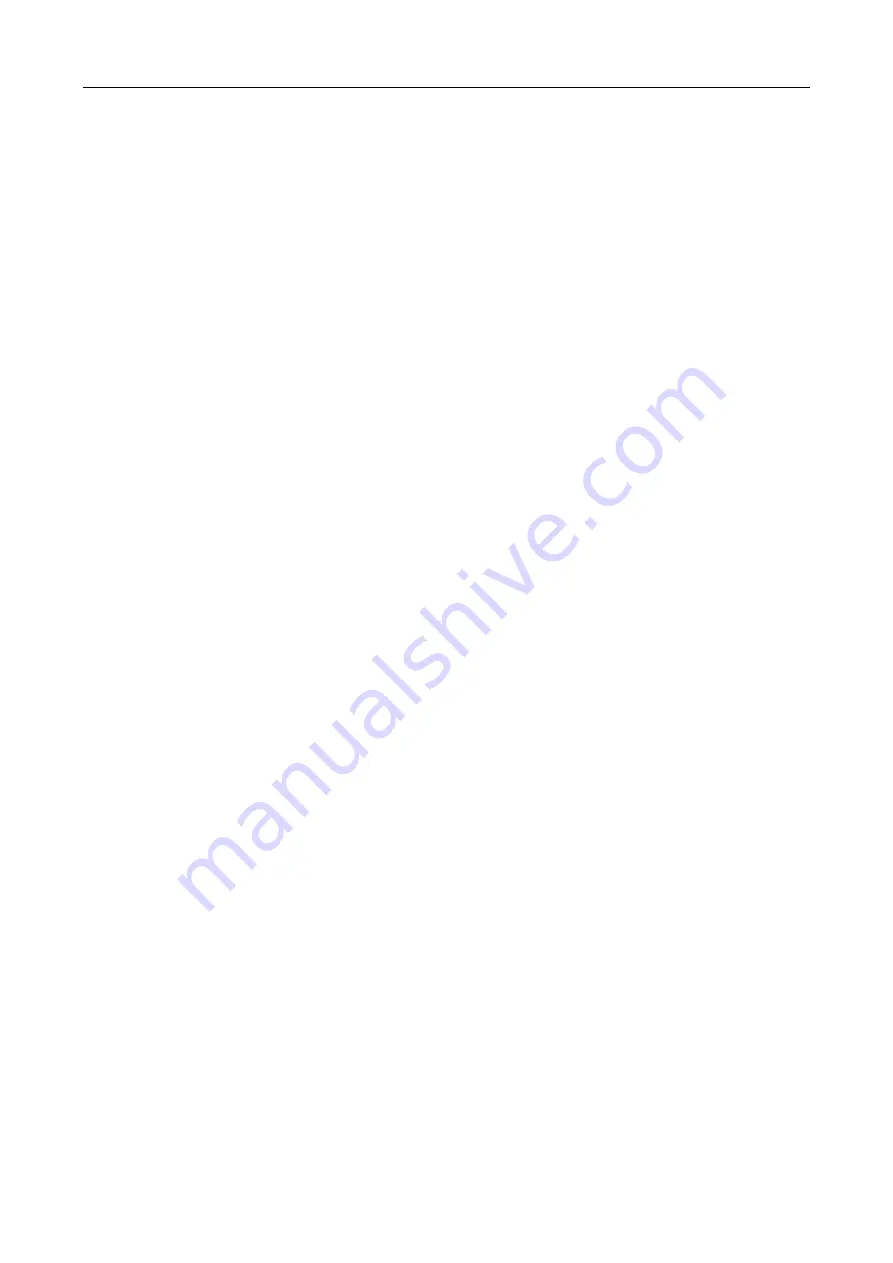
4-7
Setting up & Commissioning
514C Product Manual
RUNNING PERFORMANCE ADJUSTMENTS
GENERAL
If the controller is operating in tachogenerator mode the IR compensation potentiometer (P8)
must be anti-clockwise.
The Proportional and Integral potentiometers (P3, P4, P6, P7) as preset by Parker Hannifin
Manufacturing Limited will provide stable and responsive performance under most load
conditions. Thus if instability is observed it is important to first check the load and coupling:
If there is a cyclic variation of the armature current check the mechanical couplings to the
load - this is a common cause of apparent instability in either the speed or motor current. If
speed instability is present check whether the repetition rate of the instability is related to the
mechanical revolution of the load - if it is then the instability frequency will vary with speed.
This form of instability may be reduced by adjustment of the drive presets, but total
elimination of the problem may require improvement of the load characteristics.
Instability due to incorrect setting of the drive control parameters can occur and is
recognisable because its frequency will be independent of the motor speed. If this form of
instability is present, or if the application demands that the drive is trimmed for optimum
response, then the stability controls may be adjusted as follows. Note that while the speed
stability and response may be improved without the use of a Diagnostic Unit or Oscilloscope
it is difficult to optimise the current response without such instrumentation. Consequently,
the following procedure assumes that both instruments are available.
Current Loop Adjustment (P6 and P7)
1.
With all power supplies disconnected, disconnect the field wires from terminals F+ and F-
labelling each wire clearly so that it can later be reconnected with the correct polarity.
Connect the Stall Override terminal T15 to +10v.
NOTE:
(i) It is now possible to operate the motor in a stalled condition. Great care must be taken
not to damage the motor by overheating. If the motor is fitted with a force ventilation
fan, arrange that it is connected and running during the test. In any case
DO NOT
remain in the stalled condition for long periods.
(ii) Although the field supply is disconnected the motor may still produce some torque due
to residual or compound field flux. It is essential therefore, to mechanically lock the
motor shaft, or apply sufficient load to prevent rotation during the following procedure.
2.
The optimum setting of the Current Proportional and Integral presets (P6 and P7) depends, to
some extent, on the setting of the Main Current Limit (P5). Thus P5 should be correctly
adjusted to suit the load, before adjustment of P6 and P7 is attempted.
3.
When the Main Current Limit control is correctly set, proceed as follows:
Ensure that a step change can be applied to the speed setpoint path.
Connect the Diagnostic Unit to the Control printed circuit board. Connect the Oscilloscope to
the output sockets on the Diagnostic Unit and switch to Diagnostic 26. This provides access
to a safe, isolated signal representing the armature current waveform where
1.1v =
100%
full load current.
4.
Reconnect the supplies, switch on and RUN. Observe the armature current waveform while
changing the polarity of the Current Demand signal (by varying the Speed Setpoint). With each
change of Current Demand polarity the current should increase rapidly, but without overshoot