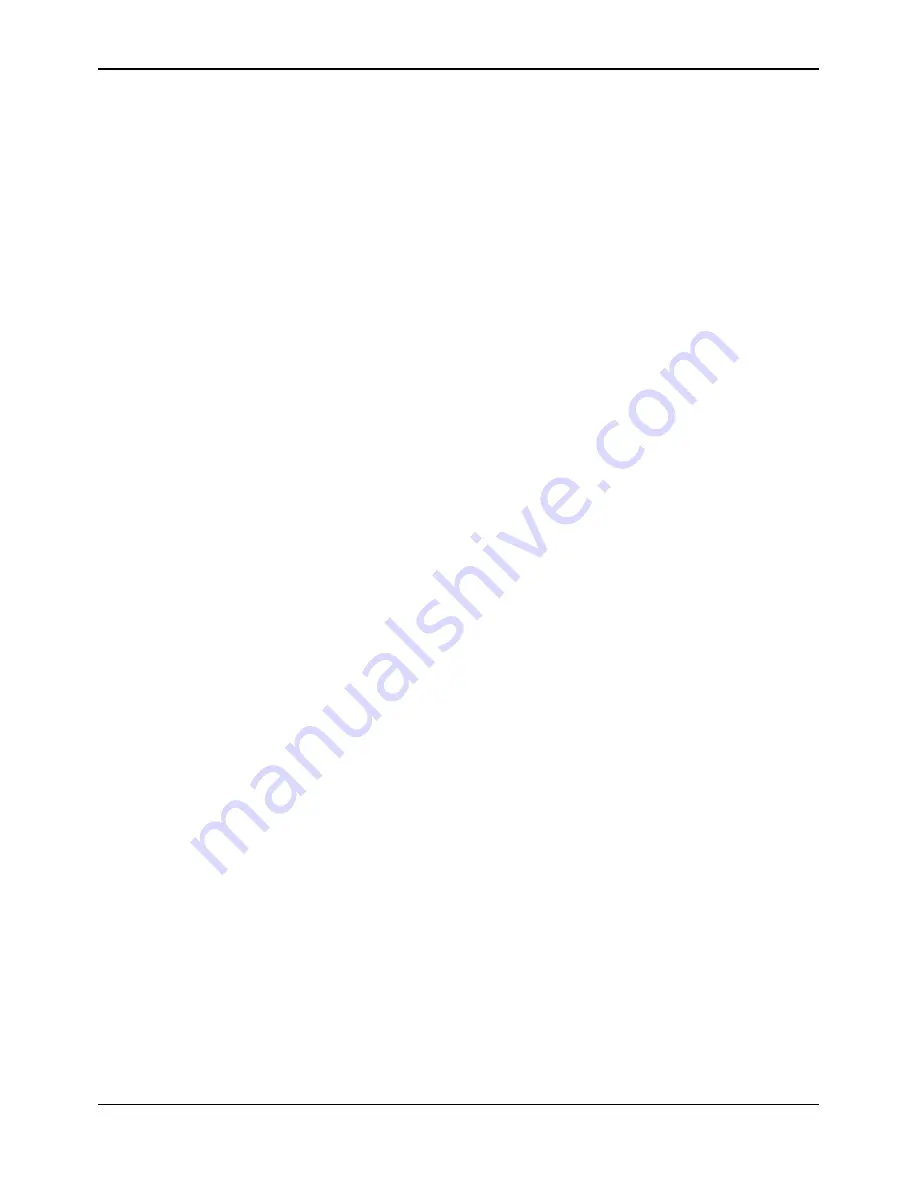
F3SP-U3P-TGR
User's manual
8
3 OPERATION.
The electronic control system of the device is made up of a microprocessor.
By means of the suitable hardware, it continuously control and check the
connected photocells. No interference among the photocells is possible as
they are controlled sequentially; it will be thus possible to install one or two
adjacent photocells. When one or more beams are interrupted, the electronic
system opens the outputs .
The photocells have been triggered are displayed by LEDs on the housing.
The control-unit can work in two different modes (please refer to par. 7 page
14) which he can carry out the following operations:
The two external buttons that have to be connected are for:
•
TEST : This is used to check if the whole system works effectively. By
pressing the TEST button (opening of the contact), this simulates the
interruption of one or more safety PESs. This operation makes the
machine stop, so the system checks can be made according to the
established time and modes. If pressed after a failure detection of the
unit (see the table error code), reset of the system is required.
•
RESET button: It is used to start the system, also for manual reset
condition after relay triggering or after an error which can be reset (see
table related to the error codes).
Two different operating modes are available:
1. Automatic reset: The system will start automatically after the beam
intrusion have been removed.
2. Manual reset: The system will remain in safe off condition until the
RESET button have been pressed. This manual reset allows to start
the system only on a wanted action of the user.
During the unit working, no operation set by the user interface involves
functions which can influence the system safety.
Summary of Contents for F3SP-U3P-TGR
Page 3: ......
Page 13: ...F3SP U3P TGR User s manual 12 5 2 PIN OVERVIEW ...
Page 27: ...F3SP U3P TGR User s manual 26 13 OVERALL DIMENSIONS Control unit F3SP U3P TGR ...
Page 28: ......