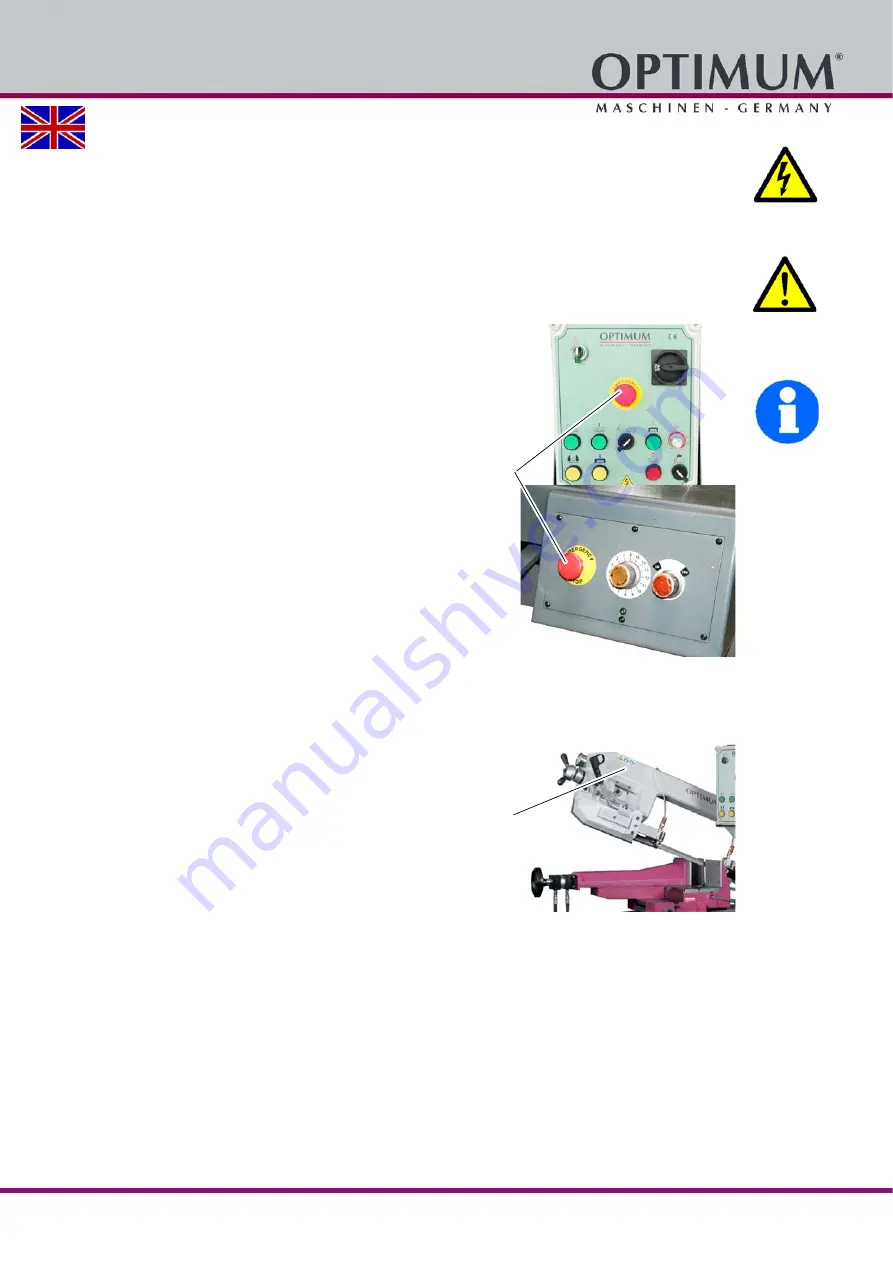
Safety
Version 1.0.3 - 2020-10-13
13
Translation of original instruction
SD351AV
EN
SD351A
V_G
B
_1.
fm
WARNING!
Dangerous voltage even if the main switch is switched off. The areas marked by the
pictogram might contain live parts, even if the main switch is switched off.
1.8.2
Emergency stop switch
CAUTION!
Only press the emergency stop button in a genuine emergency. You should not use the
emergency-stop button to stop the machine during normal operation.
The emergency stop button switches off
the metal band saw.
INFORMATION
Turn the emergency stop button clock-
wise after pressing it to switch on the
metal band saw again.
Img.1-2:
Control panel
1.8.3
Saw bow
The saw bow of the metal band saw is pro-
vided with a protective cover. The
protective cover covers the
belt guide rolls and the revolting saw band.
The metal belt saw only switches on when
the protective cover is being closed.
Img.1-3:
Saw belt housing with protective cover.
Emergency stop
switch
Saw bow
Summary of Contents for 3290360
Page 1: ...EN Operating Instructions Version 1 0 3 Metal band saw Part no 3290360 ...
Page 80: ...Version 1 0 3 2020 10 13 80 Originalbetriebsanleitung SD351AV DE EN SD351AV_wiring diagram fm ...
Page 92: ...Version 1 0 3 2020 10 13 92 Translation of original instruction SD351AV EN SD351AV_GBSIX fm ...