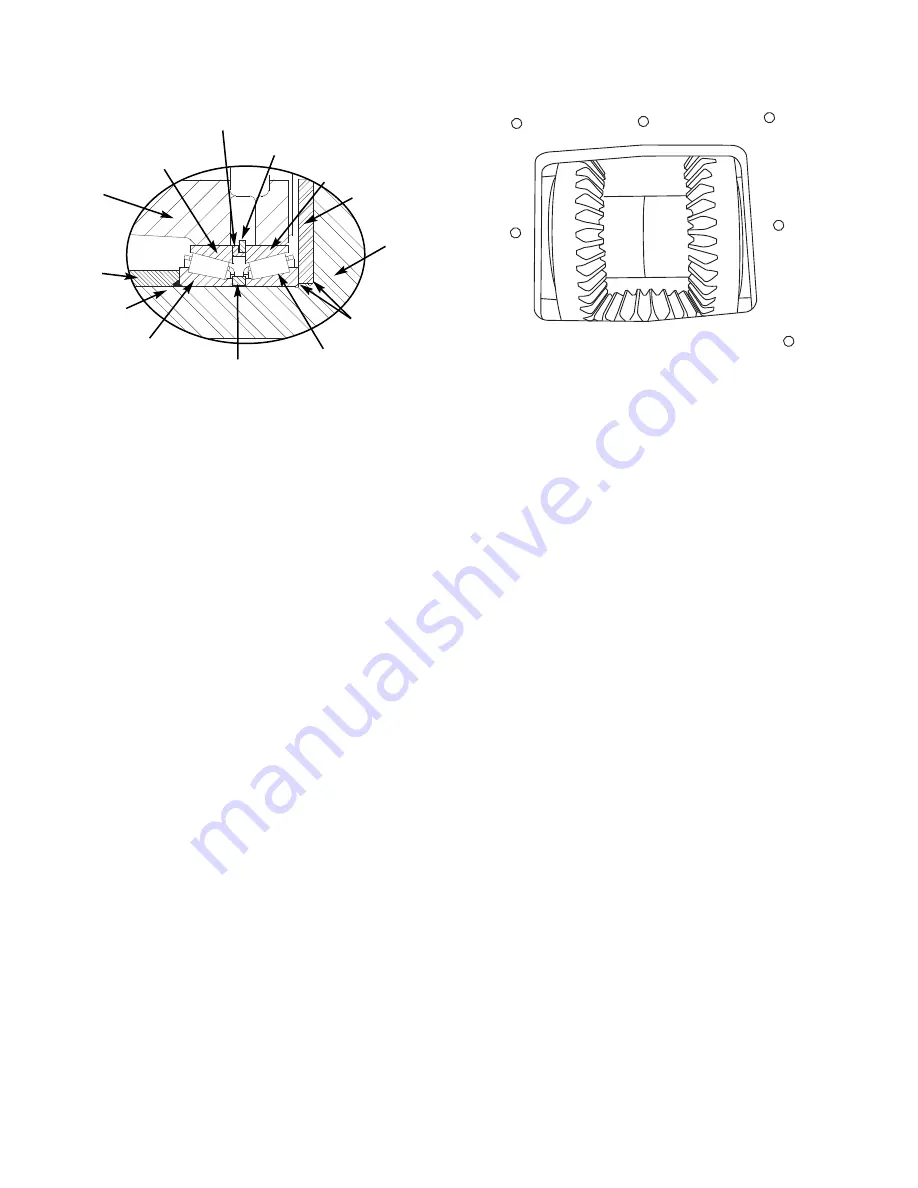
the bevel pinion and seat securely against the pump drive
pinion. Install bearing cone set spacer on to the bevel pin-
ion.
Install the bearing cup retaining ring into the groove in the
carrier bore.
Place the carrier assembly onto bench with the pump side
facing up. Install one bearing cup of bearing set (1) and
seat against the retaining ring.
Turn the carrier over so that the pump side faces down.
Install the bearing cup spacer with the shoulder inside of
the retaining ring. Install the remaining bearing cup and
seat firmly against the bearing cup spacer and retaining
ring.
Place the carrier over the bevel pinion so that the pump
side bearing cup seats on the bearing cone.
Press the remaining bearing cone securely onto the bevel
pinion, seating into the bearing cup.
Lubricate and install O-Ring (5) onto the bevel pinion
against the bearing cone. Install seal spacer (9) over the
bevel pinion with internal tapered edge toward the bear-
ing cone and O-Ring.
Install the oil seal retaining ring (7) into the carrier bore
groove. Apply non-hardening sealant to the outside sur-
face of the oil seal (8) and install the oil seal firmly against
the retaining ring (7).
Install the bearing lockwasher (4) and locknut (2) onto the
bevel pinion. Tighten the locknut to 150 lb•ft (203 N•m)
torque and bend tang of lockwasher (4) into slot of lock-
nut.
Spacer, Bearing Cup
Retaining Ring
Bearing Cup
Bearing Cup
Carrier
Seal Sleeve
O-Ring
Bearing Cone
Bearing Cone
Set Spacer, Bearing Cone
Pinion, Pump Drive
Bevel Pinion
Apply LocTite
601 Here
BEVEL PINION CARRIER INSTALLATION
Apply gear tooth marking compound to bevel pinion and
install carrier assembly into winch case using the original
shim set. Replace gasket as required. Tighten capscrews
to 75 lb•ft (102 N•m) torque.
Rotate bevel pinion in same direction as PTO shaft rota-
tion and check bevel pinion/gear tooth contact pattern.
See typical contact patterns, next page.
Remove carrier assembly to add or remove shims to
obtain the correct tooth contact pattern illustrated below.
Refer to Clutch Shaft Service for bevel gear backlash
adjustment procedure.
Upon final installation of carrier assembly, apply non-
hardening thread sealant to capscrews and tighten to 75
lb•ft (102 N•m) torque.
Refill winch to proper level with recommended lubricant.
30
Summary of Contents for CARCO 50B
Page 2: ......
Page 13: ...WIRING HARNESS 70A for D6R Series II 11...