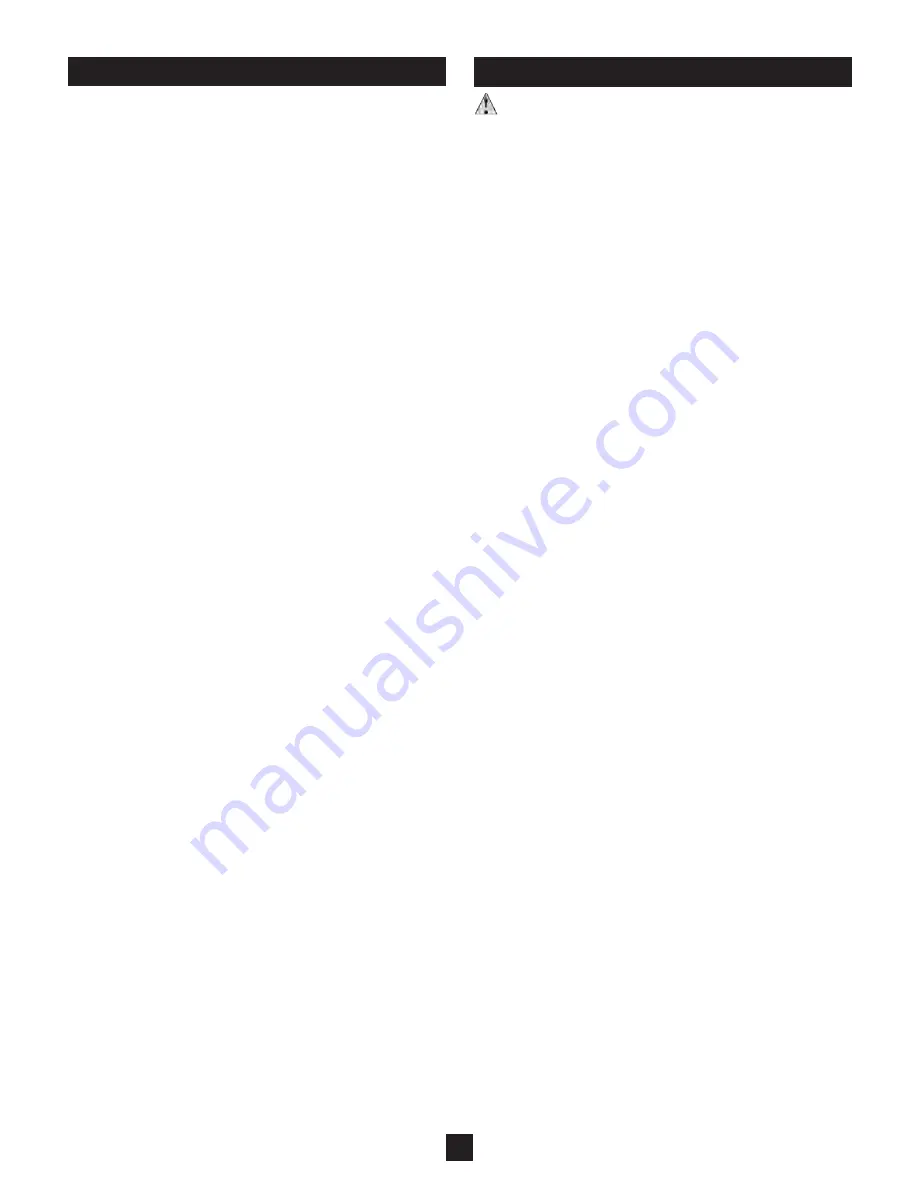
T R O U B L E S H O O T I N G
M A I N T E N A N C E
PROBLEM: Sensor will not sense material
CAUSE/SOLUTION:
1)
Verify power is applied to the sensor.
2)
Verify "Sense Adjust." Reposition adjustment clockwise
therefore making the probe more sensitive to "difficult to
sense" materials.
3)
Verify probe coverage when sensing is expected. The sen-
sor is not designed to be "tip sensitive." Permit significant
probe coverage before expecting material sensing.
4)
Verify electrical continuity between sensor housing and ves-
sel wall.
5)
Verify connection of the electronic module to the probe.
PROBLEM: Sensor remains in the "SENSE" mode even
when material is absent
CAUSE/SOLUTION:
1)
Verify the active probe is not in direct contact with any inter-
nal vessel structure. If so, reposition sensor.
2)
Verify "Sense Adjust" setting. Reposition adjustment
counter-clockwise therefore making the probe less sensitive
to "easy to sense" materials.
3)
Verify there is not a large buildup of material between the
active probe and the probe housing. See "Cleaning" in the
"Maintenance" section of this bulletin.
PROBLEM: Sensor does not seem to hold its calibration
CAUSE/SOLUTION:
1)
Verify that the "sense adjust" is positioned at ideal point as
described in 2-Step Calibration procedure. Placing setting
too close to threshold can create nuisance false signals.
2)
Maximize probe coverage of material being sensed.
"Difficult to detect" materials (i.e. low dielectric or light mate-
rials) are more easily detected when more probe is covered.
Avoid setups where "probe tip sensitivity" is required.
3)
Insure electrical continuity between the probe's mounting
point (3/4" NPT or 1 1-4" NPT) and the bin wall. Sealant
tapes (i.e. Teflon tape) can electrically isolate these regions
and make sensing more difficult.
4)
Assess the temperature swing that the electronics sees in
application. Applications with "difficult to detect" materials
and that experience a wide temperature swing are the most
vulnerable. Consult factory for support.
PROBLEM: Output contacts perform opposite of
designations (N/O, N/C)
CAUSE/SOLUTION:
1)
Designations on PCB relate to relay status when in "Fail-
Safe Low" mode and when no material is sensed. If "Fail-
safe High" mode is used, the designations are reversed.
Swap wire terminations of N/O and N/C if necessary.
Changing the fail-safe selection is not recommended.
Fuse Replacement:
The fuse incorporated into the LV800 PCB is not intended for
operator replacement. A qualified technician can replace the
applicable fuse according to the following specifications. If nec-
essary, consult the factory for additional technical assistance or
for return of the LV800.
115VAC
F1: 5x20mm, 0.63A Time Lag (Slo-Blo), 250VAC
Littelfuse:
#218.063
Bussman:
#GDC-63mA
230VAC
F1: 5x20mm, 0.32A Time Lag (Slo-Blo), 250VAC
Littelfuse:
#218.032
Bussman:
#GDC-32mA
Preventive Maintenance:
The LV800 design is virtually maintenance free. In typical
applications, once the sensor is properly calibrated, it will oper-
ate without any further attention. In abrasive applications,
probe condition should be periodically observed. Although the
probe's construction is made with high quality engineering plas-
tics, heavy abrasion can wear away the probe's insulators. This
can influence the calibration and eventually lead to sensor fail-
ure. The electronics are housed in a weatherproof enclosure.
In addition the PCBs are conformal coated with a silicone-
based material to further prevent electrical influence by con-
densation. The sensor electronics should periodically be
observed for any signs of contamination caused by improper
enclosure protection (i.e. insure cover is fully engaged, and that
wire entries are properly sealed.)
Cleaning Requirements:
Environmental and hazardous location protection is highly
dependent on the proper installation of the cover to the hous-
ing. A lubricant is applied to the housing/cover threads to
enhance ability to twist-on twist-off cover. Clean and re-lubri-
cate threads if necessary to insure trouble-free operation. Do
not physically alter threads in anyway otherwise environmental
or hazardous location protection could be compromised.
The driven shield feature of the LV800 is designed to minimize
the need for cleaning the probe portion of the sensor. In appli-
cations where material build-up is so excessive that electronics
can not adequately compensate, probe cleaning may be nec-
essary. If so, wipe the probe with a clean damp cloth from the
housing to the probe tip.
7