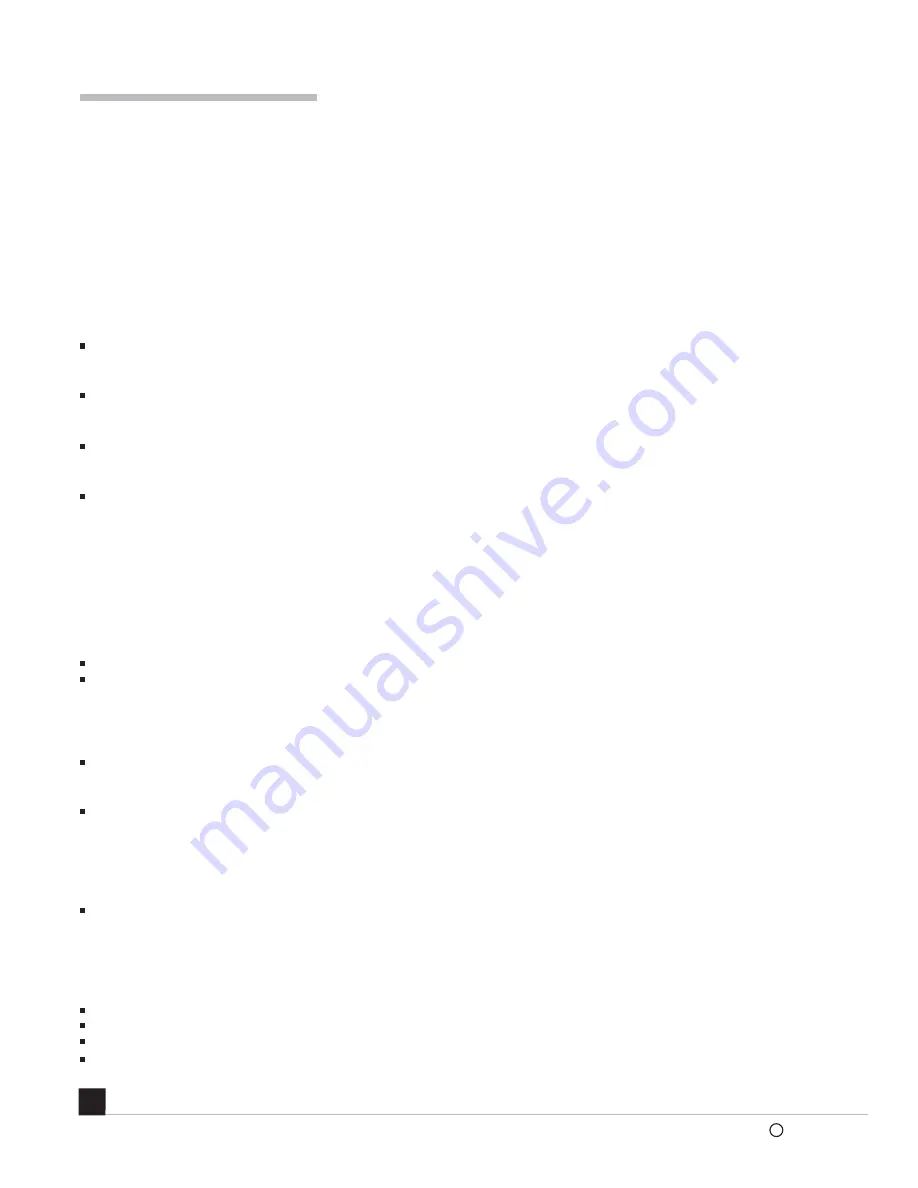
XI. Fire Hazards -
Read Before Installing and Operating
Do not use this product to collect other types of dust or flammable vapors.
Fire or explosion may occur!
Never collect sparks from a bench grinder into a wood dust collector.
Never introduce sparks or sources of ignition into the dust collector.
Personnel should keep at least 20 feet away from unit.
Check dust bin frequently and before leaving the shop for smoldering material.
Keep portable Fire Extinguishers handy.
The ABC type (dry chemical) is generally a good choice for small wood shops.
Additional information on portable extinguishers can be found in NFPA 10 (Standard for Portable Fire Extinguishers).
Be especially careful with sanding units. They can produce concentrations of dust in the combustible range. Make
certain enough air volume is at the suction point to capture all the particulate generated.
This high air volume will dilute the mixture below the lower limit of flammability. Be careful not to generate sparks into
the sanding dust.
Empty dust bin and clean filter often, especially when sanding.
Dont overload woodworking equipment, especially sanders. Excessive frictional heat can spontaneously ignite dust.
Sparks can be generated in several ways:
High-speed sanders and abrasive planers may strike foreign material
Saws and edgers may strike foreign material and create a red hot metal fragment.
Knots in hardwood can create frictional sparks.
Tramp metal when drawn into the collector can spark against ductwork.
Check wood stock for old nails and screws which can create red hot metal fragments.
Avoid using excessively large wood waste storage bins.
Always check storage bins for smoldering material before leaving for the day.
Electrically ground all equipment and ducting. Static sparks can ignite wood dust. (Avoid using PVC drainpipe)
Dont allow accumulation of layers of fine dust on horizontal surfaces. (Especially overhead lights, electrical boxes,
and fuse panels which can ignite dust)
Oneida Collectors are designed for WOOD DUST only!!
Wood shaping and cutting processes generate wood chips, shavings, and dust. These materials are considered
combustible. Air borne wood dust below 420 microns in size (.017 of an inch) in certain concentration ranges when
ignited can deflagrate (burn quickly).
An ignition source such as a spark, or ember, can ignite a dust mixture resulting in an expanding flame front, which
can cause an explosion if tightly contained. A disturbance that raises a cloud of accumulated fine dust can raise additional
dust clouds, which can cause a series of explosions that can level an entire building.
Until this type of fire has been
witnessed, it is difficult to believe the devastation. This type of fire is rare but worth safeguarding against.
The best way to avoid a wood shop fire is to keep the shop clean. A shop ankle deep in dust with layers of fine dust
everywhere is an accident waiting to happen. A good dust collection system reduces overall fire hazards but also adds
new concerns. A fire hazard is still present. Combustible material is now in the dust collector and storage container.
It is the buyers responsibility to follow all applicable federal, state, local, OSHA, NFPA, or authorities having
jurisdiction codes and regulations when installing and operating this dust collector.
Fire Marshalls may want the unit located outside of the building. If the collector is located inside the facility,
controls such as spark detection, suppression, or explosion venting may be required.
Most local jurisdictions consult or adopt NFPA ( National Fire Protection Agency) codes. However, other codes
may apply. Local codes may vary from jurisdiction to jurisdiction.
NFPA 664 Code book, Standard for the Prevention of Fires and Explosions in Wood Processing and Woodworking
Facilities, applies to woodworking operations that occupy areas of more than 5,000 sq. ft. or to areas where
dust producing equipment requires an aggregate dust collection flow rate of more than 1500 cfm (Cubic Feet
per Minute). This exempts some small operators from the NFPA code 664, but other codes may apply in your
jurisdiction. Consult your local Fire Marshall for help. Additional information can be found in NFPA Code Book
664.
The following points are worth heeding:
O.A.S. 2008
c
5 - 7.5 HP Direct Drive Owners Manual
The customer assumes the responsibility for contacting their insurance underwriter with regard to specific
application requirements of explosion venting or if additional fire protection and safety equipment may be
required.
14