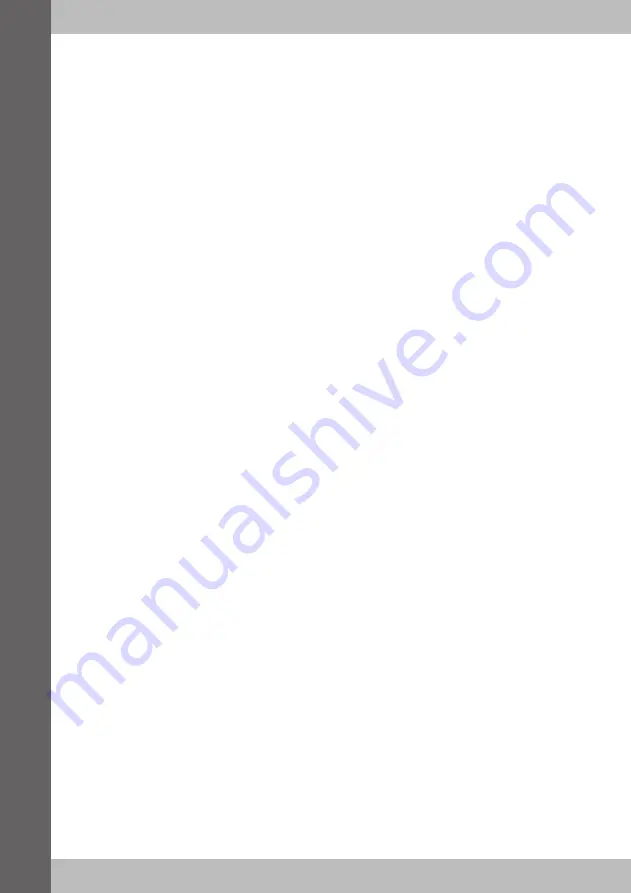
English
2
Basic operation
Flow measurement
The unit measures flow using an axial turbine mounted in the aluminum base block. The oil flow
rotates the turbine and its speed is proportional to the oil velocity. The revolutions of the turbine
are measured by means of a magnetic sensing head which feeds a pulse every time a turbine
blade goes by to an electronic circuit. The electronic circuit has a built-in micro processor; the
signal is amplified and linearised to maximise accuracy.
Pressure gauge
The pressure gauge has a spiral Bourdon tube and the gauge case is filled with glycerine to
ensure good dampening on pulsating pressures. The gauge is connected to the turbine block
by a fine bore capillary tube. The unit gauge has a shuttle valve which automatically reads
the highest pressure in both directions of flow. A gauge port is provided on the block for the
addition of a low pressure gauge.
Temperature
The thermistor temperature transducer is in contact with the oil flow and readout is on the
meter scale calibrated 32 - 250°F or 0 - 120°C.
Bi-Directional Loading Valve
The reverse flow valve gives positive shut-off and pressure control in both directions of flow.
The loading valve has two easily replaceable burst discs located in the valve assembly which
internally protect the unit and machine in both flow directions.
Installation guidance
l
All hydraulic connections should be made by suitably qualified personnel.
l
Avoid sharp bends because high pressure hoses will deflect and straighten under pressure.
l
A preliminary check of the hydraulic system’s oil supply, pump rotation, filters, oil lines,
cylinder rods as well as looking for external leaks should be made prior to installing the unit.
l
Although the unit can be used in both flow directions, the preferred direction is indicated by
the larger arrow on the panel. When used for reverse flow tests, slightly lower accuracies
may be obtained depending on the oil viscosity, density and compressibility.
l
The unit should be connected to the hydraulic circuit by means of flexible hoses 3 - 6 ft
(1 - 2 metres) metres long.
l
The use of quick-disconnect couplings can save time. Make sure the hoses are long enough
so that the unit can be used safely on the machine.
l
The hoses and fittings at the inlet must be of adequate size for the flow being tested.
Elbows, rotary couplings etc., at the inlet and outlet ports should be avoided to ensure
accurate readings.
l
The use of the flexible hoses will help to isolate the unit from vibration which often exists.
l
The internal burst discs are to protect the unit not the hydraulic installation. Always ensure
the appropriate relief devices are fitted to protect the installation.