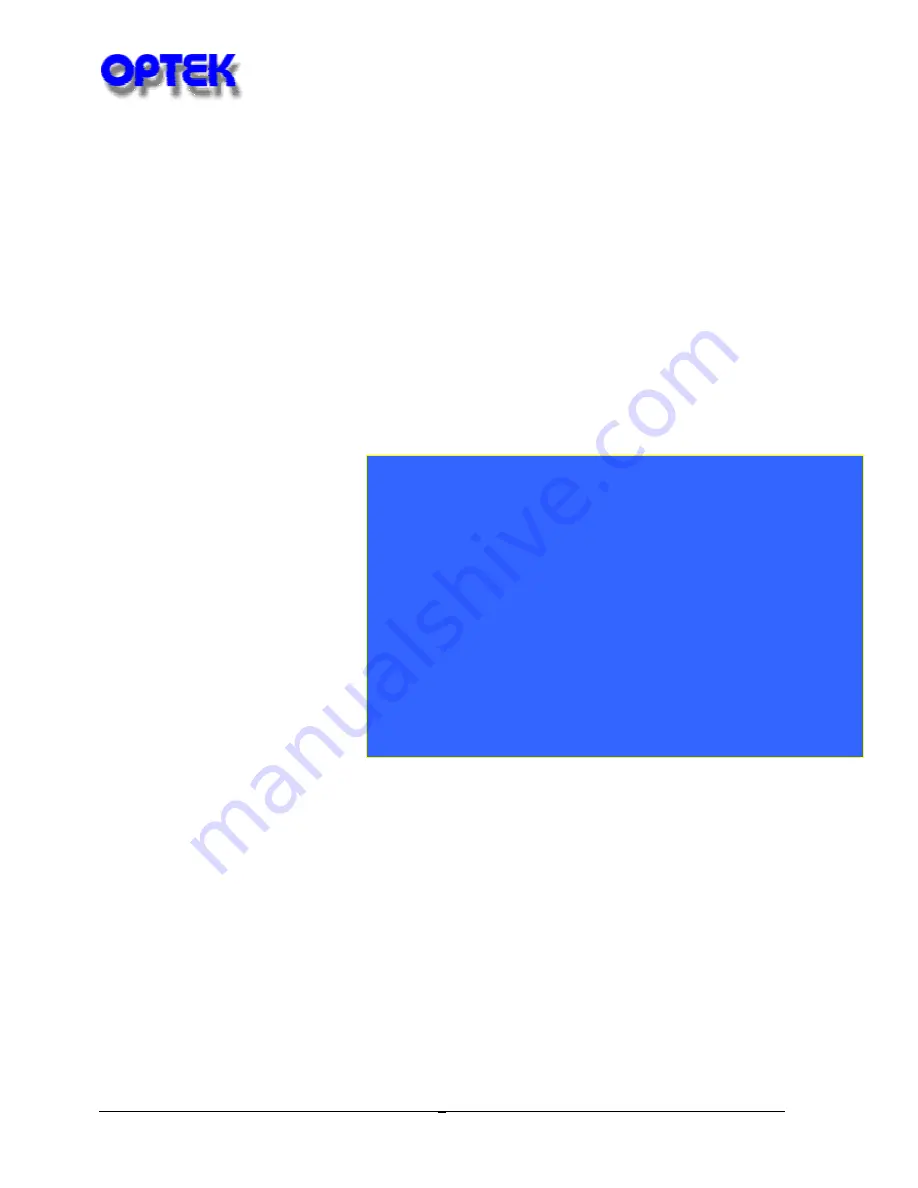
O P T E K
D P L - 2 4
4
Vacuum lamination of printed circuit boards has been utilized
for many years. But it was not until the development of the
DPL-24 that a system provided vacuum prior to the
application of positive pressure.
No pressure is applied to the product during the vacuum
dwell cycle. In this way maximum evacuation of air from
between the substrate and the laminate is assured.
During the pressure cycle a flexible diaphragm encapsulates
the product and true isostatic lamination is achieved. Unlike
roll laminators, the DPL–24’s diaphragm descends directly
towards the platen. No lateral stress is applied , hence less
distortion of the film can occur.
A Differential Pressure Laminator
INTRODUCTION
he DPL-24 Differential Pressure Laminator has been designed to give the
operator a superior method for laminating sheet supported emulsions such
as dry film solder mask, etc. Such materials can be applied to various
thicknesses and sizes of substrates. Experimentation is being done on alternative
uses for this device, among them, High Vacuum, Multi-Layer, Pressing of Printed
Circuit Boards and microBGA interconnects.
The substrate, prelaminated either manually, or utilizing the
A cold-roll lamination technique, is placed on the vulcanized rubber
platen mounted in the drawer
and positioned in the vacuum
chamber. Products of
differing thicknesses and
geometries can
be intermixed during a cycle if
adequate “hold-down”
techniques are employed.
The massive 1000 LB
chamber is constructed of
Ductile Iron and uses only
two o-rings. This design
ensures a positive seal for best
vacuum performance.
Utilizing a high quality, high volume 45 CFM, 3 horsepower, rotary
vane vacuum pump, an end point below two Torr is typically achieved.
T