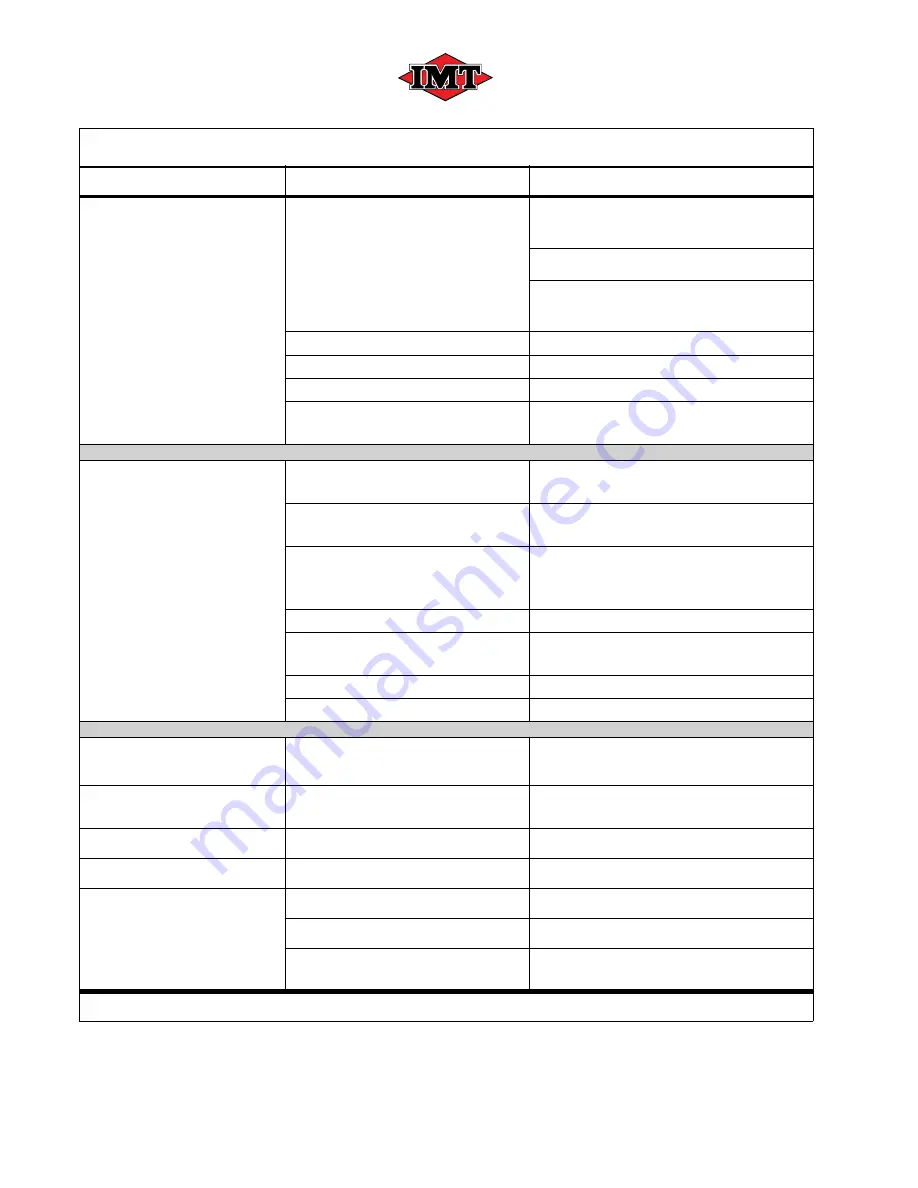
CAS80R
SECTION 6: TROUBLESHOOTING
PAGE - 30
Manual # 99905932 (February 2016)
®
IOWA MOLD TOOLING CO., INC.
(641) 923-3711 • www.imt.com
6.2 TROUBLESHOOTING GUIDE
MALFUNCTION/FAULT
POSSIBLE CAUSE
CORRECTIVE ACTION
Compressor shuts down
air with demand present
Compressor discharge
temperature switch is open
Cooling air flow is insufficient; clean
cooler and check for proper ventilation.
Low fluid sump level; add fluid.
Fan not operating. Check ground and
fan switch.
Plugged oil filter
Replace oil filter.
Dirty cooler core exterior
Clean cooler core.
Contaminated cooler core
Remove and clean cooler core.
Hydraulic pressure and flow
incorrect
Adjust and reset.
Compressor will not build
up pressure
Air demand is too great
Check service lines for leaks or open
valves. Too much air demand.
Dirty air filter
Check the filter and clean or change
element if required.
Pressure regulator out of
adjustment
DO NOT ATTEMPT TO ADJUST.
Contact the IMT Service Department
for assistance.
Defective pressure regulator
Replace pressure regulator.
Motor does not speed up
Check hydraulic flow and pressure and
adjust if necessary.
Service valve wide open
Close service valve.
Inlet stuck shut
Check oil level
Compressor over pres-
sures
Pressure regulator out of
adjustment
Contact factory service department.
Defective pressure regulator
Replace pressure regulator; Contact
factory service department.
Leak in air control line
Check line and correct.
Inlet valve stuck open
Free or replace valve.
Restriction in control line
Dirt or ice present. Clean or free up.
Defective safety valve
Replace safety valve.
Plugged coalescer (air/oil
separator)
Replace coalescer.
Continued on next page
Summary of Contents for IMT CAS80R
Page 66: ...BLANK PAGE...
Page 67: ...BLANK PAGE...