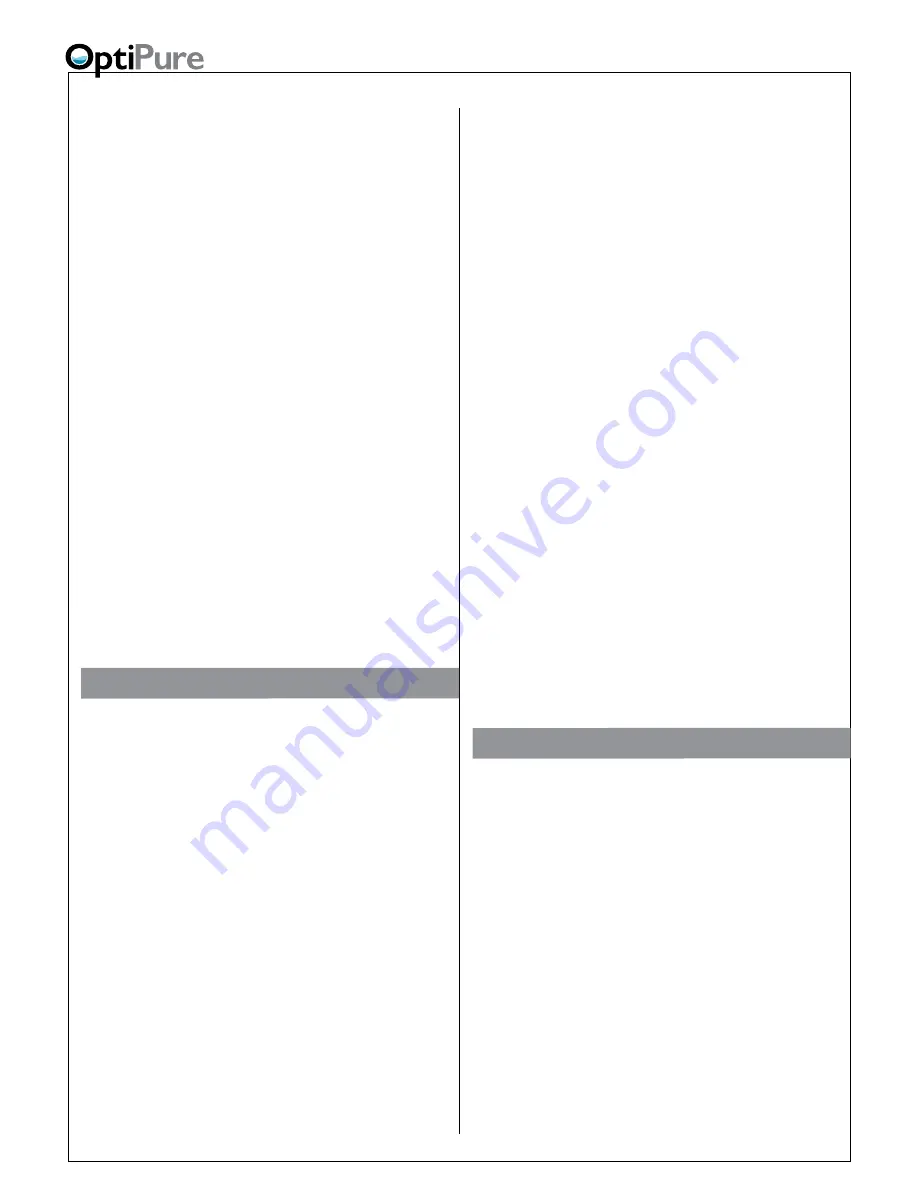
BWS350 System Installation, Operation & Maintenance
10
3. Open downstream valves at the equipment to
allow water to flow and air to purge through the
post-treatment (if used) and from the distribution
lines. When purging distribution lines the pump
may shut off if the water level in the storage tank
drops near the bottom of the tank. (Add more
water to the tank if necessary.) Once distribution
lines are flushed and all air is purged, close the
equipment valves. When there is no demand for
water the buffer tank will fill and the pump will shut
off automatically.
4. Before proceeding to “System Blend Adjustment,”
follow these steps to empty the tank of untreated
feed water:
• Connect a piece of 3/8” blue tubing into the
push-to-connect fitting of the SAMPLE PORT
VALVE on the right side of the processor, and
route the other end of the tubing into a drain or
bucket.
• Open the Sample Port Valve to drain water
from the storage tank. When the pump shuts off
due to a low water level, close the Sample Port
Valve.
5. Replace and tighten the lid onto the storage tank.
System Blend Adjustment
IMPORTANT: The TDS Blend must be properly
adjusted before operating the connected
equipment.
If you do not know the “TARGET TDS”
SET THE BLEND “IN” between 60 and 80.
The
owner/operator should consult with their OptiPure
Dealer or contact the OptiPure factory for assistance in
determining an appropriate TDS Target Range.
An improper TDS Blend setting or failure to
properly maintain the system can cause damage
to equipment.
Factors that can impact the TDS of the
Optimized Water include changes in water pressure
and temperature, seasonal changes in water quality,
and municipal source blending practices. To assure
maintaining your target TDS range year-round we
recommend periodically checking the “IN” TDS and
making adjustments as needed.
Optimized Water TDS - Blending Adjustment
1. Allow the system to operate for at least 5 minutes
before continuing to Step 2.
2. Push the purple “POWER” button on the Water
Quality Monitor located on the upper left corner.
It will immediately display the “IN” or Optimized
Water - TDS (Total Dissolved Solids) in PPM (parts
per million). By adjusting the blend valve you are
able to change the “IN” TDS to the desired Target
Range.
3. Within 30 seconds, push the “OUT” button to
display the Permeate Water TDS (from the RO
membrane).
4. If the “IN” TDS is outside of the desired range:
• Turn the Blending Valve knob counter-clockwise
to open the Blending Valve, increasing the
amount of Filtered Water blending with the
RO water, thereby increasing the TDS of the
Optimized Water.
• Turn the Blending Valve know clockwise to close
the Blending Valve, decreasing the amount
of Filtered Water blending with the RO water,
thereby decreasing the TDS of the Optimized
Water.
5. Once the desired TDS is obtained allow the
system to run for several minutes, periodically
checking the “IN” TDS. Make smaller incremental
adjustments as necessary until the TDS “Target” is
achieved.
Complete the Installation
Transition to Owner/Operator
The FINAL STEP is to meet with the Owner/Operator,
familiarize them with the system and complete the
Post-Installation Check List
.
The system is now in “normal operating” mode and
the storage tank will fill with Optimized Water from
the Processor. Complete the
“Post Installation
Checklist”
to
Confirm Normal Operation and
System Settings
.
Allow the storage tank to fill before beginning
operation of the connected equipment.