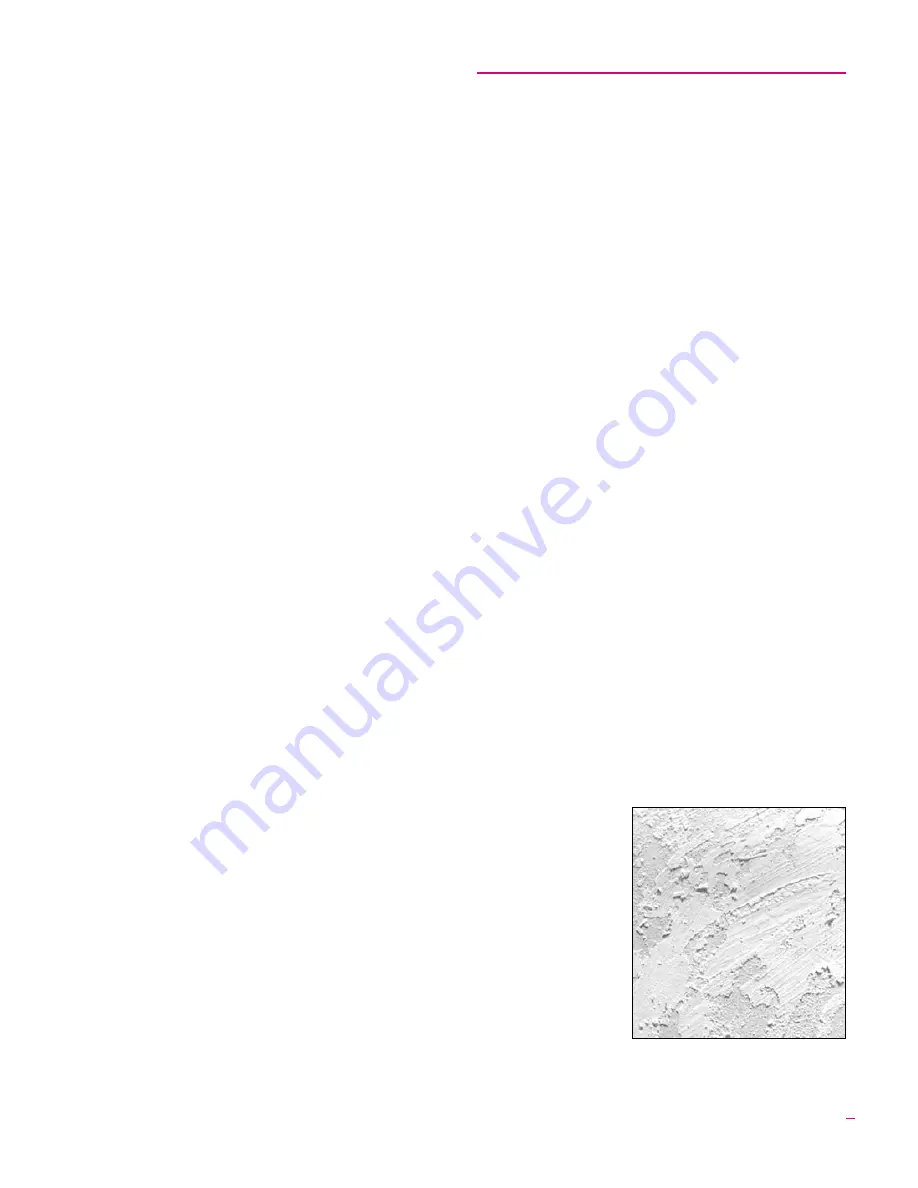
Segment 1 heats the wax to 300°F/148°C and holds it for
one hour, allowing it to drip from the mold.
Segment 2 hardens the mold.
Segment 3 lowers temperature to 800°F/426°C, the typi-
cal casting temperature for silver. (Most types of gold cast at
900°F/482°C.)
Note:
Casting temperature depends on the size of
the mold. The temperatures above are only a guide.
See your jewelry supply dealer for temperature
recommendations.
Burnout Instructions
1
Place a metal tray inside the kiln on three ½” posts.
Place the mold on a wire mesh screen on top of the
tray. The mold’s sprue hole should be down. The tray
will catch melting wax as it drips from the sprue hole.
2
Keep the kiln’s vent hole(s), if any, open during wax
elimination. If the kiln has no vent hole, leave the
door open ½”. This allows fumes to escape from the
kiln. Heat the kiln to 300°F/148°C and hold it at that
temperature for at least one hour.
Note:
Do NOT heat the wax above 300°F/148°C.
Hold at 300°F/148°C for at least one hour. During
this hour, the wax will melt from the mold and drip
into the tray. If the kiln gets hotter than
300°F/148°C, the wax may smoke and deposit car-
bon inside your kiln, causing expensive damage.
3
After one hour at 300°F/148°C, open the kiln. Remove
the mold and wax tray. Pour the wax from the tray and
leave the tray out of the kiln until your next wax elimi-
nation. (Do not leave the tray in the kiln!)
4
Heat the mold to the temperature recommended by
your jewelers’ supply house where you purchased the
mold material. This is usually around 1350°F/732°C.
5
Lower the temperature to the casting temperature of
the metal. Hold at that temperature until you are
ready to begin casting. Remove the mold with tongs.
Wear protective gloves and safety glasses.
Saving a Carbon-Damaged Kiln
If you follow the above directions, your kiln should be safe
from wax damage. In some cases, a small amount of carbon
may form on the walls over a period of time. This is due to the
burning of wax residue that was left in the mold. For this rea-
son we recommend that you periodically fire the kiln to
1500°F/815°C as follows:
1
Open the vent cover(s) or leave the door ajar ½”.
2
Fire the kiln empty to 1500°F/815°C at a rate of
300°F/166°C with a one hour hold (01.00).
Firing Mistakes
Silver Clay
Cracks
Cracks that appear in fired silver clay may be due to too
much water in the silver clay before it was fired. Another
cause is careless handling of a dried, unfired piece. To re-
pair, fill the crack with silver clay and fire again.
Brittle
Silver clay will not reach full strength if underfired. You
may be able to save the piece by firing again to the correct
temperature and hold.
Too Much Shrinkage
When silver clay is overfired, it shrinks too much and
loses detail. If the kiln is firing hotter than the temperature
programmed, check the position of the thermocouple (see
page 17, bottom left column). Replace the thermocouple if it
is old.
Glass
Glass Cracking
Probable Causes:
I
Heating the Kiln Too Fast
I
Cooling the Kiln Too Fast
I
Fusing Incompatible Glass
I
Not Enough Glass Separator on Shelf
Most problems in fusing are caused by rushing the firing.
The glass must change temperature slowly during the criti-
cal temperature range of 100° - 500° F / 37° - 260°C. This
critical range applies to both heating and cooling.
The second critical temperature range is annealing,
which is the cooling range of 950° - 700° F / 510° - 371°C aver-
age. Cool the glass slowly during this range so the stress in
the glass will have time to dissipate.
If you become im-
patient after the glass
has fused and you
crack open the door of
the kiln for a few sec-
onds to peek inside,
you may hear a “ping,”
which is the sound of
glass cracking. Avoid
the temptation to open
the door. Wait until the
kiln has cooled to room
temperature. Some
artists schedule their
fusing so that it is com-
pleted before they go to
bed. That way they will
15
Flaking glass separator can cause the
glass to crack. This is because the glass
sticks to the shelf.