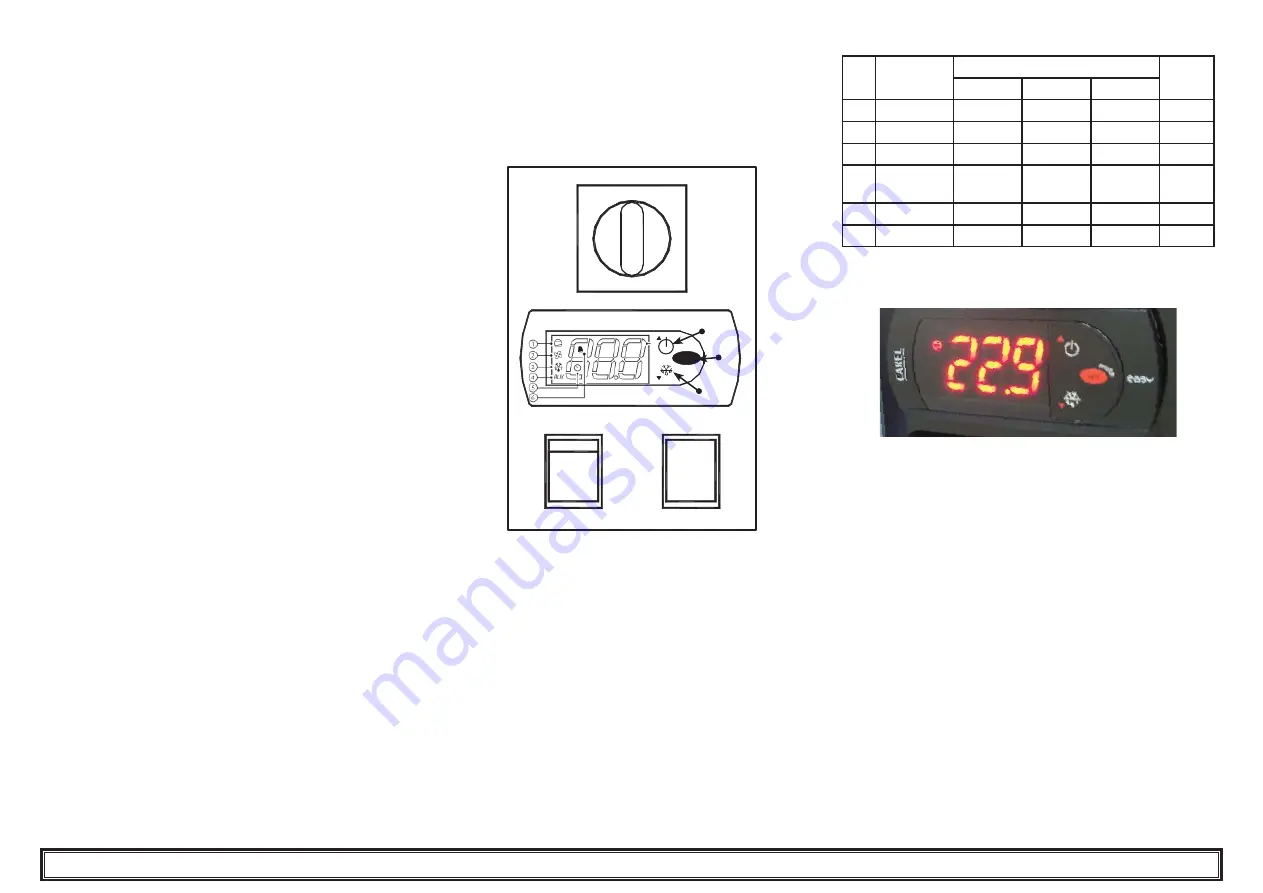
English
ICE003-005
3 / 6
ity of the expansion vessel as well.
3.4 Electrical
circuit
3.4.1.
Checks and connections
!
Before carrying out any operation on the electrical system, make
sure that the appliance is disconnected from the electrical power sup-
ply.
All electrical connections must comply with the applicable regulations
in force in the country of installation.
Initial checks
1) Th
e power supply voltage and frequency must correspond to the
values stamped on the chiller nameplate. Th
e power supply charac-
teristics must not deviate, even for brief periods, from the tolerance
limits indicated on the electrical diagram , which are +/- 10% for the
voltage; +/- 1% for the frequency.
2) Th
e voltage must be supplied with phase and neutral conductors,
and the latter must be connected to earth in its own cabin (TN
system, or behalf of the supply company, TT system). Th
e phase
conductor and the neutral conductor are not interchangeable and
must not be confused..
Connection
1) Th
e electrical power supply must be connected to the chiller using a
3-wire cable, comprising 2 phase conductors and an earth conductor.
For minimum cable section, see par. 7.2.
2) Pass the cable through the cable entry on the rear panel of the ma-
chine and connect the phase and neutral to the terminals of the main
isolator switch (QS); connect the earth wire to the earth terminal
(PE).
3) Ensure that supply cable has at its source protection against direct
contact of at least IP2X or IPXXB.
4)On the supply line to the chiller, install a residual-current circuit
breaker with a trip rating of (RCCB - IDn = 0.3A), with the current
rating indicated in the reference electrical diagram, and with a short
circuit current rating appropriate to the short circuit fault current
existing in the machine installation area.
Th
e nominal current In of the magnetic circuit breaker must be
equal to the FLA with an intervention curve type D.
5) Max. grid impedance value = 0.274 ohm.
Subsequent checks
Check that the machine and the auxiliary equipment are earthed and
protected against short circuit and/or overload.
!
Once the unit has been connected and the upstream main switch
closed (thereby connecting the power supply to the machine), the
voltage in the electrical circuit will reach dangerous levels. Maximum
caution is required!
3.4.2. ON/OFF
remoto
All the chillers can be connected to a remote ON/OFF control.
See the electrical diagram for the connection of the remote ON-OFF
contact.
4 Control
4.1 Control
panel
Fig.1
MUTE
SET
O
I
QS
S1
H1
A
B
C
QS
Isolator
switch
S1
On / Off switch: enables pump startup and activates the
control
A
UP key:
used to increase the value of a parameter.
B
SET key:
used to access parameter programming f
unctions.
C
DOWN key:
used to decrease the value of a parameter.
H1
red:
Indicates the presence of machine alarms.
N°
function
normal operations
start
up
ON
OFF
fl ash
1
compressor
on
off --
--
2
fan
--
--
--
--
3
defrost
--
--
--
--
4
auxiliary
output
--
--
--
--
5
clock (RTC)
--
--
--
--
6
alarm
--
--
--
--
Photo 1
(display in operation)
4.2
Starting the chiller
• Connect the power supply to the machine by turning the main
isolator switch QS to On.
• Switch on the chiller as follows: press the On/Off [S1] switch to On.
• Set the desired temperature on the controller.
4.2.1.
Adjustments at commissioning
a) Th
e chiller is set for operation at a default temperature of 12 °C with
a diff erential of 3 °C; to adopt a new setting, see heading 4.5.
b) Verify correct operation of the pump, using the pressure gauge
(read P1 and P0) and checking the pressure limit values (Pmax and
Pmin) indicated on the pump data plate.
P1 = pressure with pump ON
P0 = pressure with pump OFF
Pmin < (P1-P0) < Pmax
- Example n°1.
Conditions:
closed circuit, pressure P0 = 2 bar
pump data plate values: Pmin 1 bar/ Pmax 3 bar
adjust the valve outlet to give a pressure of 3 bar < P1< 5 bar
- Example n°2.
Conditions:
open circuit, pressure P0 = 0 bar
pump data plate values: Pmin 1 bar/ Pmax 3 bar