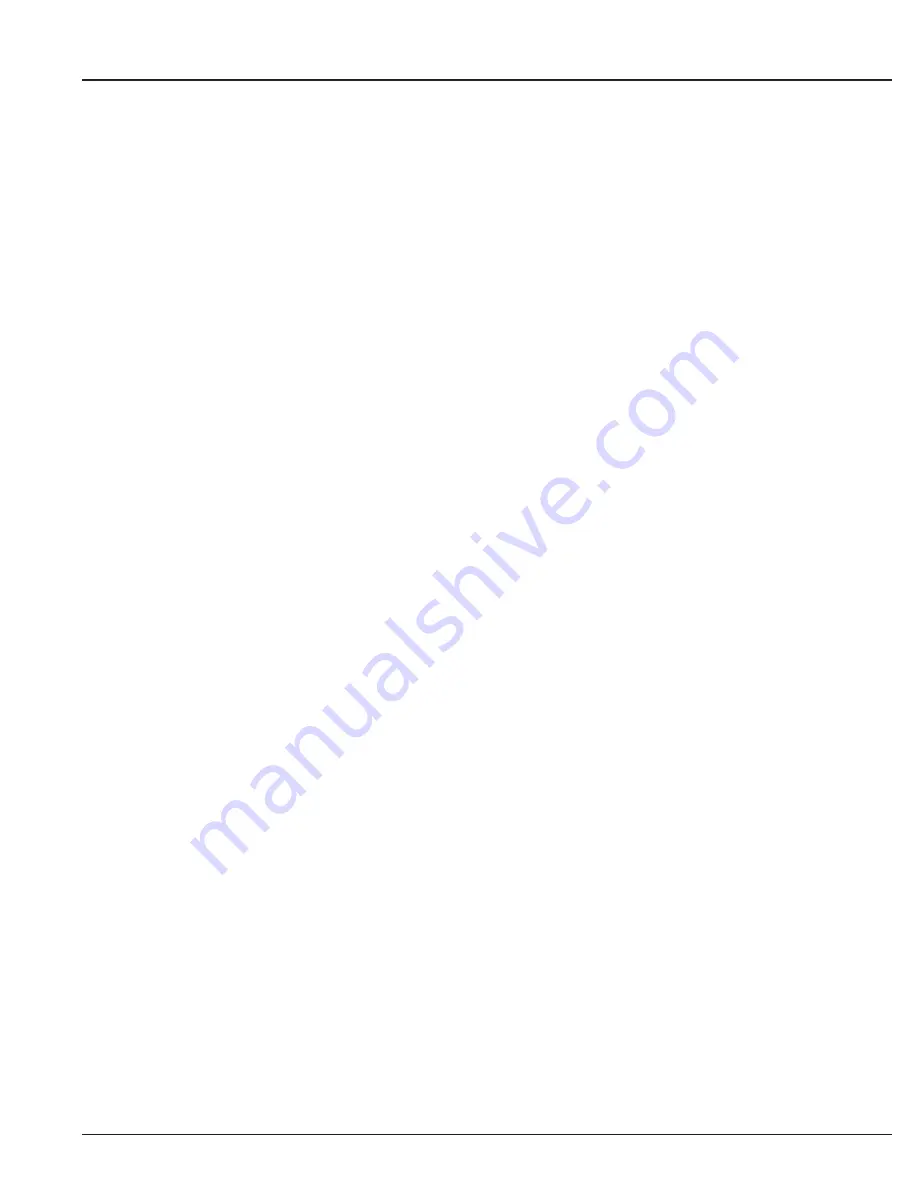
zipldr_setup&operations
www.OmniTurn.com
support@OmniTurn.com
(541) 332-7004
(541)-332-1018 fax
Fast... Precise... A
ff
ordable...
Zip Loader Setup & Operations
Omni
Turn
Page 17 of 44
Aligning the loader for Small Diameter Parts
See Page for 1/8” pushrod description (1/16” knife option)
When loading parts with diameters 5/16 and greater, the push-rod is fitted with a delrin push-
er which is the about the same diameter as the part, or a little smaller. Alignment is less crit-
cal because the push-rod doesn’t contact the ‘vee’: it is suspended between the adapter plate
(at the shuttle), and the pusher. The pusher rides in the vee to push the part into the liner.
Small diameter parts are 1/4” or less. For loading 1/4” parts or bars, use a 30-1/4” long push-
rod; for parts or bars down to about 3/16, turn down the end of the pusher to clear the collet
so part or remnant can be ejected. For smaller diameter parts, use a 3/16 or 1/8 pushrod. For
the 3/16 pushrod, put 4-40 holes in the pushrod at locations shown on page 14. Alignment is
very critical because the entire push-rod rests in the vee. For 1/8” pushrod, a different adapter
plate is required, and for parts less than 1/8” a different escapement knife may be necessary.
See page for more information about the various pushrods, including part numbers.
If the small diameter parts have sharp edge on face, it may be necessary to grind a small chamfer
inside the collet to insure reliable feeding. A die-grinder with a cone-shaped tool is adequate.
Speed of the pusher is also important, and the in-feed chamfer on the liner can be a factor.
Basic Alignment
The basic alignment procedure (as described on previous page) is to loosen the lock-knob
at left and lower the vee to bottom. Put 1-1/8” rod in the vee. Align the entire ziploader to
the drawtube with vee at lowest setting (bottom of pivot).
A 1-1/8” alignment rod ships with the loader. This rod is useful for setting the basic align-
ment, which is suitable for parts and bars 5/16 and greater. The vee stays on center for all
diameters because as vee is pivoted up, the center of different diameters passes through the
center of drawtube. The distance from the knife to the knee of the vee is adjusted for differ-
ent diameters by loosening the black knurled adjustment knobs on each side. The center of
each diameter should stay close enough to center of drawtube to load all diameters from 1”
to 5/16 by pivoting the tray. When loading smaller parts it gets much more critical.
Aligning the ‘ vee’ (rotating the chassis)
After the basic alignment is done, and the correct liner is installed, loosen the tray-lock knob
and micrometer lock knob, then use micrometer adjust to rotate the chassis until parts to
freely move from ‘vee’ into the liner. With the smallest parts it may be necessary to relocate
the entire loader side-to-side to get perfect alignment. To do this, it may be easier to loosen
the pivot braket tee nuts and nudge the chassis assembly.