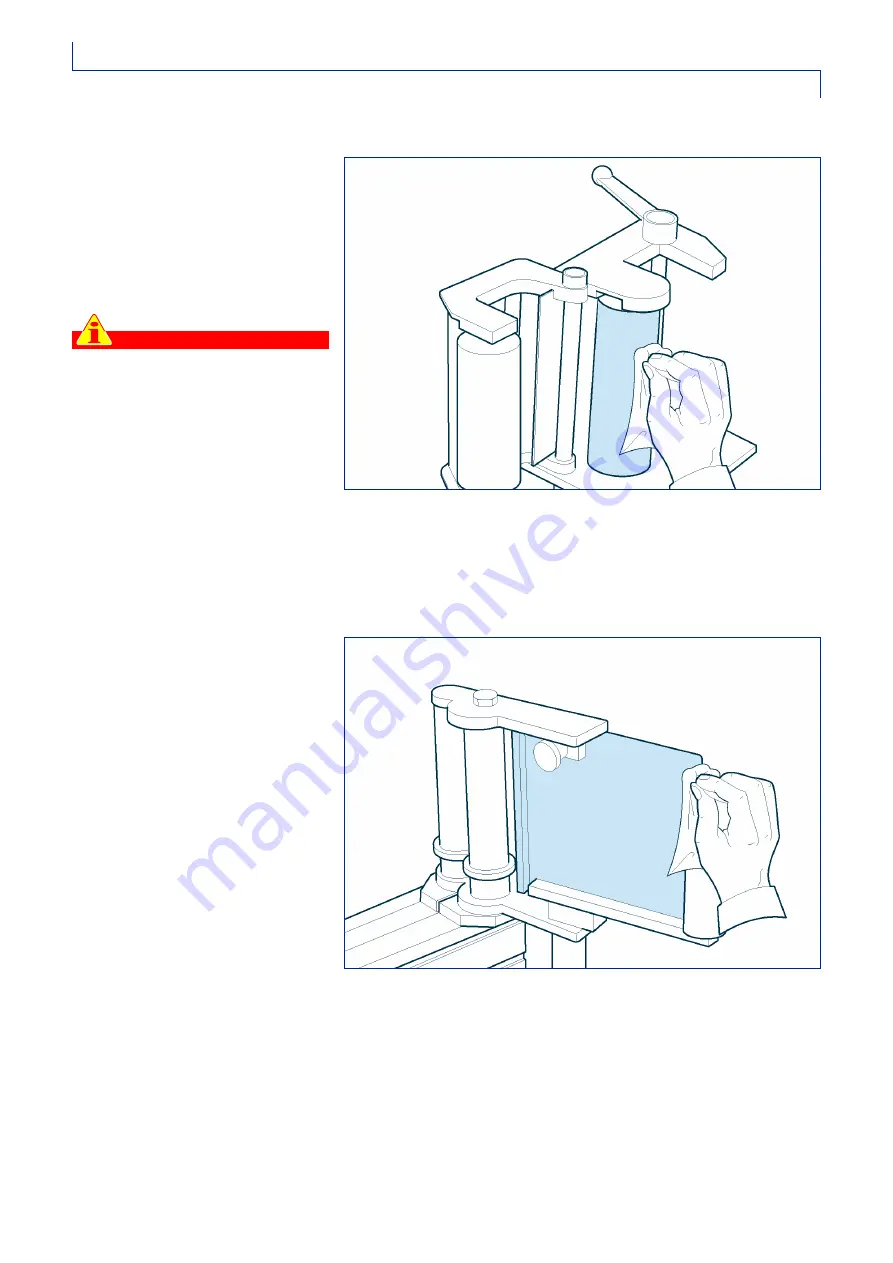
Section 5
LABELING UNIT
-
31
-
English
F
412
0501
00.fm
ID
M
version:
Module 40/60/90/120
CLEANING THE RUBBER ROLLER/COUNTER-ROLLER
Proceed as follows.
1 -Open the driving unit and clean
with a cloth dipped in a liquid
detergent. Do not use sharp tools
that could damage the surface
treatment.
2 -Dry thoroughly after cleaning.
Important
This is usually the most heavily-
soiled area. If spirit or citric acid
based detergents are not effective,
ask the supplier of the labels which
solvent is most suitable for
removing the adhesive without
damaging the rubber. If necessary,
dismantle the counter-roller
assembly as illustrated in the section
“Changing the driving rollers” to
clean them more thoroughly.
CLEANING THE LABEL DETACHING BLADE
1 -Clean the edges of the label
detaching blade with a cloth dipped
in detergent.
2 -If necessary, dismantle the label
detaching blade as explained in the
section “Changing the label
detaching blade” to clean it more
accurately.
IDM-41200602900.tif
IDM-41200603000.tif