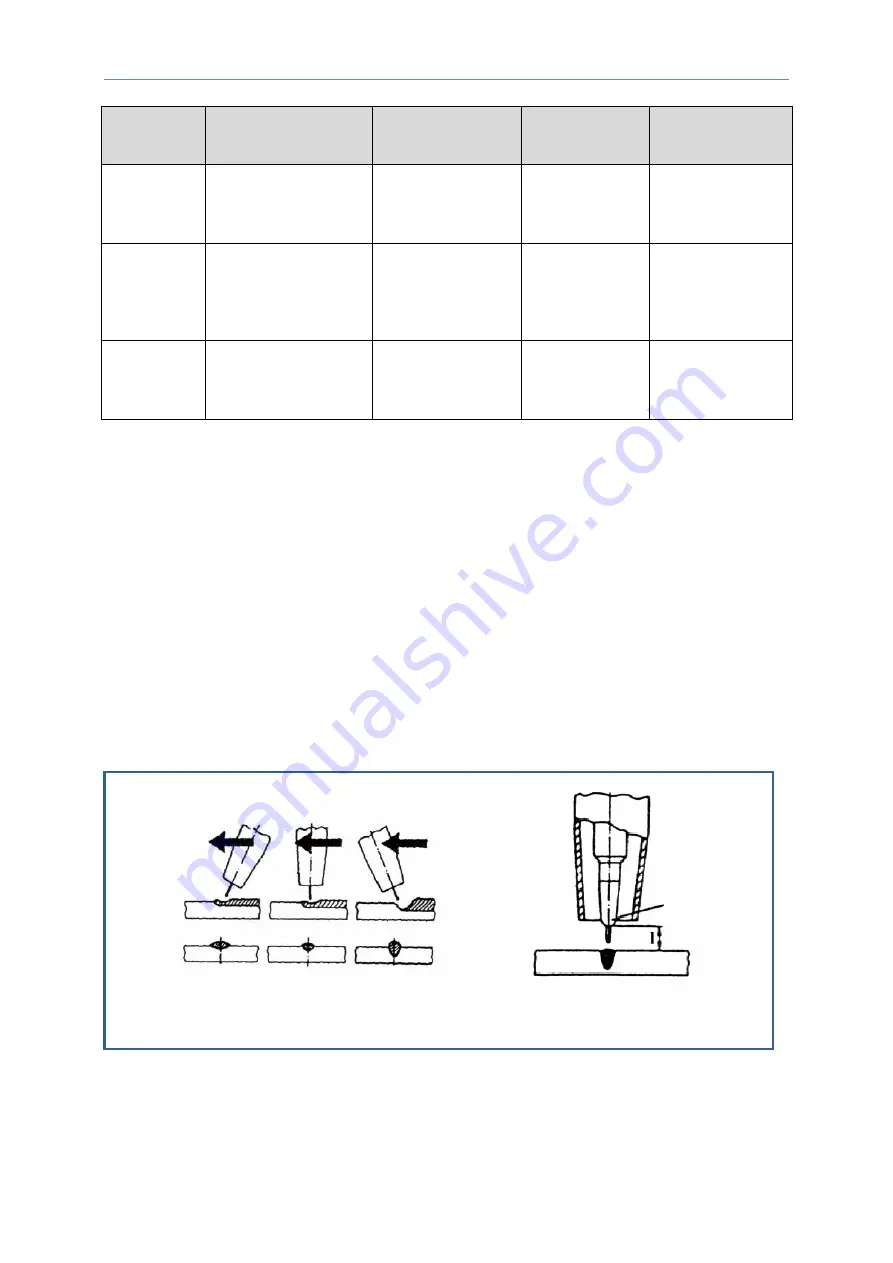
Welding
GB
64
CPTX 400-2/400-2w/450-2w Synergy
Type of the
groove
Diamter of the wire
(mm)
1
Drive gear
(Code)
2
Cog gear
(Code)
3
Feed roll
(Code)
Semicircular
groove
1,2
1,6
2,0
2,4
0430-04-0008
0432-04-0001
0430-04-0008
0430-04-0009
0432-04-0001
0430-04-0009
0430-04-0010
0432-04-0001
0430-04-0010
0430-04-0011
0432-04-0001
0430-04-0011
Trapeze
groove
0,8
1,0
1,2
1,6
0433-04-0001
0432-04-0001
0430-04-0012
0433-04-0002
0432-04-0001
0430-04-0012
0433-04-0003
0432-04-0001
0430-04-0012
0433-04-0004
0432-04-0001
0430-04-0012
Ribbed
groove
1,2
1,6
2,0
2,4
0430-04-0013
0432-04-0001
0430-04-0013
0430-04-0014
0432-04-0001
0430-04-0014
0430-04-0015
0432-04-0001
0430-04-0015
0430-04-0016
0432-04-0001
0430-04-0016
8. Welding
Set up the device in the workplace. Pay attention primarily to the fact that the air can
circulate well and the cooling is ensured. Clip the ground wire with the clamp on the clean,
non-oxidized work part. Congenial to the material and the thickness of the work piece, the
corresponding wire diameter has to be selected. After turning the switch the welding machine
is on and welding supply. With the potentiometer you can select the needed wire speed.
Note that the handling of the torch greatly affected the welding quality (see following figure).
The distance between the wire and the work piece must be kept constant, whereat the
recommended distance for steel plates is about 5-10 mm.
Pressing the torch switch the unit starts to weld. The torch is handled by one of the three
methods shown above.
Push
Position
Neutral
Position
Pull
Position
Contact
tip