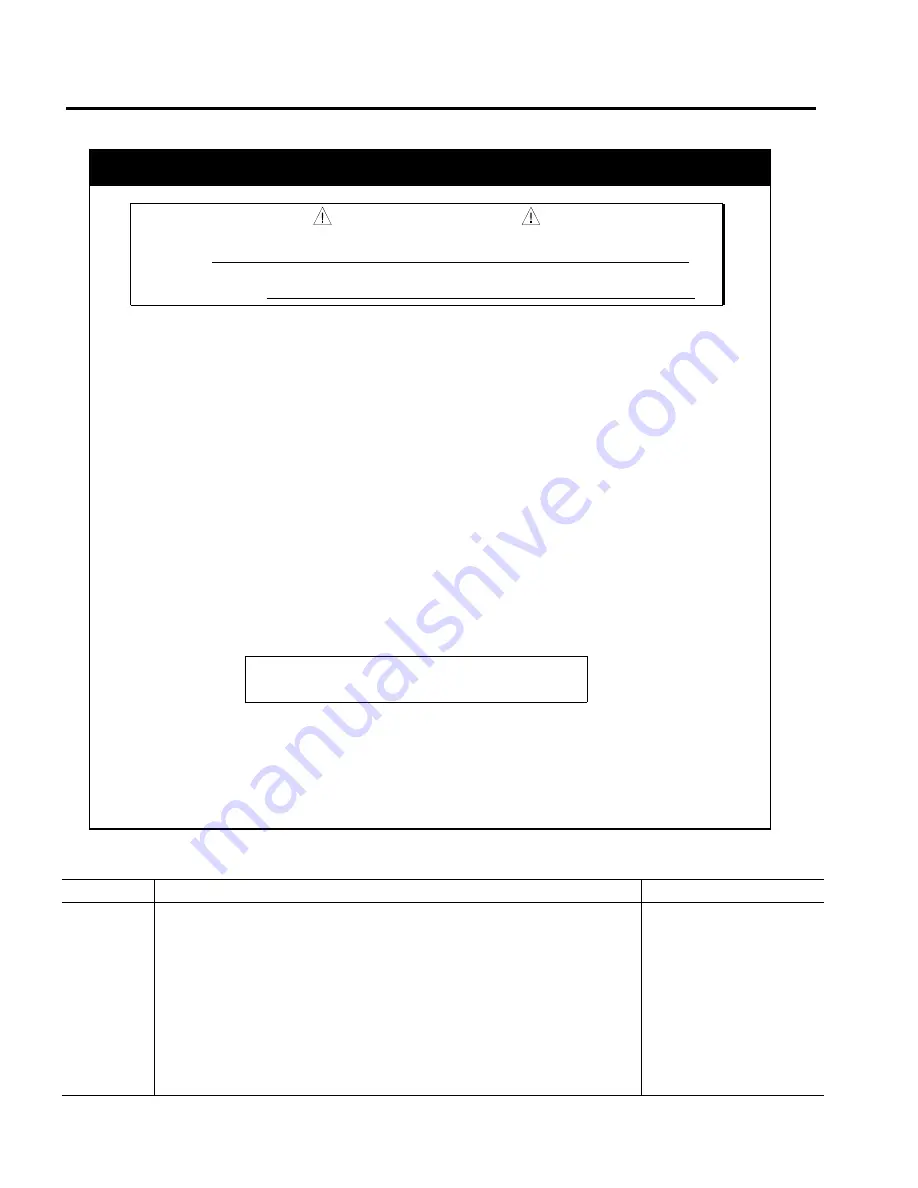
2 2
AT6250/AT6450 Installation Guide
Testing the Installation
Test Setup
WARNING
¥ The test procedures below require you to exercise the I/O connected to your AT6n50 system;
therefore, make sure that exercising the I/O will not damage equipment or injure personnel.
¥ The procedures below are designed to be executed with the drives not connected to the
AT6n50; therefore, do not proceed until you have disconnected the drives from the AT6n50.
¥
Terminal Emulation
.
To communicate with the AT6n50, you will need a terminal emulation program. We
recommend you use Motion Architect, a Windows-based program that is included in your ship kit. Motion
Architect provides terminal emulation and program editor features as part of its ensemble of programming tools.
Using Motion Architect:
1 . Power up the AT6n50 AUX board.
2 . To install Motion Architect, insert Disk 1 into your computerÕs disk drive and run the Setup program
(setup.exe). Follow the instructions in the Setup program.
NOTE
: Be sure to install the driver and
operating system files for your product. The Setup program will prompt you for the Ò6000 Driver and
SamplesÓ disk and your productÕs ÒOperating System and DOS Support SoftwareÓ disk (you can find these
disks in your AT6n50 ship kit).
3 . In the Setup programÕs last dialog (indicating that Motion Architect has been installed successfully), select
ÒYes, I want to run Motion Architect nowÓ and click the ÒFinishÓ button to launch Motion Architect.
4 . From Motion ArchitectÕs main menu, click on the ÒProductÓ pull-down menu and click on ÒSelectionÓ to
invoke the Ò6000 Series Product SelectionÓ dialog box. In the dialog box, select ÒAT6250Ó or ÒAT6450Ó
and click the Okay button.
5 . From Motion ArchitectÕs main menu, click on ÒTerminalÓ to launch the terminal emulator.
6 . Download the operating system by clicking on the ÒTransfersÓ pull-down menu and selecting ÒSend
Operating SystemÓ. After the operating system is downloaded, the terminal window will display a startup
message, followed by a command prompt (
>
); this indicates that you are communicating with the AT6n50:
* PARKER COMPUMOTOR AT6N50 - N AXIS SERVO CONTROLLER
* ANALOG INPUT OPTION NOT INSTALLED
>
¥
Verify Factory Settings
.
The test procedures below are based on the factory-default active levels for the
AT6n50Õs inputs and outputs. Verify these settings with the following
status
commands:
Command Entered
Response Should Be
INLVL
.................................
*INLVL¯¯¯¯_¯¯¯¯_¯¯¯¯_¯¯¯¯_¯¯¯¯_¯¯¯¯_¯¯¯¯
HOMLVL
...............................
*HOMLVL¯¯¯¯
LHLVL
.................................
*LHLVL¯¯¯¯_¯¯¯¯
OUTLVL
...............................
*OUTLVL¯¯¯¯_¯¯¯¯_¯¯¯¯_¯¯¯¯_¯¯¯¯_¯¯¯¯_¯¯¯¯
Connections
Test Procedure
Response Format
(left to right)
End-of-travel
and
Home Limits
NOTE
: If you are not using end-of-travel limits, issue the Disable Limits (
@LH¯
) command
and ignore the first two bits in each response field.
1. Enable the hardware end-of-travel limits with the
@LH3
command.
2. Close the end-of-travel switches and open the home switches.
3. Enter the
TLIM
command. The response should be
*TLIM11¯_11¯_11¯_11¯
.
4. Open the end-of-travel switches and close the home switches.
5. Enter the
TLIM
command. The response should be
*TLIM¯¯1_¯¯1_¯¯1_¯¯1
.
6. Close the end-of-travel switches and open the home switches (return to original config.).
7. Enter the
TLIM
command. The response should be
*TLIM11¯_11¯_11¯_11¯
.
TLIM
response format:
bit 1 = Axis 1 positive (CW) limit
bit 2 = Axis 1 negative (CCW) limit
bit 3 = Axis 1 home (HOM) limit
bit 4 = Axis 2 positive (CW) limit
bit 5 = Axis 2 negative (CCW) limit
bit 6 = Axis 2 home (HOM) limit
bit 7 = Axis 3 positive (CW) limit
bit 8 = Axis 3 negative (CCW) limit
bit 9 = Axis 3 home (HOM) limit
bit 10 = Axis 4 positive (CW) limit
bit 11 = Axis 4 negative (CCW) limit
bit 12 = Axis 4 home (HOM) limit
ÒCWÓ means positive travel.
ÒCCWÓ means negative travel.
ÒHOMÓ means home.
Artisan Technology Group - Quality Instrumentation ... Guaranteed | (888) 88-SOURCE | www.artisantg.com
Summary of Contents for Compumotor 6000 Series
Page 5: ...Artisan Technology Group Quality Instrumentation Guaranteed 888 88 SOURCE www artisantg com...
Page 7: ...Artisan Technology Group Quality Instrumentation Guaranteed 888 88 SOURCE www artisantg com...
Page 33: ...Artisan Technology Group Quality Instrumentation Guaranteed 888 88 SOURCE www artisantg com...
Page 53: ...Artisan Technology Group Quality Instrumentation Guaranteed 888 88 SOURCE www artisantg com...
Page 57: ...Artisan Technology Group Quality Instrumentation Guaranteed 888 88 SOURCE www artisantg com...