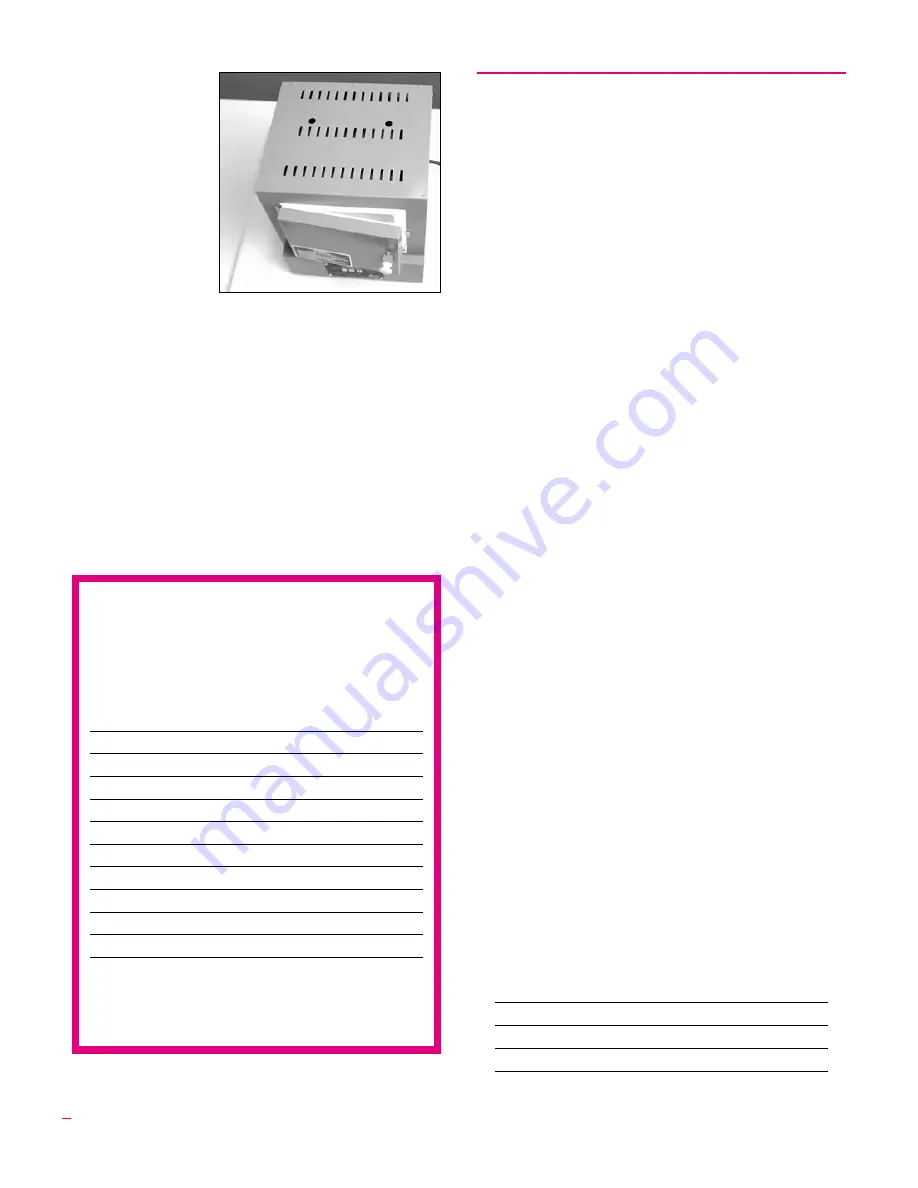
China paints will
crack or peel if ap-
plied heavily. Apply
several light coats in-
stead, firing between
each, until you get the
shade you want. Not
all china paint colors
reach
maximum
color saturation at the
same temperature
even when fired on
the same ware. So you
must know which col-
ors you should fire
first at higher tem-
peratures to prevent burning out the original colors in later
firings. For example, reds mature at a lower temperature
than other colors and are fired after the other colors have
been fired. Reds and yellows should not be fired side by side.
Colors also mature at a lower temperature on ceramic pieces
than on porcelain or hard china. Check the overglaze manu-
facturer’s literature for information on which cone to use
with each color and type of ware.
Vent the door during the first hour of firing. If your kiln
has a vent hole, leave it open during the entire firing. Allow
kiln to cool to room temperature before opening the door.
Lost Wax Burnout
Caution:
Only kilns with vent holes are designed
for lost wax burnout. However, you can use a kiln
without the vent hole provided that you open the
door ½” during venting.
Caution:
Always use a wax tray.
Caution:
If your kiln’s heating element is embed-
ded in the floor of the firing chamber, place the
metal wax tray on 3 or 4 - ½” posts inside the kiln.
This prevents the element from possibly shorting
out against the tray.
Note:
These instructions apply to injection wax that
melts at 200°F, not pattern waxes and plastics that
melt at higher temperatures. If smoke appears dur-
ing wax elimination, turn off the kiln. Smoking wax
means the kiln fired hotter than 300°/148°C.
Overview
Lost wax casting is the process of carving a shape in wax ,
and then casting that shape in metal. After the wax has been
carved, a mold is made of the wax shape. The mold is a nega-
tive image of the wax. The wax is later melted out of the mold
through hollow channels called sprues.
Lost wax burnout is the process of preparing a casting
mold for the melted metal that will be poured into it. The
steps in lost wax burnout:
1
Melt the wax from the mold.
2
Remove wax from the kiln before raising the tem-
perature higher than 300°F/148°C.
3
Harden the mold at high temperature.
4
Maintain the mold at the casting temperature rec-
ommended for the type of metal that will be poured
into the mold.
Caution:
Prevent wax or carbon from contacting
the kiln’s walls and elements. Carbon build-up in-
side a kiln ruins the interior. Carbon conducts elec-
tricity and causes elements to short circuit. Damage
to elements from contact with foreign materials is
not covered by warranty.
A Sample Program
See your digital controller instruction manual to enter
this program:
Rate
Temp.
Segment
°F/°C
°F/°C
Hold
1
500/277
300/148
01.00
2
500/277
1350/732
01.00
3
450/250
800/426
02.00
14
Open the door ½” to vent the kiln if your kiln
does not have vent holes.
Temperature Equivalents For Orton
Self-Supporting Pyrometric Cones
Cone
Cone
Self-Supporting Cones
Pre-Fire
Number
Color
Heated at: 27° F
108° F
270° F
Per Hour* Per Hour* Per Hour*
022
—
1087
1094
Green
021
—
1112
1143
Fuschia
020
—
1159
1180
Orange
019
1213
1252
1283
Yellow
018
1267
1319
1353
White
017
1301
1360
1405
Pink
016
1368
1422
1465
Light Blue
015
1382
1456
1504
Violet
014
1395
1485
1540
Gray
013
1485
1539
1582
Green
012
1549
1582
1620
Fuschia
*Rate of temperature increase during last 90 - 120
minutes of firing. Tables by courtesy of the Edward
Orton, Jr. Ceramic Foundation.