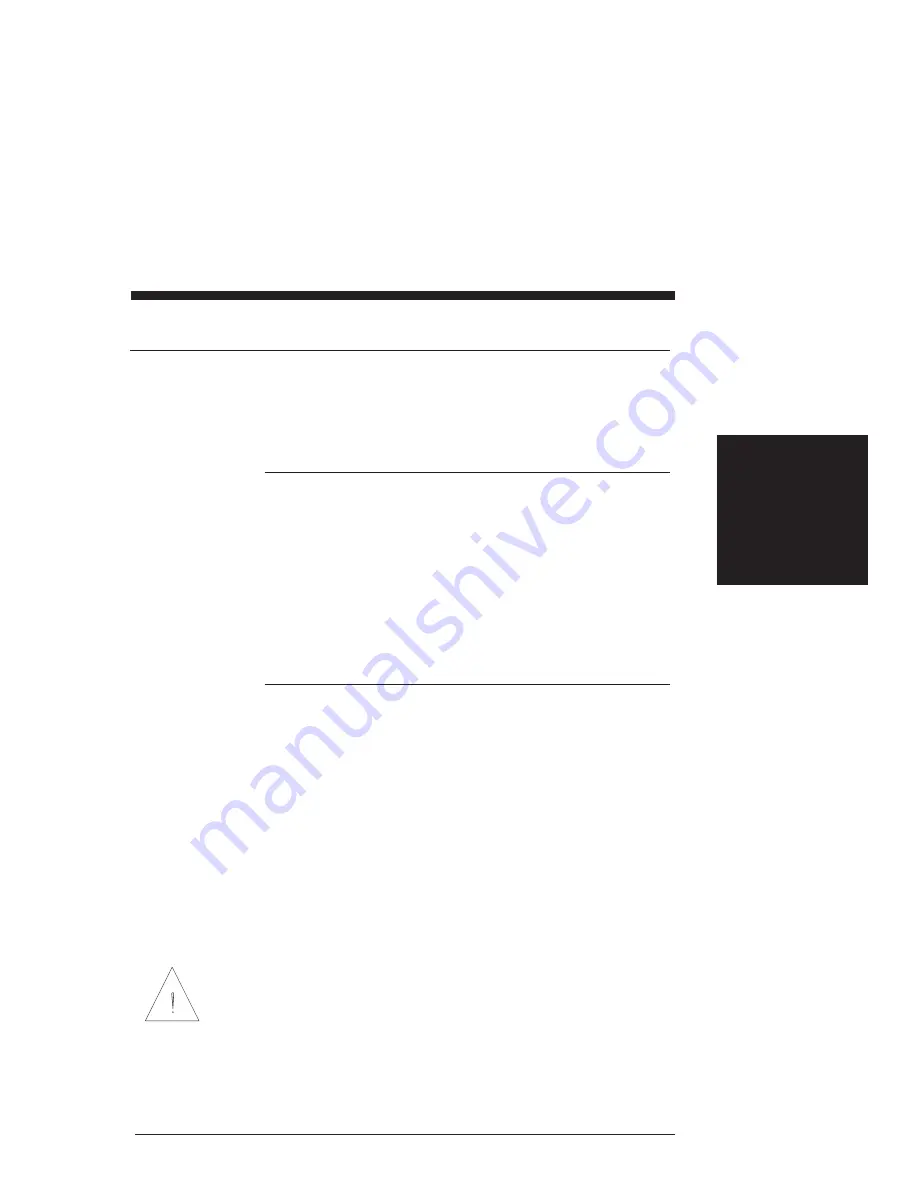
2.3 Selecting Other System Components
Selecting external
analog input and
logic input
power supplies
The 6415 drive requires an ex5Vdc (±0.25) logic power
supply for all user’s control inputs and 0 to +10Vdc (±0.10)
analog input power supply if the analog speed command is derived
from external input source configuration.
Selecting a
motor
The 6415 is designed for use with Pacific Scientific’s line of
hybrid stepper motors or most other 2 phase stepper motors. The
drive works with either the standard line or the enhanced high
performance line of stepper motors. The motor winding current
rating must be compatible with the output current of the drive
package.
Refer to the Torque/Speed Curves in the Pacific Scientific
Motion
Control Solutions Catalog
or contact your local Pacific Scientific
distributor for sizing and motor compatibility assistance.
Selecting bus
power supply
A single power supply is required to operate the 6415 unit.
Note:
In multi-axis applications, it is preferable to run each
power connection from supply to drive and not daisy-chain the
power connections.
The power supply can vary from +24 to 75 Volts maximum at a
maximum current of 5 amps. It does not have to be a regulated
supply.
Note:
The supply voltage cannot exceed 75 volts. The bus
overvoltage circuit is designed to protect the drive from minor
transients. Voltages in excess of 100 Vdc will damage the drive
and void the warranty.
IMPORTANT NOTE
Important information about the power supply is outlined in
Section 2.5.2 and Appendix C. Read these sections carefully
before applying power to the drive.
6415 Installation and Hardware Reference Manual - Rev E
2 - 3
Installation