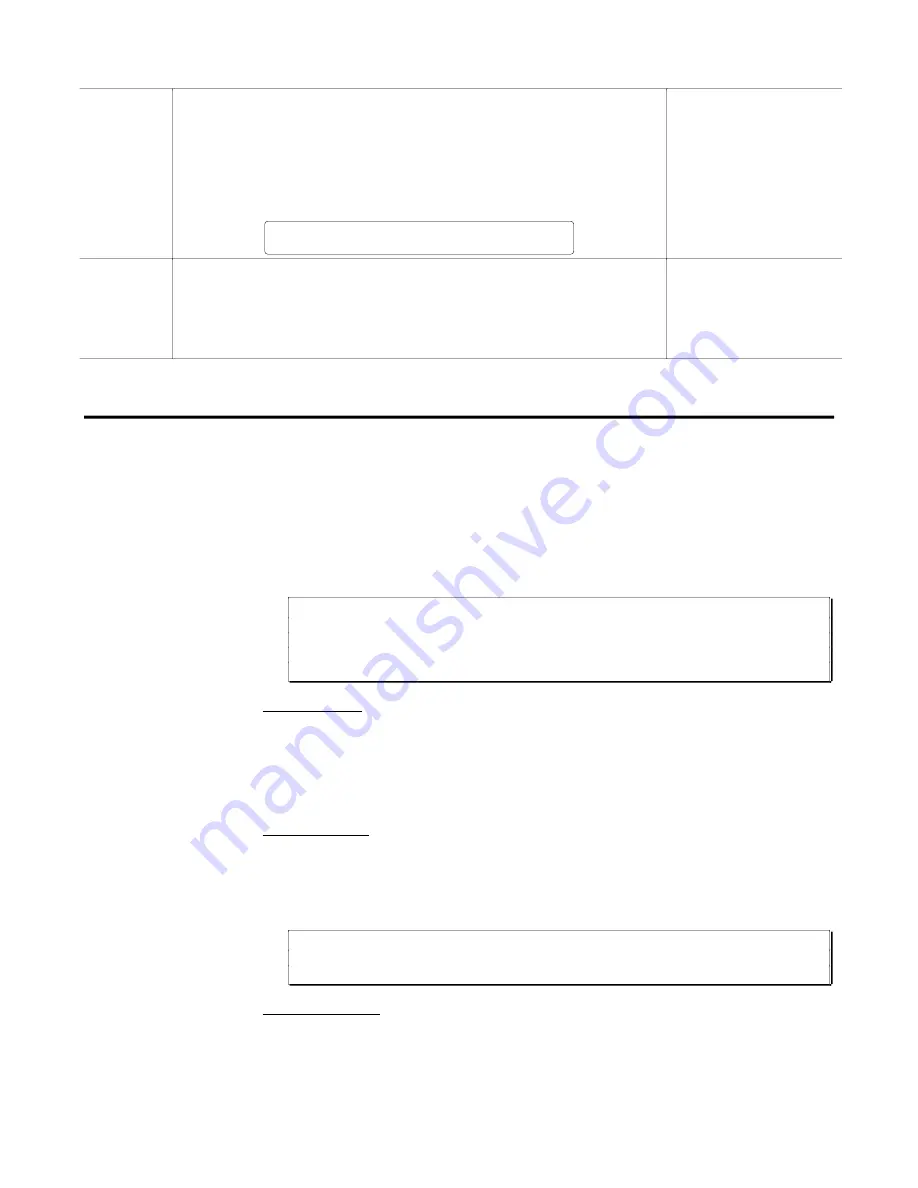
➂
Installation
21
I n s t a l l a t i o n V e r i f i c a t i o n ( c o n t . )
RP240
➀
Cycle power to the 6250.
➁
If the RP240 is connected properly, the RP240's status LED should be green and one of the
messages on the computer or terminal display should read
*RP24Ø CONNECTED
.
If the RP240's status LED is off, check to make sure the +5V connection is secure.
If the RP240's status LED is green, but the message on the terminal reads
*NO REMOTE
PANEL
, the RP240 Rx and Tx lines are probably switched. Remove power and correct.
➂
Assuming you have not written a program to manipulate the RP240 display, the RP240
screen should display the following:
COMPUMOTOR 6250 SERVO CONTROLLER
RUN JOG STATUS DRIVE DISPLAY ETC
Joystick inputs
➀
Open the joystick input switches or turn off the device driving the inputs.
➁
Enter the
TINO
command.
The response should be
*TINOØØØØ_Ø1ØØ
.
➂
Close the input switches or turn on the device driving the inputs.
➃
Enter the
TINO
command.
The response should be
*TINO1111_11ØØ
.
TINO
response:
bit 1 = joystick auxiliary
bit 2 = joystick trigger
bit 3 = joystick axes select
bit 4 = joystick velocity select
bit 5 = joystick release
bit 6 = Enable input
bits 7 & 8 are not used
➃
What's Next?
At this point you should have successfully completed this chapter's mounting, connection, and
test procedures for your 6250 system. If you intend to use thumbwheels or PLCs, or if you
intend to daisy-chain multiple 6250s, refer to the connection instructions and application
considerations provided in Chapter 5.
The following steps are recommended to prepare you for applying the 6250 in your
application.
Step
➀
Couple the Load
Couple the motor to the load, and couple the encoder to the motor (or load, as appropriate).
Step
➁
Perform the Basic System Configuration
N O T E
The set-up commands referred to in this step are not saved in the 6250's battery-
backed RAM. Therefore, we suggest you add them to the startup (
STARTP
) program.
For information in defining the startup program, refer to
Automatic Program Execution on
Power Up in Chapter 7, Programming Tips.
Number of Axes:
By configuring the number of axes in use, you limit the number of axes you can control.
This may be desired if you are only using one of the two axes available. The
INDAX
command configures the number of axes.
INDAX2
(the default setting) requires both
command fields to be entered (e.g.,
A1,1
). If you enter
INDAX1
, instead of entering
A1,1
you should enter
A1
, and all responses from the 6250 will also only show the one
field; if you enter the command
A
, the response will be
*A1
.
Drive Fault Level:
The drive fault level (
DRFLVL
) should be set to active high or active low for each axis
(default is active low—
DRFLVLØ
). This output is active high (
DRFLVL1
) for the
OEM670 and APEX series drives, and active low for the BL, UD2, UD5, and UD12
drives. If you are using the Dynaserv or any other drive that does not have a drive fault
output, set the drive fault level to active low (
DRFLVLØ
).
N O T E
Once the drive fault level has been configured, you must enable the drive fault input with
the
INFEN
command before the input is usable.
Encoder Resolution:
The encoder resolution is determined by the resolution of the encoder used with the servo
drive/motor system. The encoder resolution is essentially the number of steps, or counts
(post quadrature), per unit of travel. For example, Compumotor E Series encoders are
1,000-line encoders, and therefore have a 4,000 count/rev post-quadrature resolution.