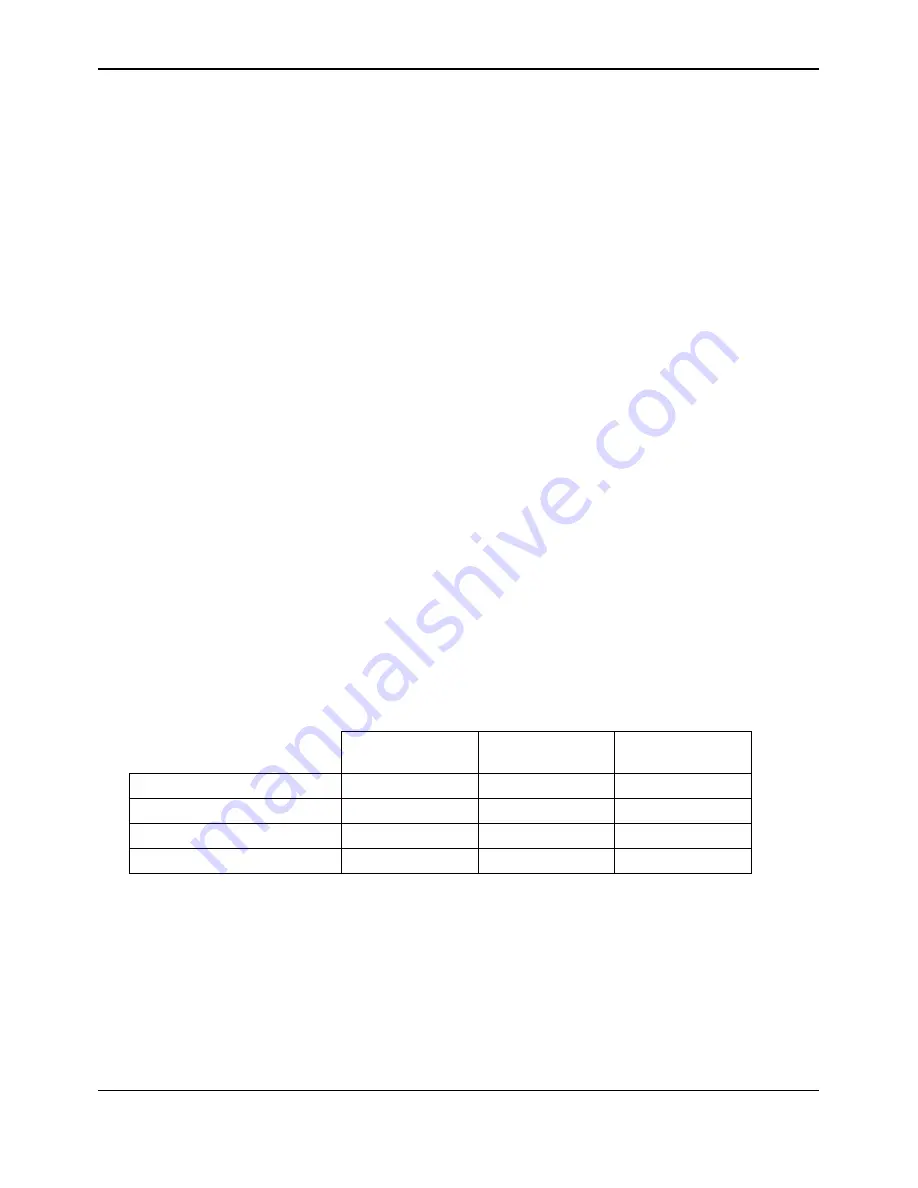
F3SP-U5P-TGR
User's manual
9
4 PRECAUTIONS AND INSTALLATION CRITERIA.
The safety products used must be suitable for the required application,
and other influences must be also taken into account such as a room
temperature, electromagnetic interference, intense light sources etc.
Please refer to the manual for specification or contact the manufacturer for
details.
4.1
CALCULATION OF THE MINIMUM INSTALLATION DISTANCE.
The safety distance ‘S’ must be sufficient to guarantee that the dangerous
area cannot be reached by the operator up to the moment in which the
machine with moving part stops. The safety distance must be calculated
according EN999 (European Standards. Safety of Machinery – The
positioning of protective equipment in respect of approach speeds of part
of the human body).
Using EN 999 formula:
S = ( K * T ) + C
S
= safety distance.
T
= T1 + T2
whereas T1 = machine response time in seconds.
T2 = unit response time in seconds including Safety sensor response time.
K
= 1600 mm/s (speed of the body approaching the dangerous area).
C
= additional distance depend on resolution of SLC and applicable standard.
1) Multiple separate beams (EN999, clause 6.1.4)
K = 1600 mm/s
C = 850 mm
Heights recommended
in EN999
4 Beams
3 Beams
2 Beams
Heights of 1
st
ray
300 mm
300 mm
400 mm
Heights of 2
nd
ray
600 mm
700 mm
900 mm
Heights of 3
rd
ray
900 mm
1100 mm
Heights of 4
th
ray
1200 mm
2) Single height beam (EN999, clause 6.1.5)
Where the risk assessment allows the use of a single beam, the following values can be used
K = 1600 mm/s
C = 1200 mm
The height of beam from the ground or reference plan: 750mm (EN 999)