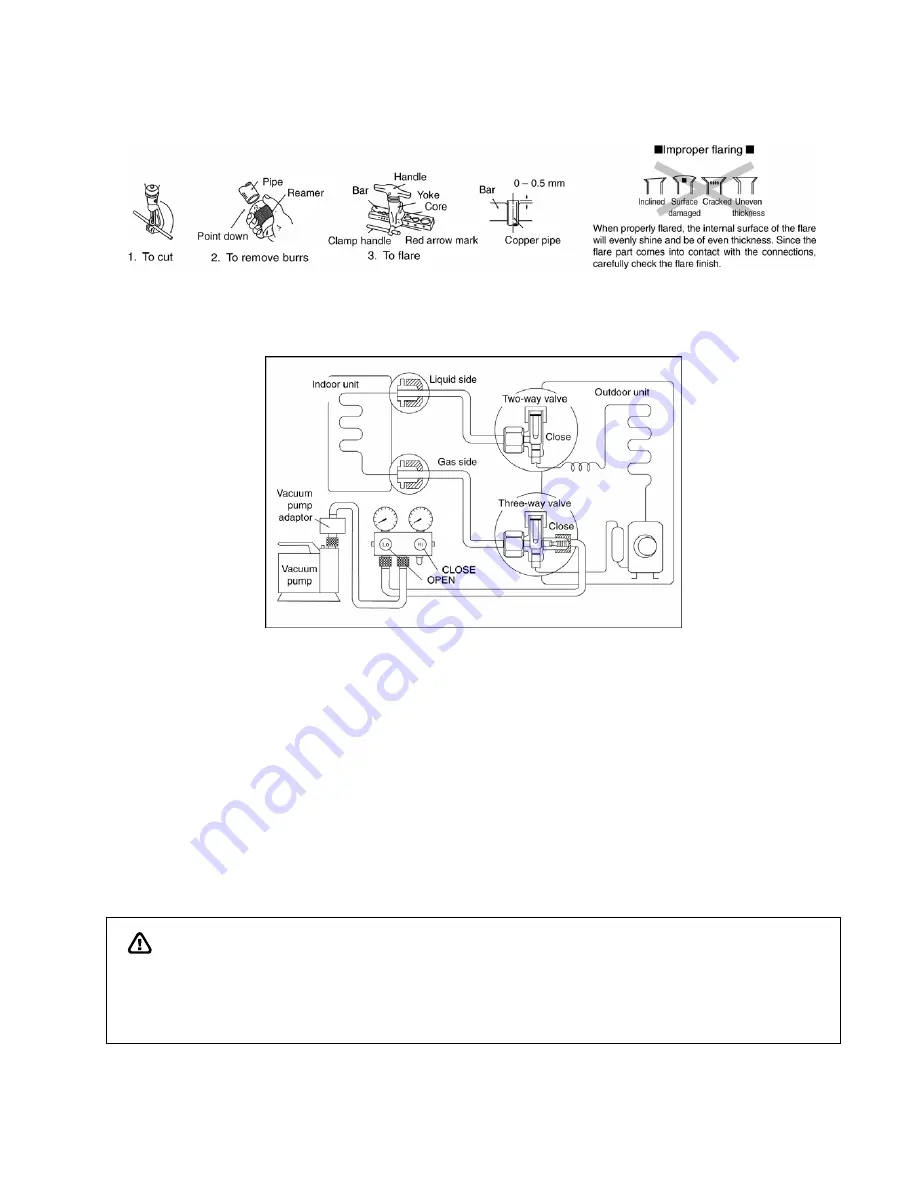
43
CAUTION
Cutting and Flaring the Piping
1 Please cut using pipe cutter and then remove the burrs.
2 Remove the burrs by using reamer. If burrs is not removed, gas leakage may be caused.
Turn the piping end down to avoid the metal powder entering the pipe.
3 Please make flare after inserting the flare nut onto the copper pipes.
11.4.3 Evacuation of the Equipment
WHEN INSTALLING AN AIR-TO-WATER HEATPUMP, BE SURE TO EVACUATE THE AIR INSIDE THE INDOOR
UNIT AND PIPES in the following procedure.
1 Connect a charging hose with a push pin to the Low side of a charging set and the service port of the 3-way
valve.
o
Be sure to connect the end of the charging hose with the push pin to the service port.
2 Connect the center hose of the charging set to a vacuum pump with check valve, or vacuum pump and
vacuum pump adaptor.
3 Turn on the power switch of the vacuum pump and make sure that the needle in the gauge moves from
0 cmHg (0 MPa) to –76 cmHg (–0.1 MPa). Then evacuate the air approximately ten minutes.
4 Close the Low side valve of the charging set and turn off the vacuum pump. Make sure that the needle in the
gauge does not move after approximately five minutes.
Note: BE SURE TO FOLLOW THIS PROCEDURE IN ORDER TO AVOID REFRIGERANT GAS LEAKAGE.
5 Disconnect the charging hose from the vacuum pump and from the service port of the 3-way valve.
6 Tighten the service port caps of the 3-way valve at a torque of 18 N•m with a torque wrench.
7 Remove the valve caps of both of the 2-way valve and 3-way valve. Position both of the valves to “OPEN”
using a hexagonal wrench (4 mm).
8 Mount valve caps onto the 2-way valve and the 3-way valve.
o
Be sure to check for gas leakage.
If gauge needle does not move from 0 cmHg (0 MPa) to –76 cmHg (–0.1 MPa), in step
3
above take the following measure:
If the leak stops when the piping connections are tightened further, continue working from step
3
.
If the leak does not stop when the connections are retightened, repair location of leak.
Do not release refrigerant during piping work for installation and reinstallation. Take care of the liquid refrigerant,
it may cause frostbite.
Summary of Contents for WH-SDC09C3E8
Page 14: ...14 4 Location of Controls and Components 4 1 Indoor Unit 4 1 1 Location of Control ...
Page 15: ...15 ...
Page 16: ...16 ...
Page 17: ...17 4 1 2 Weekly Timer Setting ...
Page 18: ...18 4 1 3 Setting Up the Special Functions ...
Page 19: ...19 4 1 4 Main Components 4 2 Outdoor Unit ...
Page 20: ...20 5 Dimensions 5 1 Indoor Unit ...
Page 21: ...21 5 2 Outdoor Unit ...
Page 23: ...23 ...
Page 24: ...24 7 Block Diagram 7 1 WH UD09CE8 ...
Page 25: ...25 7 2 WH UD12CE8 WH UD14CE8 WH UD16CE8 ...
Page 26: ...26 8 Wiring Connection Diagram 8 1 Indoor Unit 8 1 1 WH SDC09C3E8 ...
Page 27: ...27 8 1 2 WH SDC12C9E8 WH SDC14C9E8 WH SDC16C9E8 ...
Page 28: ...28 8 2 Outdoor Unit ...
Page 29: ...29 9 Electronic Circuit Diagram 9 1 Indoor Unit 9 1 1 WH SDC09C3E8 ...
Page 30: ...30 9 1 2 WH SDC12C9E8 WH SDC14C9E8 WH SDC16C9E8 ...
Page 31: ...31 9 2 Outdoor Unit ...
Page 32: ...32 10 Printed Circuit Board 10 1 Indoor Unit 10 1 1 Main Printed Circuit Board ...
Page 33: ...33 10 1 2 Solar Printed Circuit Board Optional ...
Page 34: ...34 10 2 Outdoor Unit 10 2 1 Main Printed Circuit Board ...
Page 35: ...35 10 2 2 Noise Filter Printed Circuit Board ...
Page 50: ...50 Solar Priority is Set Solar Priority is Not Set ...
Page 53: ...53 Heat Tank Heating No Priority Solar Priority Set ...
Page 54: ...54 Heat Tank Heating No Priority Solar Priority Not Set ...
Page 64: ...64 Solar Priority Not Set Heat Tank Mode Heating Priority Set ...
Page 65: ...65 Tank Mode Solar Priority Set Solar Priority Not Set ...
Page 113: ...113 17 3 To Remove Pressure Gauge 17 4 To Remove Control Panel ...
Page 114: ...114 17 5 To Remove RCCB 17 6 To Remove Transformer and Electronic Controller Board ...
Page 137: ...137 19 2 WH UD09CE8 WH UD12CE8 WH UD14CE8 WH UD16CE8 ...
Page 138: ...138 ...