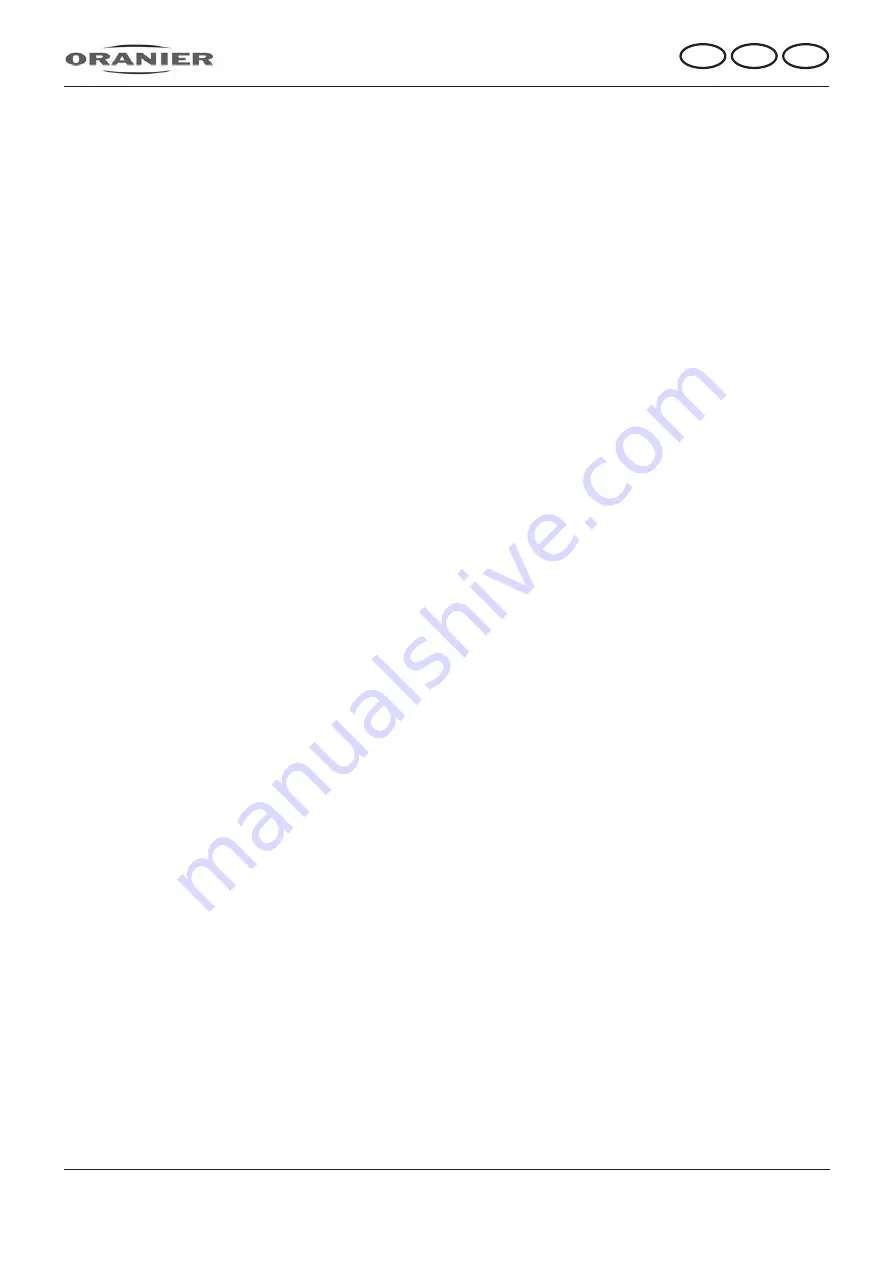
19
D
CH
AT
ORANIER factory guarantee
Proof of purchase is required in every case in order to
access guarantee services.
Regardless of the dealer's obligations arising from the
contract of purchase, we offer consumers a factory
guarantee subject to the following conditions for our
ORANIER appliances:
The ORANIER guarantee extends to the free-of-charge
repair of the appliance or faulty parts. Entitlement to
free replacements applies only to parts that show ma-
terial or workmanship defects.
All direct labour and material costs required to resolve
such defects will be taken care of.
Further claims are excluded.
These guarantee conditions only apply to Germany and
Austria. For all other countries, separate conditions ap-
plyt to the respective country company.
1.
The ORANIER factory guarantee runs for 24 months
and starts from the moment of handover, which must be
documented with an invoice or delivery note.
2.
The factory guarantee covers all functional defects
which are demonstrably attributable to manufacturing
or material problems, despite correct connection, prop-
er use and compliance with the applicable ORANIER
installation instructions and operating instructions.
Such defects will be resolved by our customer service
team. Enamel and paint damage will only be covered
by this guarantee if they appear within 2 weeks of the
handover of the ORANIER appliance to our customer
service team.
Transport damage (this must be claimed from the trans-
porting company in accordance with their terms and
conditions), as well as setup, calibration and adjustment
work on gas consumption installations, are not covered
by this factory guarantee.
3.
Claims against the factory guarantee do not prolong
the guarantee period either for the ORANIER appliance
or any newly installed parts. Swapped parts shall be-
come our property.
4.
Our customer service team will decide on the loca-
tion, nature and scope of the repairs to be carried out
or exchange of an appliance as it deems economically
appropriate.
Unless otherwise agreed, our central customer service
team should be notified. The repair will generally be
carried out at the setup location, or under exceptional
circumstances at our customer service workshop. Ap-
pliances due for repair must be made accessible so that
no damage can occur to furniture, floor coverings, etc.
5.
The spare parts and labour time required for the re-
pair will not be charged.
6.
We accept no liability for damage or defects to appli-
ances and their parts caused by:
- External chemical or physical influences
during transport, storage, setup and use (e.g. damaged
caused by quenching with water, overflowing feed, con
-
densation, overheating). Hairline crack formation on
enamelled or glazed parts does not constitute a quality
defect.
- Incorrect choice of size.
- Failure to comply with our setup and operating instruc-
tions, the applicable general building regulations and
local requirements of the responsible
authorities, gas and electricity supply companies.
This also includes defects to the exhaust gas pipes
(stove pipe, inadequate or excessive chimney draught)
and any incorrectly carried-out repair work, especially
the undertaking of modifications to the appliance, its fit
-
tings and its supply cables or pipelines.
- The use of unsuitable fuels in appliances fired with
coal and heating oil; unsuitable gas characteristics and
gas pressure fluctuations for gas-powered appliances;
unusual voltage fluctuations compared to the nominal
voltage for electricity-powered appliances.
- Incorrect operation and overload, resulting in over-
heating of the appliances, incorrect handling, inade-
quate maintenance, inadequate cleaning of the appli-
ances or their parts; use of unsuitable cleaning agents.
- Wear of the parts made from iron and firebrick ex
-
posed directly to the flames (e.g. cast steel or firebrick
linings).
We are not responsible for direct or indirect damage
caused by the appliances. This includes the build-up of
dirt in the room caused by decomposition products of
organic dust components and their pyrolytic products
which can be deposited as a dark layer on carpets, fur-
niture, textiles and stove elements.
If the resolution of a defect is not covered by our guar-
antee, then the consumer must pay the costs of the en-
gineer's visit and the repair work carried out.
ORANIER Heiztechnik GmbH
Oranier Strasse 1
35708 Haiger / Sechshelden
Summary of Contents for Polar Neo Aqua I
Page 20: ...20 Dimensions ...