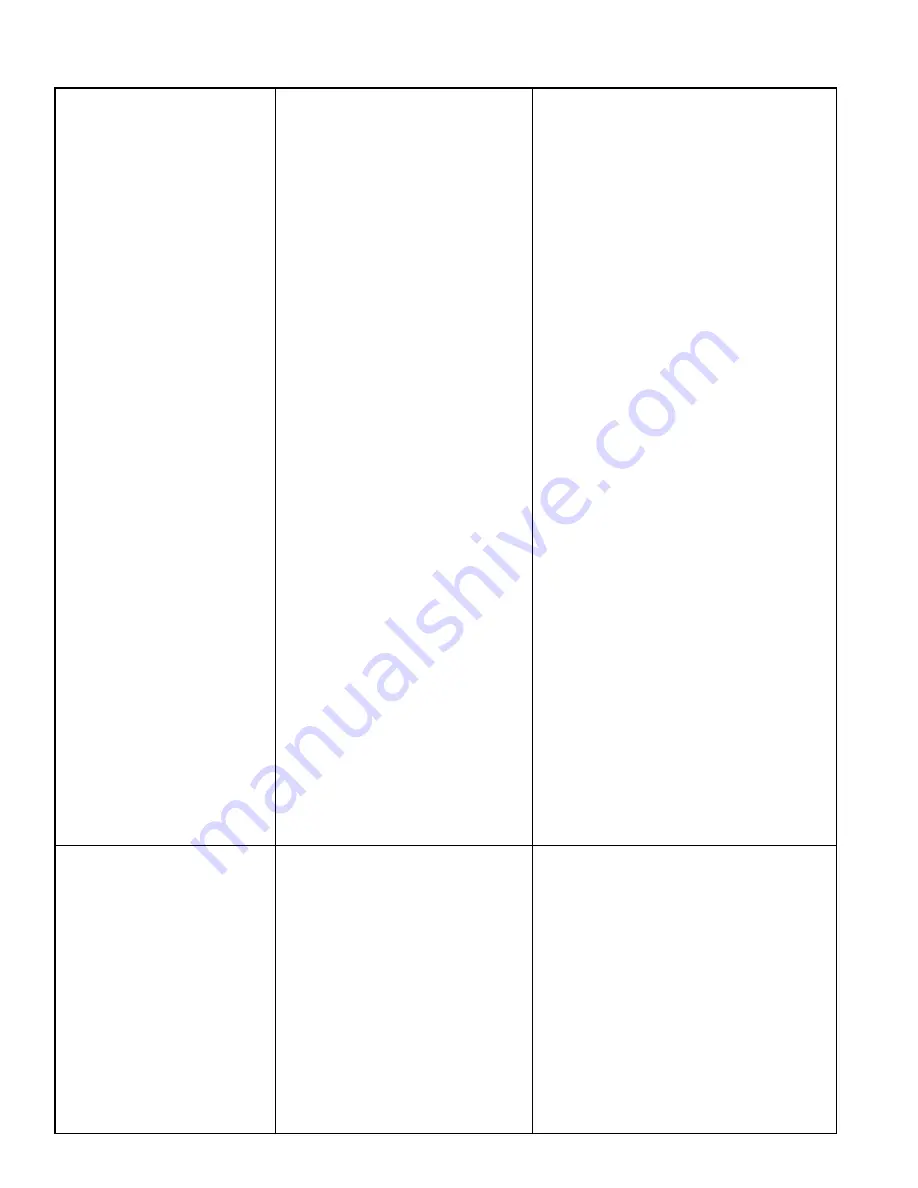
22
D
(continued)
4. Main pressure solenoid valve
(item 10) stuck in the "unload" posi-
tion, or the signal to "charge" is not
present.
5. Suction hose damaged causing
pump cavitation.
6. Pump defective.
7. Loose pressure filter.
4a. Pressure switch (item 6) in the control
valve may be stuck in the "open" position
allowing all oil to flow continuously into the
lubrication circuit.
Disconnect the red and blue wires from the
pressure switch and check for resistance
across the terminals. The switch should be
closed with the pressure drained from the
circuit. If the switch is stuck open, the pres-
sure will decay to 0 PSI. Inspect and
replace as required.
4b. The main pressure solenoid (item 10)
in the control valve may not be energizing,
or may be mechanically stuck by contami-
nation. Use a volt meter to check for 24
Volts DC at the blue wire on the solenoid. If
no voltage present, check the pressure
switch. (Refer to corrective action F2b) If
voltage is present, the solenoid may be
stuck and need to be replaced. The coil
may be tested with an Ohm-meter across
the terminals. A reading of no more than 25
Ohms at 70°F (21°C) is required. The
resistance should decrease with increased
temperature.
5. Drain oil, remove small side inspection
covers to permit access to the pump suc-
tion hose. Inspect and repair / replace as
required. Be sure hose clamps are proper-
ly tightened.
6. Check pump flow as described in the
"Hydraulic Pump" service section of this
manual. If defective, identify the cause for
the pump failure and take corrective action
prior to new pump installation.
7. Tighten or replace filter as required.
E
Clutch damaged or defective
1. Friction discs worn and steel
discs warped.
2. Clutch piston return springs weak
or broken.
3. Clutch piston seized or O-rings
defective. Clutch housing check ball
held off its seat by contamination.
4. Clutch assembled with excessive
clutch piston travel.
1. Replace clutch discs and plates. Adjust
system relief pressure to 390-410 PSI
(2690-2830 kPa) at low idle.
2. Replace springs as required. Always
replace springs in complete sets.
3. Clean and replace components as
required.
4. Rebuild clutch as outlined in the "Clutch
Assembly" section of this manual.
TROUBLE
PROBABLE CAUSE
CORRECTIVE ACTION
Summary of Contents for CARCO 50B
Page 2: ......
Page 13: ...WIRING HARNESS 70A for D6R Series II 11...