.)
APEX6151 (240 VAC):
12-15A slow blow type, Littelfuse p/n 326-015 (or equiv.)
APEX6152 (240 VAC):
12A slow blow type, Littelfuse p/n 326-012 (or equivalent)
APEX6154 (240 VAC):
20A slow blow type, Littelfuse p/n 326-020 (or equivalent)
WARNING
The APEX615n has no internal fuses. For safety purposes, provide a fuse in each of the AC
input lines.
The actual input power and current is a function of the motor's operating point (speed and
torque) and the duty cycle. The fuse value given above is for a drive and motor operating at
rated speed and rated torque at 100% duty. You can de-rate the fuse by scaling the above value
by your actual requirements.
Artisan Technology Group - Quality Instrumentation ... Guaranteed | (888) 88-SOURCE | www.artisantg.com