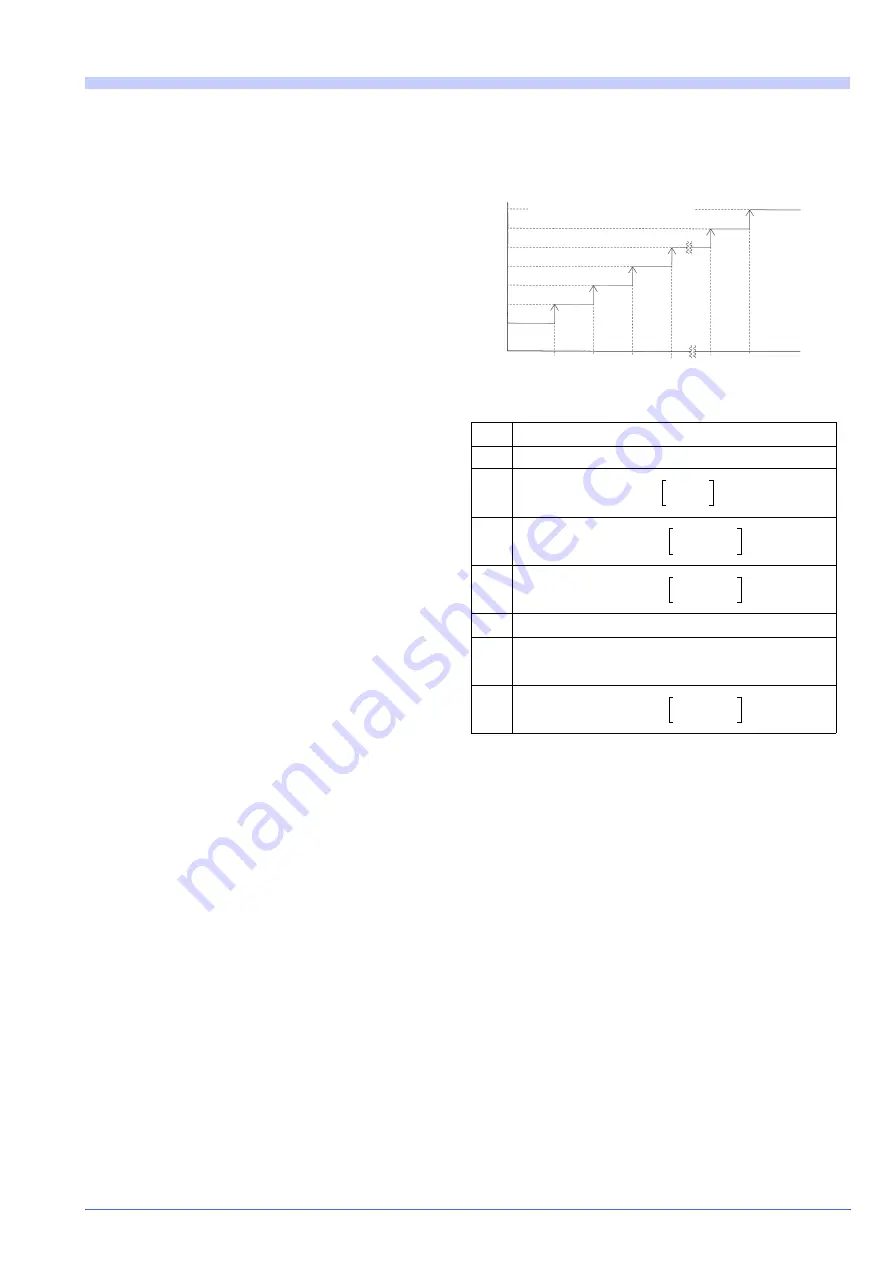
Advanced functions
29
7.5
Signal-up
It is a function to increase the welding current at the
preset current incremental rate every time the “Step-up
shift” input is given.
This sequence is completed when the welding current
reaches or exceeds the maximum current.
(
1
)
Set the DIP switch DPSW1-10 to ON (selecting
“Signal-up”).
(
2
)
In the setting mode, set the SOL No., and then set
the current incremental rate. (The set-up conditions
can be set for SOL
I
and SOL
II
separately.)
(
3
)
Press “RUN” key and press the “ENTER/SHIFT” key
three times, then the current accumulated current
incremental rate is displayed.
(
4
)
When the welding current (based on the
accumulated current incremental rate) reaches or
exceeds the preset maximum current, the “Signal-up
completion output” (the same output as that for the
step-up completion) is turned on, the “COUNT UP”
lamp of the “STEP-UP CNTR. (MONITOR)” lights,
and the buzzer sounds.
• After that, even if the “step-up shift” input is turned
on, the input is ignored and the operation is
continued at the maximum current while maintaining
the output.
(
5
)
If the set value for they current incremental rate is
changed, during the operation, the newly set
incremental rate is added to the current accumulated
current incremental rate.
<Signal-up procedure>
Welding current
0
Preset current value
1
Preset current value x
2
Preset current value x
3
Preset current value x
:
n-1
Preset current value x
n
Preset current value x
<Note>
• “S
u
“indicates set value for the signal-up current
incremental rate (0 - 9%).
W
elding cu
rrent
“Step-up shift” input
1st
2nd 3rd
(n-1)th (n)th
Maximum current (I Max)
1
S
u
100
---------
+
1
S
u
100
---------
2
×
+
1
S
u
100
---------
3
×
+
1
S
u
100
---------
n
1
–
(
)
×
+
1
S
u
100
---------
n
×
+
Summary of Contents for YF-0201Z5HGF
Page 22: ...TSMP222 TSM222 ...
Page 33: ...8 Circuit diagram Circuit diagram 33 TSMP222 YF 0201Z5HGF Circuit diagram ...
Page 37: ......