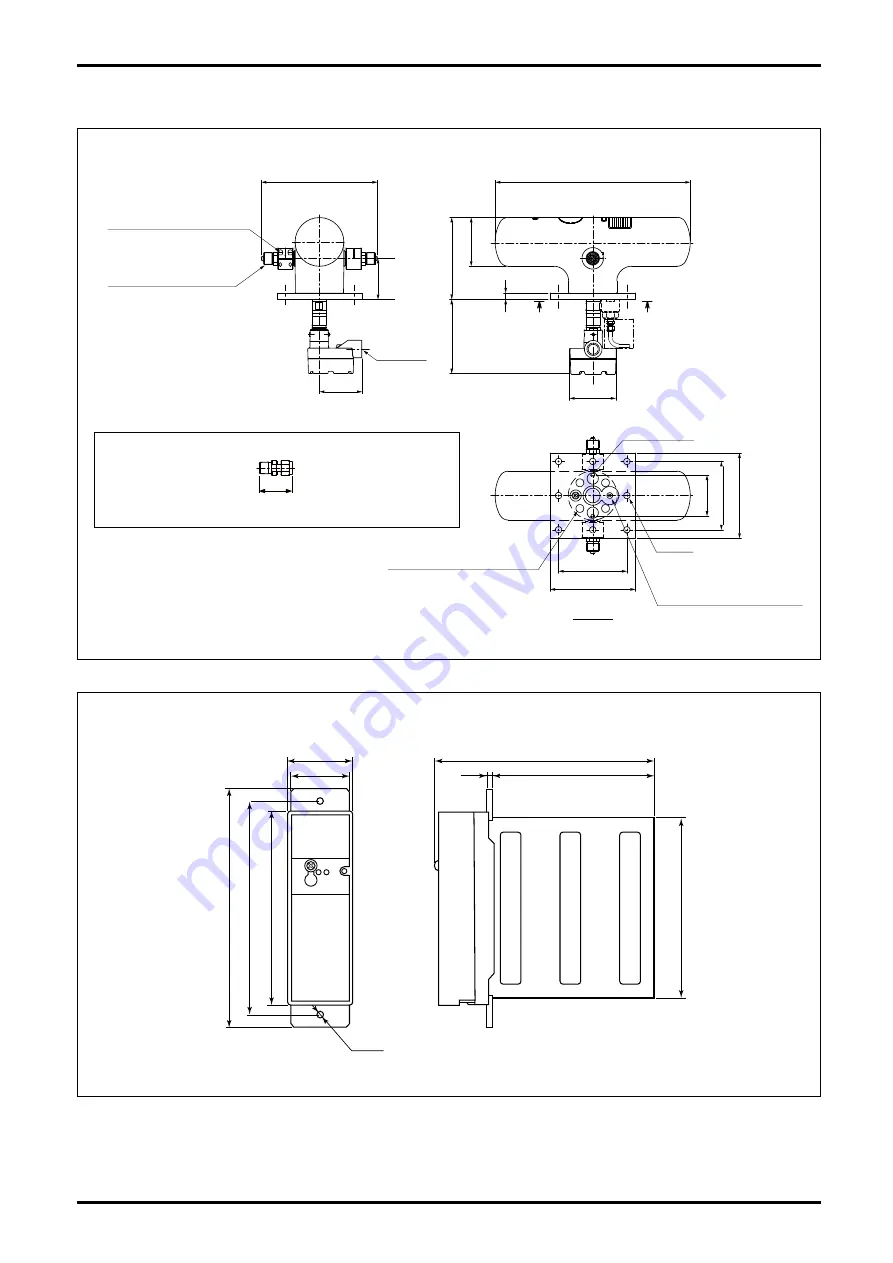
L-770HP--E
4. PART NAMES AND OUTLINE DIMENSIONS
Fig. .
2-Rc1/4 Inert Gas Filler Opening
Normally sealed with Rc1/4 plug
Rupture disk, pressure switch, etc.
may be connected here.
The sections indicated by dashed-dotted line are to be implemented by the user
(With rupture disk for implementing option)
Recommended joint: Swagelok tube joint
Model: SS-810-1-4RT (External thread: 1/4B, External diameter of tube: 1/2B)
43.4
The sections indicated by dashed-dotted line are to be implemented by the user
(Figure shows rupture disk implementation option)
Recommended joint: Swagelok tube joint
Model: SS-810-1-4RT (Male thread: 1/4B, External diameter of tube: 1/2B)
43.4
View A−A
View A−A
272
457
A
A
115
67
96
4-M6 Hex socket bolt
Tighten M6 bolts of the joint clamp
after fixing the joint connection.
High-press. Cone & Thread
Conn., 9/16 dia. 562C
192
229
φ134
φ1
15
60
15
64
2-M5 Body GND
8-φ14.5
4-M10 Meter fitting bolt (embedded)
4-M10 Meter fitting bolt (embedded)
2-Rc1/4 Inert Gas Filler Opening
Normally sealed with Rc1/4 plug
Rupture disk, pressure switch, etc.
may be connected here.
127
230
200
160
200
160
200
160
96
96
98
272
4-M6 Hex socket bolt
Tighten M6 bolts of the joint clamp
after fixing the joint connection.
High-press. Cone & Thread
Conn., 9/16 dia. 562C
Conduit
Connection
G3/4
A
A
457
192
174
φ1
15
15
φ107
2-M5 Body GND
8-φ14.5
200
160
96
●
Sensor
Unit:mm
Fig. .
●
Transmitter
Min.50
2-φ7 /1 台
ラック
ラック
144
160
±0.5
48
44
178
160
145.2
φ4.5
135
165
121.2
3.8
Unit:mm