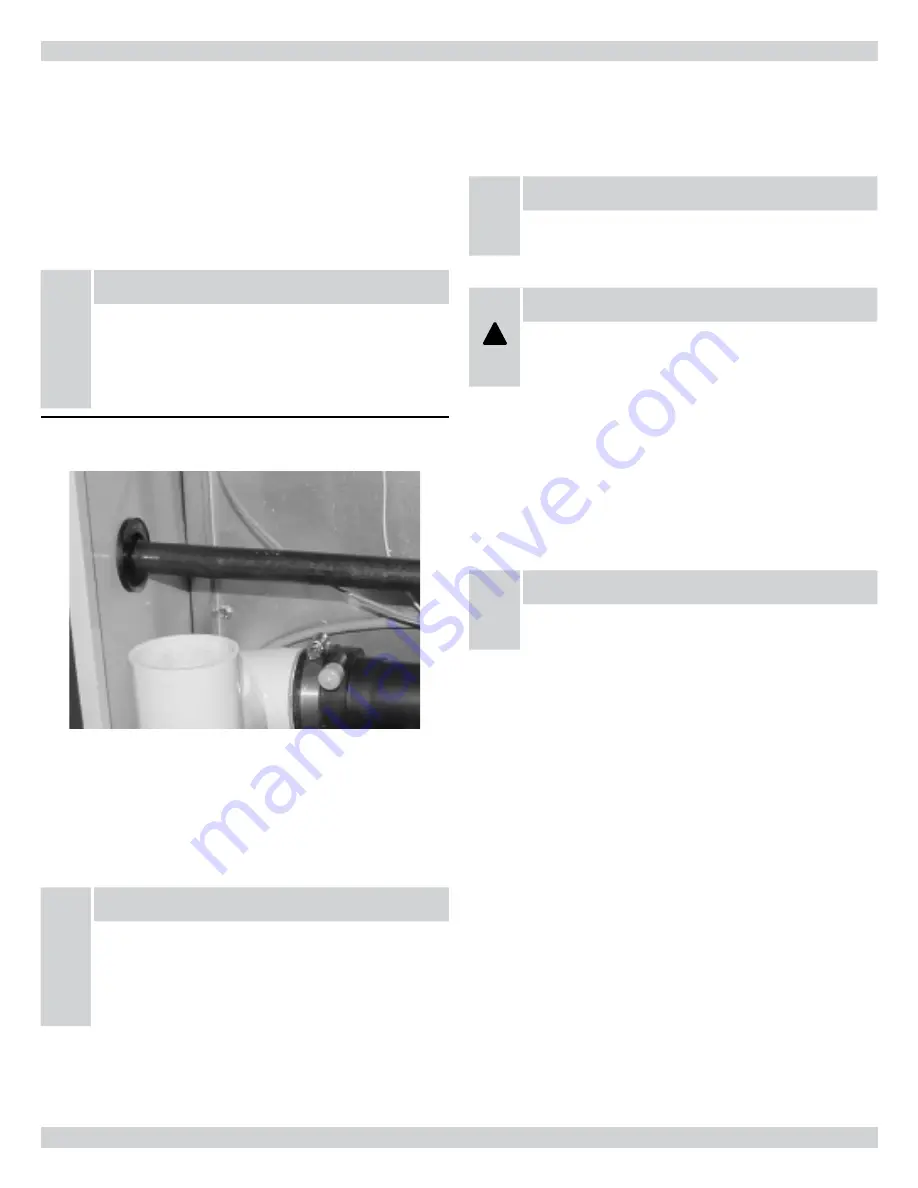
17 - GAS SUPPLY AND PIPING
Gas Piping
In Canada, the gas piping should be installed in accordance with
CAN/CGA-B149.1 and 2, and in accordance with any local codes.
In the United States, the gas piping should be installed in accordance
with NFPA 54 / ANSI Z223.1 and any local codes.
If local codes allow the use of a fl exible gas appliance connector,
always use a new listed connector. Do not use a connector, which has
previously serviced another gas appliance.
NOTICE
IMPORTANT: To maintain a good seal in the burner area,
the gas piping through the side panel into the furnace
must be ½” A53 black iron pipe. Th
e pipe passes through
a special rubber grommet that is custom manufactured to
seal tightly around the gas pipe.
Figure 28 - Furnace Gas Pipe Connections (Note Rubber
Grommet)
Th
e gas piping may enter the furnace from either side. Once the
routing of the gas pipe is determined, select and remove the appli-
cable knockout and install the grommet within the hole.
Install a BMI ground joint union between the gas valve and the side
panel to allow easy removal of the burner for service purposes.
NOTICE
IMPORTANT: Always use a backup wrench to prevent
twisting of the control assembly and gas valve. Any strains
on the gas valve can aff ect positioning of the orifi ces
relative to the burners. Th
is could result in faulty burner
operation.
Install a manual gas shut-off valve and dirt pocket as close to the
furnace as possible. Some local codes call for the manual gas shut-off
valve to be located between 4 to 5 feet above fl oor level to prevent
tampering by small children. Ensure that the valve is readily acces-
sible.
NOTICE
IMPORTANT: Ensure that the manual shut-off valve and
gas valve are not subjected to high pressures.
!
WARNING
Indicates an imminently hazardous situation which, if not
avoided, may result in death, serious injury or substantial
property damage.
Gas Inlet Pressure
Th
e natural gas inlet supply pressure should be 5” to 7” w.c. (7” w.c.
recommended). Th
e LP gas inlet supply pressure should be 11” to
14” w.c. (12” w.c. recommended). Th
ese pressures must be main-
tained while all other gas fi red appliances are operating at maximum
conditions.
NOTICE
IMPORTANT: Do not exceed 14” w.c. inlet pressure with
either fuel.
Th
e gas valve has two adjustable internal
regulators for controlling burner manifold pressure. Burner mani-
fold high fi re and low fi re pressures are listed on the furnace rating
plate.
Leak Testing
All new gas piping installations should be pressure tested as specifi ed
by CAN/CGA-B149.1 & 2, or NFPA 54 ANSI Z223.1 or ANSI/NFPA
58, “Standard for the Storage and Handling of Liquefi ed Petroleum
Gases.”
Gas piping that has not been pressure tested, from the manual
shut-off valve to the furnace gas valve for example, should be leak
tested using an electronic combustible gas detector, a commercially
prepared leak detector, or other locally approved method. A leak
detector solution can be prepared by mixing a small quantity of dish
detergent with water and daubing it onto the gas piping, especially
the joints.
35