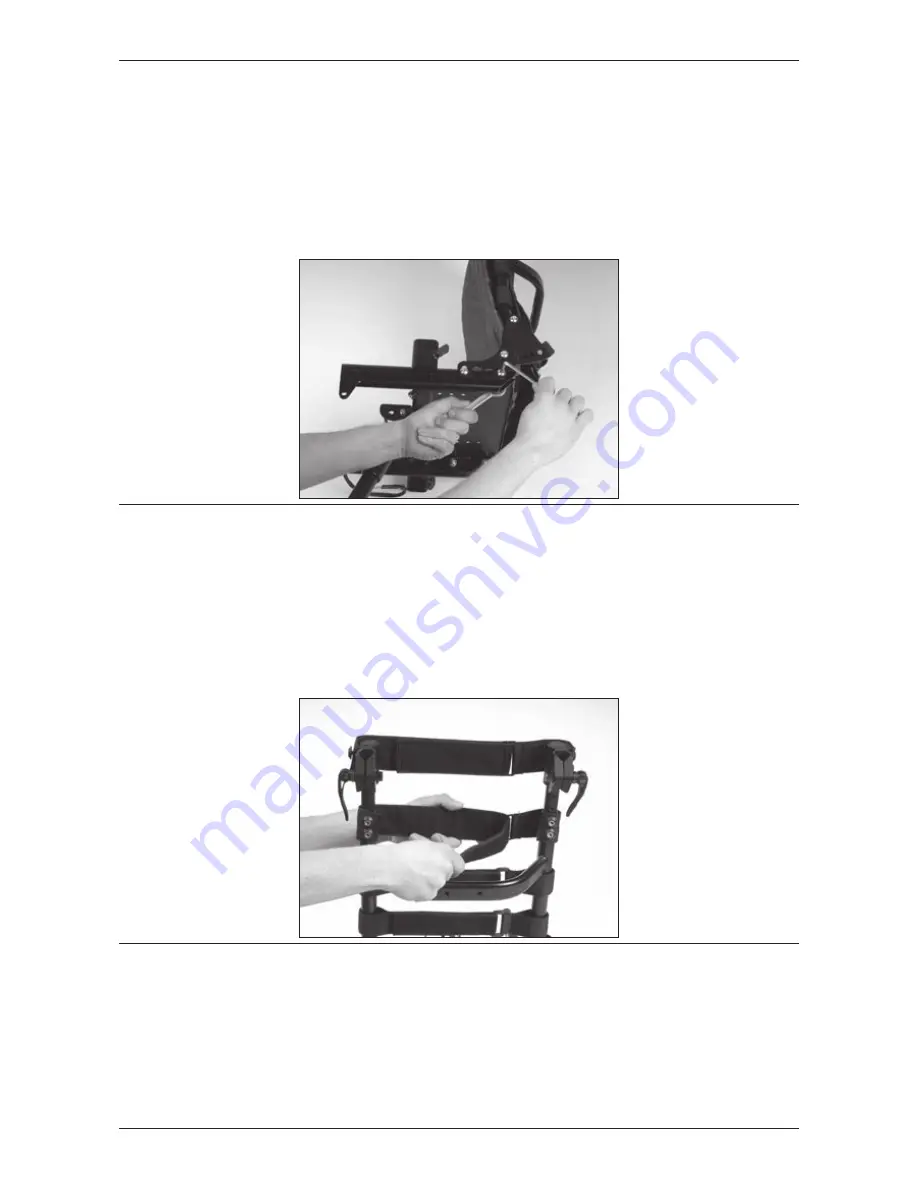
Service Work
Skippi
Ottobock | 27
6.7 Back
The back of the Skippi is attached to the seat frame with two bearing plates on the left and
right. Each of the two bearing plates is attached to the seat frame with two screws and to the
back with one screw. For loosening these three screws, use a size 5 Allen wrench and a size
13 open-end wrench. Loosen the two screws on the seat frame on the left and right to remove
the back. The fourth screw on the bearing plate serves as stop for the back angle adjustment.
Fig. 16 Loosening the bearing plate
Back upholstery
For replacing the back upholstery of the Skippi, simply pull it off the hook-and-loop straps and
reattach the new upholstery to the straps.
For readjusting the back upholstery, remove the upholstery and readjust the hook and loop
straps on the frame.
Fig. 17 Adjusting the back upholstery
Summary of Contents for SKIPPI
Page 1: ...Skippi Service Manual ...
Page 2: ......
Page 69: ...Skippi Ottobock 69 ...
Page 70: ...Skippi 70 Ottobock ...