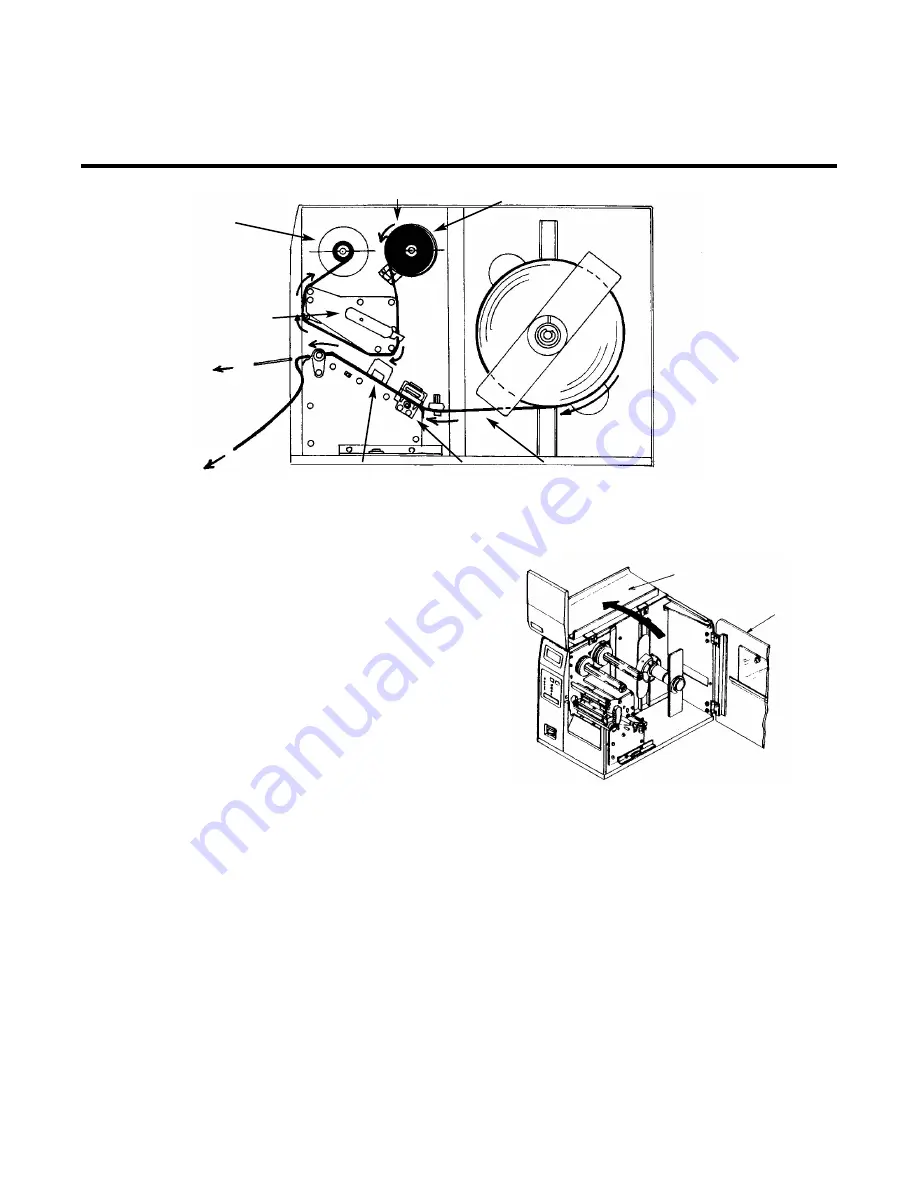
PANDUIT TDP4*H
GMTDPH-MAN
Page 2-8
Section 2: Installation
1. Open the Top Access Door by swinging it up and
to the left and the Side Access Door by swinging it
toward the rear of the printer.
2. Open the Print Head by rotating the Head Latch
toward the rear of the printer. The Print Head is
spring-loaded and will automatically open as soon
as the Head Latch is disengaged.
3. Locate the extra ribbon core supplied with the
printer. Place the core on the Ribbon Rewind
spindle, pushing it all the way to the inside of the
spindle. Note that the new empty core of each
subsequent roll becomes the next rewind core.
4. Load the ribbon onto the Ribbon Supply Spindle, also pushing it all the way to the inside of the
spindle. the dull side of the ribbon should be facing down as it travels through the Print Head
Assembly.
5. Feed the leader portion of the ribbon through the Print Head Assembly and up to the Ribbon Rewind
spindle following the routing shown in the diagram.
6. Load the ribbon behind and over the top of the Ribbon Rewind spindle and tape it to the Extra Ribbon
Core. Make sure it matches the ribbon path shown in the diagram.
7. Manually turn the Rewind spindle to wrap the ribbon onto the core one to two turns to secure it.
Loading the Ribbon
Ribbon Roll
Ribbon Path
Ribbon Rewind
Spindle
Head Latch
Dispensed
Label
Label Backing
Sensor
Assembly
Label
Hold
Down
Label Patch
Top Access Door
Side Access Door
Summary of Contents for TDP43H
Page 1: ...TDP42H TDP43H TDP46H Thermal Transfer Printer OPERATOR MANUAL GMTDPH MAN...
Page 12: ...PANDUIT TDP4 H GMTDPH MAN Page 1 8 Section 1 Overview Notes...
Page 26: ...PANDUIT TDP4 H GMTDPH MAN Page 2 14 Section 2 Installation Notes...
Page 60: ...PANDUIT TDP4 H GMTDPH MAN Page 4 6 Section 4 Cleaning and Maintenance Notes...
Page 66: ...PANDUIT TDP4 H GMTDPH MAN Page 5 6 Section 5 Troubleshooting Notes...
Page 83: ......
Page 84: ......