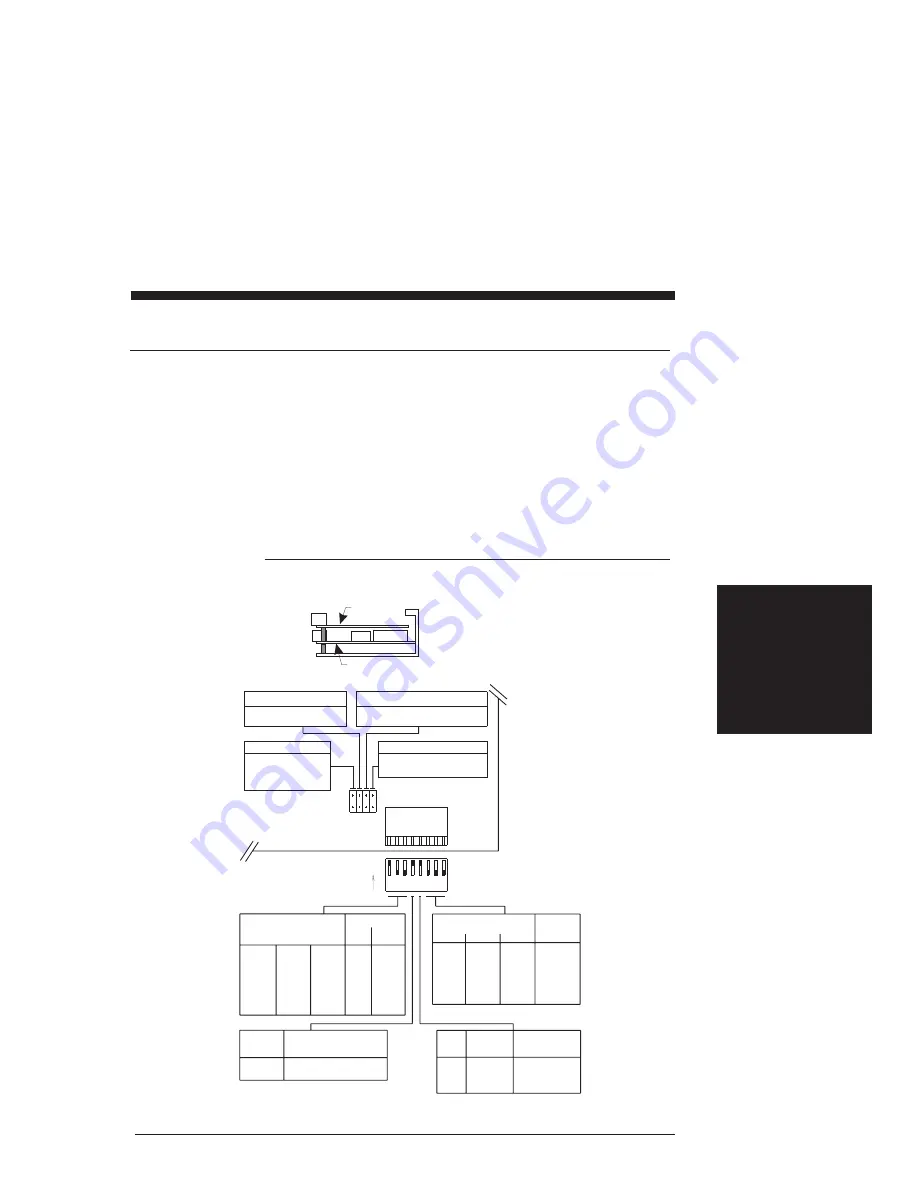
3.2 Drive Board Settings - Switch S1 & Jumper J6
Introduction
DIP switch S1 and Jumper J6 on the drive board set the following:
•
Step size
•
Motor current level
•
Digital electronic damping ON/OFF
•
Idle current reduction
•
Enable sense
•
Step filter response time
Location of S1
6415 Installation and Hardware Reference Manual - Rev E
3 - 15
Powering
Up
OPEN
SWI
POSITION 4
CLOSED
OPEN
DIGITAL ELECTRONIC DAMPING
DISABLED
ENABLED
SW1 POSITION
1
2
3
STEP SIZE
CLOSED
CLOSED
CLOSED
CLOSED
OPEN
OPEN
OPEN
OPEN
CLOSED
CLOSED
OPEN
OPEN
CLOSED
CLOSED
OPEN
OPEN
CLOSED
OPEN
CLOSED
OPEN
CLOSED
OPEN
CLOSED
OPEN
DEC
JMPR
IN
DEC
JMPR
OUT
FULL
HALF
1/5
1/10
1/25
1/50
1/125
1/250
HALF
1/4
1/8
1/16
1/32
1/64
1/128
1/256
IN: OPTO ON TO ENABLE
OUT: OPTO OFF TO ENABLE
ENABLE SENSE JUMPER
IDLE T JUMPER
SELECT IDLE CURRENT
REDUCTION TIME
SEE TABLE BELOW
DEC JUMPER (SEE SW1 TABLE BELOW)
IN: SELECT DECIMAL STEP SIZES
OUT: SELECT BINARY STEP SIZES
STEP BW JUMPER
REMOVED AT FACTORY
JUMPERS 3-4, & 7-8
INSTALLED AT FACTORY
OPEN
IDLE-T
JUMPER
SW1
POSITION 5
IDLE CURRENT
REDUCTION
IN
IN
OUT
OUT
CLOSED
OPEN
CLOSED
OPEN
DISABLED
0.1 SEC DELAY
0.05 SEC DELAY
1.0 SEC DELAY
PC CARD EDGE
S1
J6
8
2
MOTOR
CURRENT
AMPS RMS
SW1 POSITION
6
7
8
CLOSED
CLOSED
CLOSED
CLOSED
OPEN
OPEN
OPEN
OPEN
CLOSED
CLOSED
OPEN
OPEN
CLOSED
CLOSED
OPEN
OPEN
CLOSED
OPEN
CLOSED
OPEN
CLOSED
OPEN
CLOSED
OPEN
5.0
4.375
3.750
3.125
2.5
1.875
1.25
0.625
1 2 3 4 5 6 7 8
S1 SIDE VIEW
FACTORY DEFAULT POSITIONS SHOWN
FACTORY DEFAULTS:
5.0 AMPS RMS
STEPSIZE 1/25
IDLE CURRENT REDUCTION
ENABLED (0.1 SEC)
DIGITAL ELECTRONIC
DAMPING CONTROL ENABLED
DRIVER ENABLED UNLESS
ENABLE OPTO DRIVEN
SW1
JMPR
Side View 6415
Drive Board
Oscillator Board