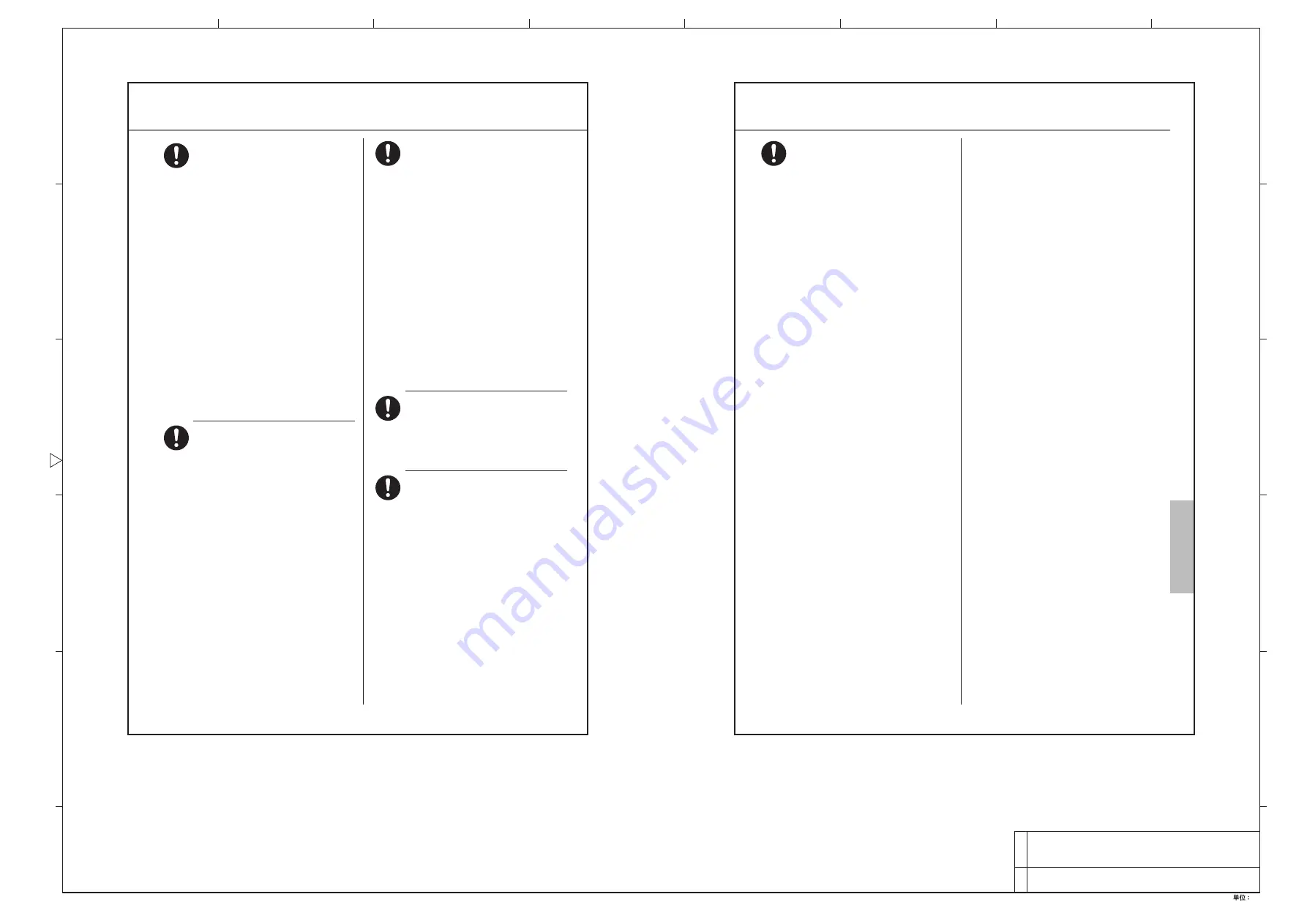
Panasonic Appliances Air-Conditioning Malaysia Sdn. Bhd. & Panasonic Appliances Air-Conditioning R & D Malaysia Sdn. Bhd.
1
2
3
4
5
6
7
8
A
B
C
D
E
F
A
B
C
D
E
F
A3
UNIT : mm
NAME
OPERATING INSTRUCTIONS ( 7 / 11 )
CODE NO.
ACXF55-18700
10
Safety precautions
e) If a vacuum is not possible, make a manifold
so that refrigerant can be removed from
various parts of the system.
f) Make sure that cylinder is situated on the
scales before recovery takes place.
g) Start the recovery machine and operate
in accordance with manufacturer’s
instructions.
h) Do not over
¿
ll cylinders. (No more than 80
% volume liquid charge).
i) Do not exceed the maximum working
pressure of the cylinder, even temporarily.
j) When the cylinders have been
¿
lled
correctly and the process completed, make
sure that the cylinders and the equipment
are removed from site promptly and all
isolation valves on the equipment are
closed off.
k) Recovered refrigerant shall not be charged
into another refrigeration system unless it
has been cleaned and checked.
• Electrostatic charge may accumulate and
create a hazardous condition when charging
or discharging the refrigerant.To avoid
¿
re or
explosion, dissipate static electricity during
transfer by grounding and bonding containers
and equipment before charging/discharging.
11. Labelling
• Equipment shall be labelled stating that it
has been de-commissioned and emptied of
refrigerant.
• The label shall be dated and signed.
• Ensure that there are labels on the equipment
stating the equipment contains
À
ammable
refrigerant.
12. Recovery
• When removing refrigerant from a system,
either for servicing or decommissioning,
it is recommended good practice that all
refrigerants are removed safely.
• When transferring refrigerant into cylinders,
ensure that only appropriate refrigerant
recovery cylinders are employed.
• Ensure that the correct number of cylinders
for holding the total system charge are
available.
• All cylinders to be used are designated for
the recovered refrigerant and labelled for
that refrigerant (i.e. special cylinders for the
recovery of refrigerant).
• Cylinders shall be complete with pressure
relief valve and associated shut-off valves in
good working order.
• Recovery cylinders are evacuated and, if
possible, cooled before recovery occurs.
9. Charging procedures
• In addition to conventional charging
procedures, the following requirements shall
be followed.
- Ensure that contamination of different
refrigerants does not occur when using
charging equipment.
- Hoses or lines shall be as short as possible
to minimize the amount of refrigerant
contained in them.
- Cylinders shall be kept upright.
- Ensure that the refrigeration system is
earthed prior to charging the system with
refrigerant.
- Label the system when charging is
complete (if not already).
- Extreme care shall be taken not to over
¿
ll
the refrigeration system.
• Prior to recharging the system it shall be
pressure tested with OFN (refer to #7).
• The system shall be leak tested on completion
of charging but prior to commissioning.
• A follow up leak test shall be carried out prior
to leaving the site.
• Electrostatic charge may accumulate and
create a hazardous condition when charging
and discharging the refrigerant.To avoid
¿
re
or explosion, dissipate static electricity during
transfer by grounding and bonding containers
and equipment before charging/discharging.
10. Decommissioning
• Before carrying out this procedure, it is
essential that the technician is completely
familiar with the equipment and all its details.
• It is recommended good practice that all
refrigerants are recovered safely.
• Prior to the task being carried out, an oil
and refrigerant sample shall be taken in
case analysis is required prior to re-use of
reclaimed refrigerant.
• It is essential that electrical power is available
before the task is commenced.
a) Become familiar with the equipment and
its operation.
b) Isolate system electrically.
c) Before attempting the procedure ensure
that:
• mechanical handling equipment is
available, if required, for handling
refrigerant cylinders;
• all personal protective equipment is
available and being used correctly;
• the recovery process is supervised at all
times by a competent person;
• recovery equipment and cylinders conform
to the appropriate standards.
d) Pump down refrigerant system, if possible.
11
English
• The recovery equipment shall be in good
working order with a set of instructions
concerning the equipment that is at hand and
shall be suitable for the recovery of
À
ammable
refrigerants.
• In addition, a set of calibrated weighing scales
shall be available and in good working order.
• Hoses shall be complete with leak-free
disconnect couplings and in good condition.
• Before using the recovery machine, check
that it is in satisfactory working order, has
been properly maintained and that any
associated electrical components are sealed
to prevent ignition in the event of a refrigerant
release.Consult manufacturer if in doubt.
• The recovered refrigerant shall be returned to
the refrigerant supplier in the correct recovery
cylinder, and the relevant Waste Transfer
Note arranged.
• Do not mix refrigerants in recovery units and
especially not in cylinders.
• If compressors or compressor oils are to
be removed, ensure that they have been
evacuated to an acceptable level to make
certain that
À
ammable refrigerant does not
remain within the lubricant.
• The evacuation process shall be carried
out prior to returning the compressor to the
suppliers.
• Only electric heating to the compressor body
shall be employed to accelerate this process.
• When oil is drained from a system, it shall be
carried out safely.
Safety precautions