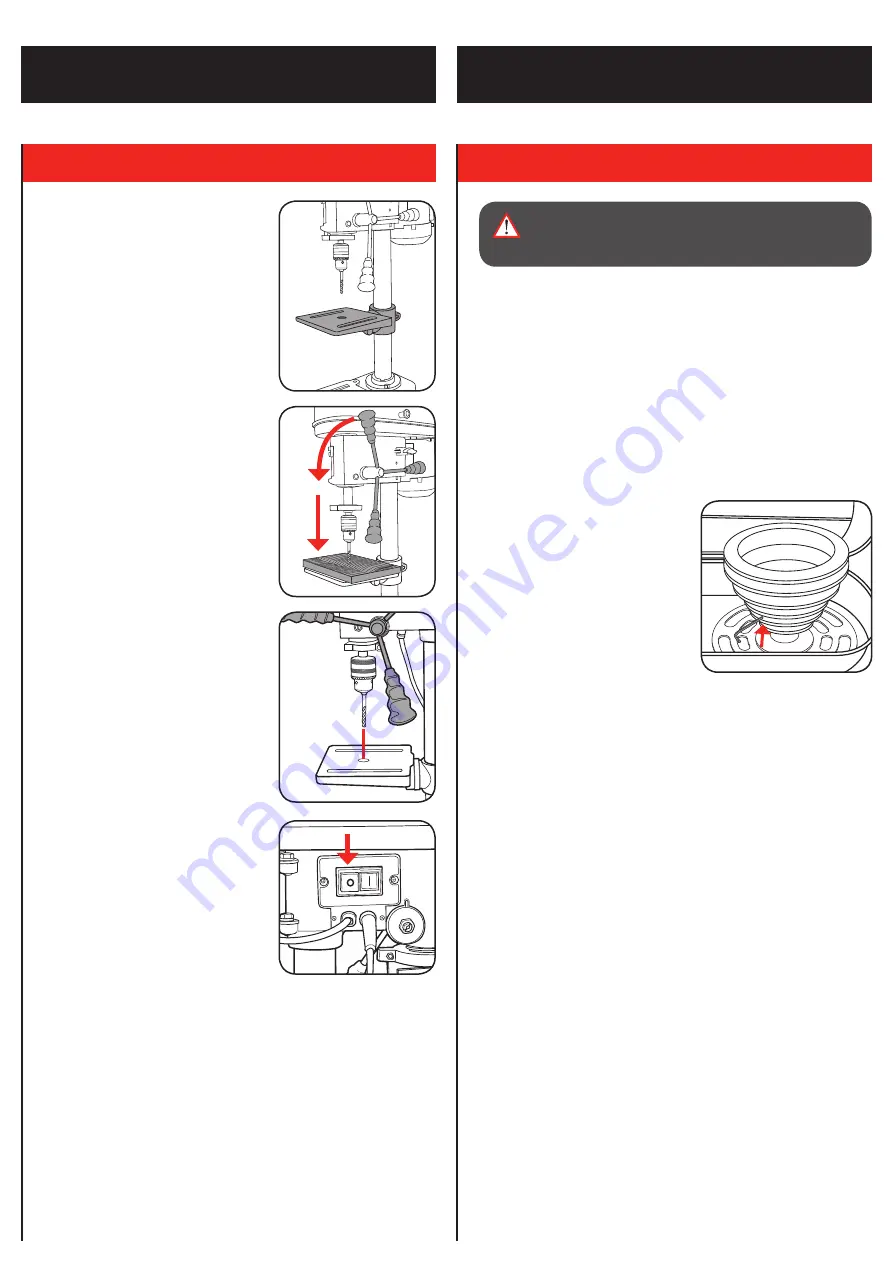
MAINTENANCE
OPERATION (cont.)
5. GENERAL MAINTENANCE
1. Ball bearings are packed with grease at the factory. No further
lubrication of bearings is required.
2. Lubricate all moving parts periodically. Wipe the column, table and
base with an oily cloth to minimise corrosion.
3. Keep air vents clean of dust and dirt.
4. Remove dust and dirt from the drill press regularly with a soft cloth,
brush or compressed air.
5. If the power cord is damaged, have it replaced by an electrician or a
power tool repairer.
6. Regularly check that all bolts, screws and nuts are securely fixed as
these could work loose during normal operation.
7. If the drive belt will not align with
the pulleys. The pulleys may be
worn and need to be replaced. To
remove the pulleys, use the 3mm
allen key provided. Loosen in an
anti-clockwise direction.
Note:
Ozito Industries will not be
responsible for any damage or injuries
caused by the repair of the drill press
by an unauthorised person or by
mishandling of the drill press.
WARNING!
ENSURE THE DRILL PRESS IS
DISCONNECTED FROM THE POWER SUPPLY
BEFORE PERFORMING ANY MAINTENANCE.
5. Adjust the table to your desired
position.
6. Slowly rotate the feed wheel
handles to bring the drill bit down
towards the table and into your
workpiece. After drilling a hole,
release the feed wheel handles
slowly to return the 13mm keyed
chuck to its original position.
Note:
Ensure the hole in the centre
of the table is aligned with the drill bit.
If not aligned, use the 4mm Hex key
provided to loosen the head assembly
on the column support and re-align the
head assembly. Re-tighten the 2 head
lock screws.
7. Continue the operation until the
task is completed. When completed,
switch the drill press off by pressing
the red (O) button on the switch.
0
10
20
30
40
50
0
10
20
30
40
50
0
10
20
30
40
50
0
10
20
30
40
50
0
10
20
30
40
50
0
10
20
30
40
50
0
10
20
30
40
50
0
10
20
30
40
50
0
10
20
30
40
50
0
10
20
30
40
50