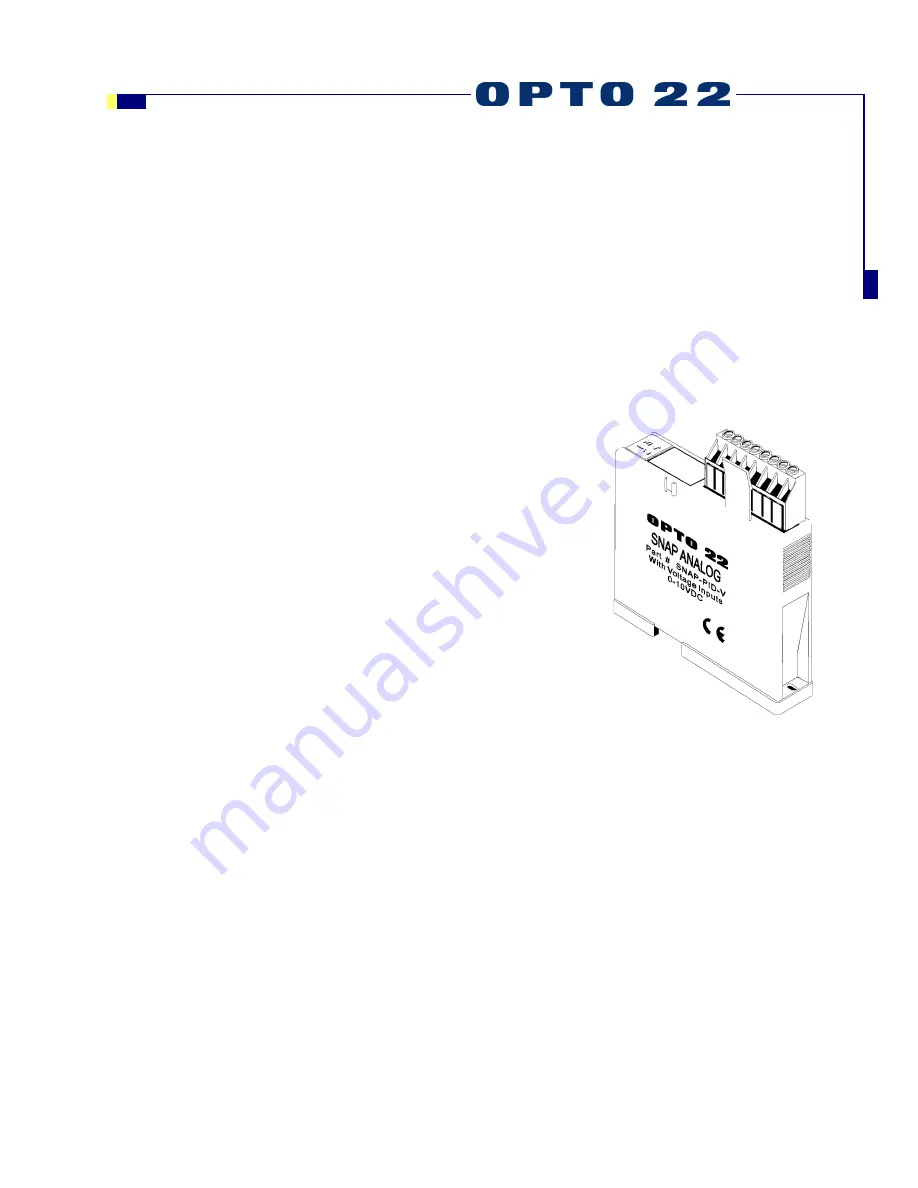
SNAP PID Module User’s Guide
1
Chapter 1
SNAP PID Module User’s Guide
Introduction
The SNAP-PID-V module is designed for users of Opto 22
SNAP Ethernet I/O™ systems with the
SNAP-B3000-ENET, SNAP-ENET-RTC, or
SNAP-WLAN-FH-ADS brain. The SNAP-PID-V monitors
input signals and adjusts output signals to control one
proportional-integral-derivative (PID) loop, performing
all necessary PID calculations in the module itself.
Before the introduction of the SNAP-PID-V module, using
a PID loop with SNAP Ethernet I/O systems required an
Opto 22 industrial controller running an OptoControl™
strategy or a remote computer running SCADA software.
For non-Ethernet I/O units, the multifunction B3000 brain
could be used. The SNAP-PID-V module makes this
equipment unnecessary, since all PID calculations are
made in the module independent of a controller or other
processor.
SNAP-PID-V Applications
Typical applications for the SNAP-PID-V module include temperature, pressure-level, flow, and
process control. The SNAP-PID-V is ideal for remote installations or other environments where
communication links are subject to interruption. Since PID calculations run locally on the I/O
module independent of a controller, brain, or other processor, PID loop control can continue even
if the communication link to the I/O system is broken.
The SNAP PID module is also useful in applications where multiple PID loops must be controlled
at one location. When multiple PID loop calculations run on a single industrial controller or
computer, a performance degradation can occur. When additional SNAP-PID-V modules are
added to a SNAP rack, however, all modules continue to perform PID loop calculations at a
constant speed without system degradation, providing a highly scalable solution. Up to twelve
SNAP-PID-V modules can be used on an Opto 22 16-module B-series mounting rack.
SNAP-PID-V