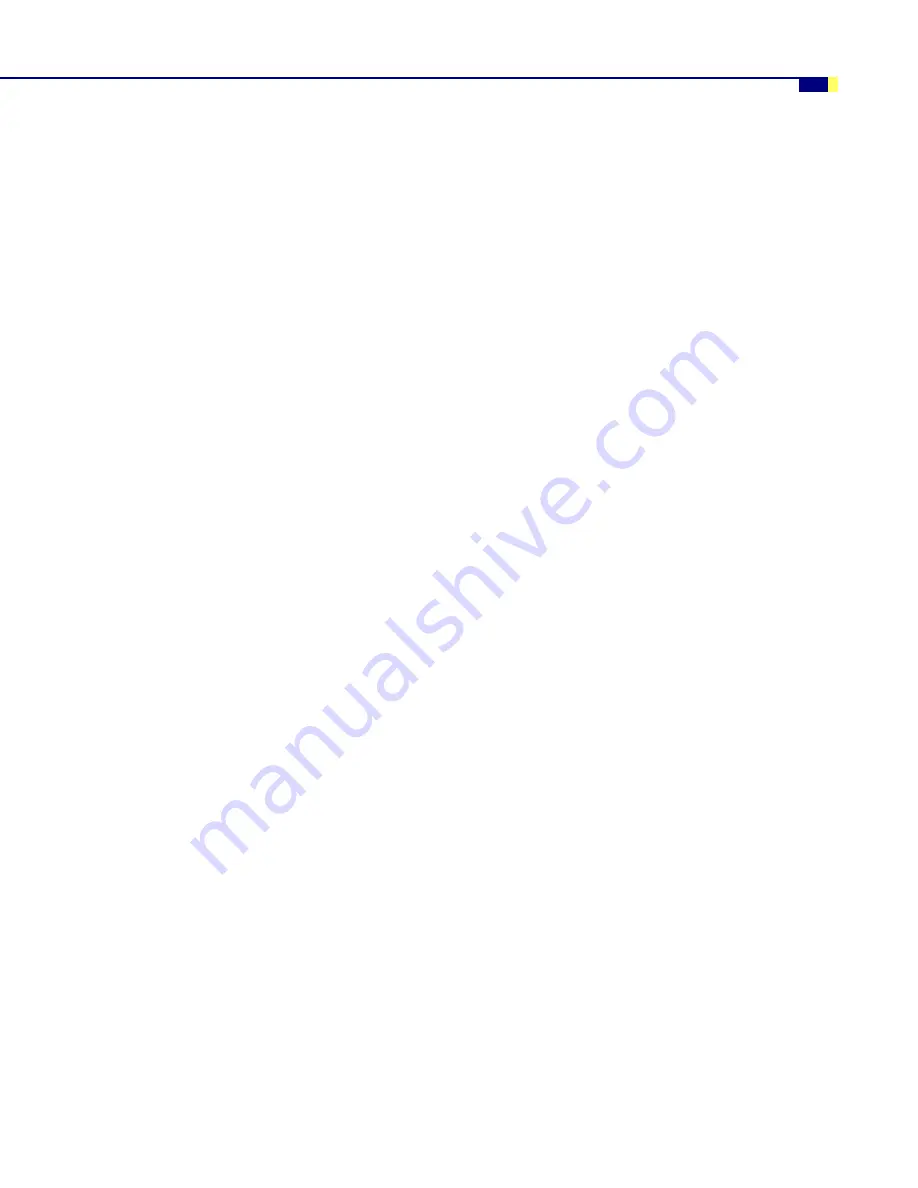
SNAP PID MODULE REFERENCE
SNAP PID Module User’s Guide
17
•
Confirm that the module is plugged firmly into the mounting rack. For applications where
vibration or thermal expansion and contraction may be a consideration, it may be beneficial
to use screws to attach the PID and other SNAP modules to the SNAP mounting rack.
•
If PID information doesn’t appear in the ioManager PID Module screen or when using
OptoENET PID Module Tuner, do the following:
– Check that the correct module location on the mounting rack is selected in ioManager’s
PID Module screen.
– Confirm that signal input and output wiring is correctly connected to the module’s
screw terminal connector. See
“Attach Input and Output Wiring” on page 5
for wiring
information.
SNAP PID Module Reference
PID Velocity Algorithm
The SNAP-PID-V module uses the following PID velocity algorithm:
PID Control Word
The SNAP-PID-V module’s control settings are configured by modifying a single hexadecimal
control word.
When using ioManager software you need to use the control word to configure the
PID module. When using OptoENET PID Module Tuner, it isn’t necessary to enter a control word
since control settings are made using the software’s user interface.
Change in output
= Gain
×
(A + B – C)
where
A = (Error at t
0
) – (Error at t
1
)
B = ((Error at t
0
) / Integral ratio)
C = (Derivative ratio
×
(PV input at t
0
) – (2
×
PV input at t
1
) + (PV input at t
2
))
and
Error = Setpoint – PV
t = Scan time (the time between setpoint and process variable readings)
t
0
= Time when the scan timer reaches zero. This is when PID is calculated.
t
1
= The last time the scan timer reached zero, or (t
0
– t).
t
2
= The second-to-last time the scan timer reached zero, or (t
0
– (2
×
t)).
PV
= Process Variable (the input signal)
Integral ratio
= Integral / Scan time
Derivative ratio
= Derivative / Scan time
Setpoint and process variable readings are taken when the scan timer reaches zero and the PID
calculation is made.